Imagine a world where your smartphone stops working after just a few months or a high-tech medical device fails during a critical procedure. These situations highlight the importance of durable, reliable materials in modern electronics—materials that must endure extreme conditions while delivering peak performance. But how do manufacturers verify that these materials meet the necessary standards? This is where microhardness testing steps in.
With electronic devices becoming smaller, faster, and more powerful, materials used in their construction face unprecedented challenges. Every microchip, sensor, and circuit board needs to withstand mechanical and thermal stresses without compromising functionality. Microhardness testing offers a solution by analyzing materials’ mechanical properties at a microscopic scale, providing assurance that they are up to the task.
By measuring key attributes like hardness, uniformity, and wear resistance, microhardness testing has become an integral part in advanced electronics production. Without it, manufacturers risk costly failures, compromised reliability, and shortened product lifespans. It’s not just about testing materials; it’s about protecting the technologies that power our daily lives.
Understanding Microhardness Testing in Electronics
Microhardness testing measures a material’s resistance to deformation under a small applied load, providing detailed information about its structural integrity. The process is particularly valuable for assessing thin materials, coatings, and microstructures, which are common in advanced electronics. By using precise indentation techniques, microhardness testing reveals not only a material’s hardness but also its homogeneity and resistance to wear.
The two primary methods of microhardness testing—Vickers and Knoop—are indispensable in the electronics industry. The Vickers test uses a diamond-shaped indenter to create a measurable indentation, which is suitable for evaluating uniformity in materials like thin films and coatings. On the other hand, the Knoop test, with its elongated diamond-shaped indenter, is better suited to ultra-thin layers, such as those found in semiconductors and sensors, as it minimizes penetration depth.
Take, for instance, microhardness testing in semiconductor manufacturing. Silicon wafers, the building blocks of microchips, require exacting hardness properties to withstand fabrication and prolonged use. Even a slight deviation in hardness could compromise chip performance or lead to premature failure. Similarly, microhardness testing is vital for guaranteeing that copper interconnects within circuit boards maintain the structural integrity needed for consistent electrical performance.
Applications of Microhardness Testing in Electronics
Microhardness testing serves as a useful tool in a number of sectors of electronics manufacturing. Below are 3 key areas where microhardness testing is highly beneficial.
Semiconductor Manufacturing
Semiconductors are the heart of modern electronics, found in everything from smartphones to medical devices. Semiconductors’ performance and reliability depend heavily on their materials, especially silicon wafers. Microhardness testing guarantees consistent hardness, which is extremely important during chip fabrication. A minor hardness flaw can lead to cracking or warping, compromising the entire production process. As an example, advanced chips used in high-speed processors must endure thermal cycling and mechanical stresses—conditions that demand flawless material properties.
Microhardness testing also extends to evaluating interconnect materials like copper and aluminum, which form the pathways for electrical signals within chips. Making sure these pathways retain structural integrity under continuous electrical load is paramount to maintaining device performance over time.
Printed Circuit Boards (PCBs)
Printed circuit boards are the backbone of electronic devices, connecting various components to ensure functionality. PCBs are exposed to repeated thermal and mechanical stresses during manufacturing, soldering, and operation. Microhardness testing is a necessary step for verifying copper layers and solder joints durability. For instance, solder joints act as the glue that holds components together; any weakness in their hardness can lead to failure during thermal expansion or contraction.
Manufacturers also rely on microhardness testing to assess protective coatings applied to PCBs. These coatings shield the boards from environmental factors like humidity and corrosion. By verifying the hardness of these layers, microhardness testing extends the lifespan of electronic devices used in critical fields such as aerospace and automotive.
Thin Film Coatings
Thin films are indispensable in advanced electronics, used in applications ranging from sensors to touchscreen displays. These films must exhibit exceptional hardness to withstand constant use and environmental wear. For instance, touchscreen coatings on smartphones are subjected to scratches, impacts, and temperature variations. Microhardness testing evaluates the wear resistance of these films, assuring that they maintain clarity and responsiveness over time.
Another vital application is in microelectromechanical systems (MEMS), which are miniature devices used in applications like accelerometers and gyroscopes. MEMS devices must combine durability and precision to function reliably in dynamic environments. By using microhardness testing, manufacturers can validate these properties, reducing the risk of device failure in high-stakes scenarios like automotive safety systems.
The Importance of Quality Equipment in Microhardness Testing
Microhardness testing accuracy and reliability depend heavily on the quality of the equipment used. In advanced electronics, where even minor material discrepancies can lead to significant failures, investing in state-of-the-art testing devices is non-negotiable.
Precision and Accuracy: High-end microhardness testers offer exceptional precision, measuring indentations with sub-micron accuracy. By way of example, automated systems equipped with advanced imaging technologies ensure consistent results, critical for applications like thin-film evaluation.
- Efficiency and Automation: Modern microhardness testing devices often include automated features, allowing manufacturers to test multiple samples quickly and efficiently. This is particularly useful in high-volume production environments, where time is as valuable as accuracy.
- Adherence to Standards: Equipment designed to comply with international standards such as ASTM E384 guarantees that test results are consistent and widely accepted across global supply chains. This compliance is essential for maintaining trust and collaboration in industries that rely on advanced electronics.
- Real-World Example: In 2023, a leading electronics manufacturer reported a 20% improvement in production efficiency after upgrading to an automated microhardness testing system. This reduced production costs and boosted product reliability, boosting customer satisfaction.
Achieving Reliability Through Microhardness Testing
Microhardness testing has proven itself to be a key process in advanced electronics. Its ability to measure critical attributes such as hardness, uniformity, and wear resistance makes sure that materials meet the demanding standards required in today’s high-tech devices. Whether safeguarding semiconductor performance, enhancing PCB durability, or validating thin-film coating resilience, microhardness testing underpins the reliability of modern electronics.
As electronic devices shrink in size and grow in complexity, materials face challenges. By investing in precise, automated, and standards-compliant microhardness testing equipment, manufacturers can maintain the highest levels of quality and performance. Ultimately, microhardness testing is more than a quality control measure—it is a guarantee of durability and innovation, securing the technologies that shape our daily lives.
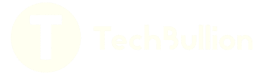