Sandblasting machine a kind of machine that uses compressed air as the power to form a high-speed jet beam that sprays high-speed jet feed onto the workpiece surface so that the outer surface mechanical properties change.
Second, the sandblasting machine classification structure
1) Suction dry sandblasting machine
General composition
A complete suction type dry blasting machine is generally composed by six systems which are structural systems, media power systems, piping systems, dust removal systems, control systems and media systems.
How it works?
The suction type dry sandblasting machine get power trough compressing air. The negative pressure that made trough high-speed movement of the airflow in the gun, then via the sand tube into the spray gun and spray the abrasive to the surface to be processed, to achieve the desired processing purposes. The suction type dry sandblasting machine is both the power for the jet and also the acceleration power.
2) Press-in dry sandblasting machine
For the press-in dry blasting machine, we mainly introduce the press-in blasting working unit which is the basic working unit composed of the pressure tank and spray gun.
General composition
A complete press-in dry blasting machine work unit is generally composed of four systems: pressure tank, medium power system, pipeline system and control system.
How it works?
Pressing dry sandblasting machine uses compressed air as power, using the working pressure that established in the pressure tank. Then spray the abrasive through the sand valve into the injection nozzle and spray onto the surface that to be processed to achieve the desired processing purposes. In the press-in dry sandblasting machine, the compressed air is both the power supply and jet acceleration power.
The pressing dry sandblasting machine uses grinding fluid pump as its feeding power, through which the machine puts the mixing grinding fluid(mixture of abrasive and water) into the spray gun. Then, gets the acceleration power through pressing air tank to establish the working pressure, the abrasive through the sand valve into the sand injection and injection nozzle, spray to the surface to be processed to achieve the desired Processing purposes. In the press-in dry sandblasting machine, the compressed air is the power supply and jet acceleration power.
3) Liquid sandblasting machine
Liquid sandblasting machines, relatively to the dry blasting machine, the best feature is a good prevent control of the blasting process from dust pollution and improve the the sandblasting operation working environment. Following is the structure and its working principle.
General composition
A complete liquid sandblasting machine generally consists of five systems: structural systems, media power systems, piping systems, control systems and auxiliary systems.
How it works
The Liquid sandblasting machine’s power supply is from the grinding fluid. The grinding fluid(abrasive and water mixture) is delivered to the gun through the grinding pump. Compress air as the grinding fluid acceleration power, goes through the air pipe into the gun, in which, the compressed air enters the gun inject through the nozzle, and sprays onto the machined surface to achieve the desired processing purposes. In the liquid sand-blasting machine, the grinding liquid pump is the power supply and compressed air is the accelerate power.
4) Frozen sandblasting machine
Frozen sandblasting theory originated in the 1970s in Europe and America. Then, the Showa Carbon Co., Ltd. from Japan found that the device is mainly used to replace deburring treatment for the hand-rubber molded parts, precision injection molding and die casting products.
Frozen sandblasting machines, known as the automatic jet-type frozen trimmer, This equipment from the late 1970s had been widely used in developed countries. China began to gradually promote them after 2000 and then become one of the necessary post-process equipment.
How it works
Rubber and plastic alloy materials belong to the polymer material, which at different temperatures will be in different phase, and from the phase point of view, the material changes only at the mechanical states. The material changes in low temperature conditions. When return to normal temperature conditions, the performance will be restored.
Frozen sandblasting machines use liquid nitrogen low-temperature freezing effect to embrittle the rubber and plastics alloy. At this time, the embrittlement on the edges occurs in advance of the product. During the time difference, through a high-speed jet shoot polymer particles to impact products to remove the burs of plastic alloy products and aluminum, zinc alloy products.
Comparison of Plasticized-powder Extrusion and Metal Powder Injection Molding
Today, powder metallurgy technology has developed a lot of branches and different processes, in which two most representatives are plasticized-powder extrusion and MIM. Although both belong to powder metallurgy, they are quite different.
First, plasticized-powder extrusion process is a development of metal powder coated extrusion process, at low temperature, squeezing excellent mobility copper, tungsten , cemented carbide, high melting point inter-metallic compounds and ceramic materials. Nowadays, it has a dedicated continuous extrusion equipment. The material used in this process is a metal powder with excellent flowability adding with a certain amount of the accelerating agent. The blank produced by this process can be finished after drying and sintering.
Let us take a look at another new type of metal parts forming process – MIM. It is a combination of traditional powder metallurgy and modern plastic injection molding technology. It relies on the binder formulation research and development, and feed production technology. It has a long but slow development history. The basic process is first to mix the metal powder and binder a certain temperature and pressure conditions into a specific mold, and then degrease the binder, sintered the blank to get a certain mechanical properties.
Through the above description we can see that plasticized-powder extrusion and MIM have lots of same advantages. So in recent years, these two processes have a rapid development. They have following four same advantages: 1, near-net-shape forming; 2, can be formed as the final product shape by the first time; 3, hard to be used by CNC machining and other technologies, specially for small and complex parts and elongated parts; 4, the scope of materials application is quite extensive. The two processes can be used as new materials and new R & D methods.
A common feature of both is the use of adhesives. From the selection of adhesives and formulations point of view, their binder can be classified as three major systems: wax, methyl cellulose and plastic base. The use amount is about 8% to 20 % of total material ratio. From the process point of view, both must remove the adhesive after the products are formed.
But the two are also obviously different. As to the raw materials, plasticized-powder extrusion metal powder particles have big size range, from a few microns to hundreds of microns. Relatively, MIM has higher metal powder requirements. The powder particle size is generally between 0.5-20 microns, and higher requirements on the powder preparation method and the shape. So after forming, the product is more compact, smaller sintering shrinkage, and higher dimensional accuracy.
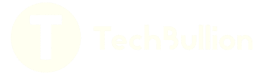