In recent years, metal 3D printing has revolutionized industries ranging from aerospace to healthcare by enabling the production of highly complex, customized parts with precision and speed. Among the various additive manufacturing methods, Selective Laser Melting (SLM) and Direct Metal Laser Sintering (DMLS) are two of the most prominent techniques for metal 3D printing. Although they share many similarities, subtle differences between them define their respective applications and capabilities. This article delves into the inner workings of these technologies, their characteristics, and the ultimate benefits they offer to manufacturers and engineers.
How Metal 3D Printing Works
At its core, both SLM and DMLS employ a laser to fuse fine metal powders into solid objects. The process begins by spreading a thin layer of metal powder across the build platform, which is contained in a sealed chamber filled with inert gas (like argon) to prevent oxidation. A high-powered laser then scans the cross-section of the part, melting or sintering the powder particles, bonding them together layer by layer. After each layer is completed, the platform moves down by one layer thickness, and the process repeats until the part is fully formed.
The two methods differ in the nature of the metal powders they use. SLM exclusively uses pure metals with a single melting point, fully melting the particles during the printing process. On the other hand, DMLS utilizes metal alloys with multiple constituents and varying melting points, which sinter together at the molecular level. This fundamental difference means that SLM is typically used for single-metal parts, whereas DMLS is ideal for alloy-based components.
Key Differences: SLM vs. DMLS
While both SLM and DMLS are used for producing high-performance, end-use metal parts, the materials they can work with differ significantly. SLM is most suitable for pure metals such as aluminum, titanium, and stainless steel, whereas DMLS can process a broader range of metal alloys, including complex combinations like cobalt-chrome and Inconel. This makes DMLS more versatile for applications requiring high-performance materials, such as in aerospace and medical devices.
Furthermore, the metal powder used in these processes also influences the mechanical properties of the finished parts. SLM-produced parts tend to have more uniform properties due to the use of a single metal, while DMLS parts benefit from the enhanced characteristics provided by metal alloys, such as improved strength and resistance to heat.
Materials and Applications
The material selection in metal 3D printing is crucial for the end part’s performance. SLM and DMLS can print using a wide array of metals, including:
- Aluminum alloys: Known for their low density and good thermal properties, often used in automotive and aerospace industries.
- Titanium alloys: Valued for their corrosion resistance and strength-to-weight ratio, making them ideal for aerospace and medical applications.
- Stainless steel and tool steels: Offering high wear resistance and hardness, they are widely used in tooling and machinery.
- Cobalt-chrome and Inconel: Superalloys that perform well at high temperatures, commonly used in turbine engines and other extreme environments.
These materials, particularly the high-strength alloys, are difficult to process with traditional manufacturing methods, making metal 3D printing an essential technology for industries that demand precision and specialized materials.
Design Flexibility and Precision
One of the greatest advantages of metal 3D printing is its ability to create complex geometries that traditional manufacturing methods struggle with. With SLM and DMLS, engineers can design parts with intricate internal structures, lattice patterns, and organic shapes that would be impossible to produce using conventional subtractive methods.
However, the technology does come with limitations. For instance, metal 3D printing requires the use of support structures, which help to anchor the part to the build plate and prevent warping during the high-temperature process. These supports must be removed post-printing, and their presence can add to material waste and post-processing costs. Optimizing the design to minimize the need for supports is crucial to reduce the overall cost of production.
Post-Processing and Surface Finishing
After the part is printed, several post-processing steps are typically required. These include the removal of excess powder, the detachment of support structures, and heat treatment to relieve internal stresses and enhance mechanical properties. For parts that require precision, CNC machining may be used to refine features like holes or threads. Surface finishing techniques such as polishing, media blasting, and metal plating are also common to improve the part’s surface quality and fatigue strength.
The post-processing stage is often one of the most time-consuming and expensive parts of the 3D printing process, but it is essential for achieving the desired final properties.
The Ultimate Benefits and Challenges of Metal 3D Printing
Metal 3D printing offers several significant advantages:
- Complexity without extra cost: Traditional manufacturing methods often struggle with intricate designs, but metal 3D printing allows engineers to create highly complex parts without increasing production costs.
- Customization: This technology is ideal for low-volume, highly customized parts, making it especially valuable in industries such as medical implants, aerospace, and defense.
- Reduced material waste: Unlike subtractive manufacturing, which cuts away material, additive manufacturing only uses the material needed for the part, resulting in less waste.
However, the technology is not without its challenges. The high cost of metal powders, as well as the need for post-processing, can make metal 3D printing expensive. Moreover, the build size of the printers is still limited, and designs may need to be optimized for the specific capabilities of the technology.
Conclusion
Metal 3D printing, through methods like SLM and DMLS, represents a revolutionary shift in manufacturing. These technologies allow for the creation of parts with complex geometries, superior material properties, and the ability to customize components for specific applications. Although high costs and design restrictions remain, the ultimate potential for metal 3D printing in industries like aerospace, automotive, and healthcare is vast. As these technologies continue to evolve, they will undoubtedly play an increasingly important role in the future of manufacturing.
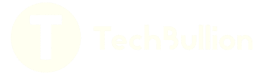