Things that injection molding inc should pay attention to during processing
- Seat rows must have status. Positioning methods include slingshots, beads, standard row clips, etc., which must be detailed according to various requirements. The row seats must have beading to ensure wear resistance. Wear-resistant materials must be used for layering and wear-resistant plates, and oil grooves must be added.
- Pay attention to the maintenance of the surface of the embryo to avoid rust or scratches during the production process. Before mold packaging, the inner mold should be sprayed with white/colorless rust inhibitor, rinse the entire mold surface, and then apply butter.
- The mold must have no sharp corners and must be chamfered. Except for specially designated places. The diameter of the positioning ring should match the engineering drawing, and the continuous form and position of the ejector pin should match the engineering drawing.
- The mold should be equipped with side locks (straight locks) on four sides. If the side lock cannot be installed, a taper lock or taper lock will need to be installed. Tapered locks should be installed transversely.
- All internal mold material and model level requirements must be purchased according to the technical requirements formally confirmed during the order or design review process. Material certification must be provided, and if it is a hard mold, a heat treatment report must be provided.
- General structure molds must place pillars with both ends flat. Small molds require 0.1 mm, and large preloads of 0.1 mm-0.15 mm.
- The mold embryo guide cover needs to be processed with an exhaust groove to prevent the guide belt from growing. Try to avoid using a grinder to grind the mold. If you don’t want to use a grinder, you must use a whetstone to save light (especially the disc surface).
- The lift seat must be made of wear-resistant hard material. Sloping roof requires processing of oil tanks. Sloping roofs should usually be hardened to HRC 40-45 degrees with 2510 or CR12. The inclined roof is subject to impact loads, so it cannot be too hard. Otherwise, it will break and chamfer the C corner at all orthogonal positions.
- All screws and mold accessories require basic content, and the screw heads cannot be sawed. The effective locking length of the screw must be sufficient. In fact, dust explosion is a process in which dust reaches a certain density in the air and reaches above the lower explosion limit. The ignition source burns instantly to produce high temperature. The mixed gas generated after burning in a limited space rapidly expands, the pressure increases, and sound is generated.
The following defects may be encountered during the injection molding process:
- Characteristics of defects in injection molded parts: The injection molding process is incomplete because the mold cavity is not filled with plastic or the injection molding process lacks certain details.
- Reasons for possible problems: (1) Insufficient injection speed. (2). Plastic material shortage (3). There is no screw gasket left at the end of the screw regeneration process. (4).Change of running time. (5). The temperature of the injection cylinder is too low. (6).Insufficient injection pressure. (7). The nozzle is partially blocked. (8). The heater outside the nozzle or injection cylinder cannot operate. (9).The injection molding time is too short. (10). Plastic is attached to the throat wall of the hopper. (11). The capacity of the injection molding machine is too small (ie, injection weight or plasticizing capacity). (12). The mold temperature is too low. (13). There is no anti-rust oil to clean the mold. (14). The anti-return ring is damaged and the melt has backflow.
- Management skills: (1). Increase injection speed. (2). Check the amount of plastic in the hopper. (3). Check whether the injection route is set correctly and change it if necessary. (4). Check whether the check valve is worn or cracked. (5). Check whether the inspection operation is stable. (6). Increase the melt temperature. (7). Increase back pressure. (8). Increase injection speed. (9). Check the nozzle hole for foreign matter or unplasticized plastic. (10). Check the outer surface of all heaters and use an ammeter to check whether the energy output is correct. (11). Increase the screw forward time. (12). Increase the cooling capacity of the hopper throat area, or reduce the temperature of the rear area of the injection cylinder. (13). Use a larger injection molding machine. (14). Properly increase the mold temperature. (15). Clean and clean the anti-rust agent in the mold. (16). Check or replace the backstop ring.
Differences in size of injection molded parts: 1. Characteristics of the defects of injection molded parts: The change in weight and size during the injection molding process exceeds the production capacity of the mold, injection molding machine, and plastic combination. 2. Reasons for possible problems: (1). The plastic input into the injection cylinder is uneven. (2). The temperature or fluctuation range of the injection cylinder is too large. (3). The capacity of the injection molding machine is too small. (4). The injection pressure is not stable. (5). The screw reset is not firm. (6). Changes in operating time and inconsistent solution viscosity. (7). The injection speed (flow control) is not stable. (8).A type of plastic that is not suitable for the mold is used. (9). Consider the impact of mold temperature, injection pressure, speed, time and holding pressure on the product.
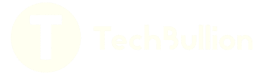