In the chemical, manufacturing, and engineering sectors, energy efficiency is a critical consideration. Rising energy costs, increasing regulatory pressures, and the need to meet sustainability goals are driving industries to seek solutions that optimize resource consumption. While advanced technologies and system upgrades often take the spotlight, an often-overlooked hero in energy conservation is industrial insulation.
Properly designed and installed insulation systems can significantly reduce energy loss, enhance operational efficiency, and support sustainability efforts—all while improving safety and reducing costs. This article explores the critical role of insulation in industrial facilities and provides actionable insights for facility managers and engineers.
Understanding Energy Loss in Industrial Facilities
Industrial facilities consume vast amounts of energy to power equipment, maintain process temperatures, and ensure safe and efficient operations. However, a significant portion of this energy can be wasted due to insufficient or deteriorating insulation.
Key areas of energy loss include:
- Piping Systems: Heat loss in uninsulated or under-insulated pipes can result in increased fuel consumption and higher energy bills.
- Process Equipment: Boilers, tanks, and reactors without proper insulation can lead to substantial thermal inefficiencies.
- Building Envelopes: Poor insulation in walls, roofs, and floors allows heat transfer, undermining climate control efforts.
Investing in robust insulation solutions addresses these challenges, helping facilities operate at peak efficiency.
Benefits of Effective Industrial Insulation
- Energy Savings
Well-insulated systems reduce heat transfer, maintaining optimal operating temperatures and lowering energy consumption. This can translate into significant cost savings over time, particularly for energy-intensive processes. - Improved Safety
Insulation helps regulate surface temperatures, reducing the risk of burns from hot equipment and pipes. It also minimizes condensation, preventing slippery surfaces and mold growth. - Extended Equipment Life
By stabilizing operating temperatures, insulation reduces the strain on equipment, decreasing wear and tear and extending the lifespan of machinery. - Environmental Sustainability
Lower energy consumption leads to reduced greenhouse gas emissions, aligning with corporate sustainability goals and environmental regulations.
Choosing the Right Insulation for Your Facility
Selecting the appropriate insulation depends on several factors, including the application, operating conditions, and material compatibility.
- Temperature Range: High-temperature applications require materials like ceramic fibers, while lower temperatures might use fiberglass or foam.
- Chemical Resistance: Facilities handling corrosive chemicals need insulation that can withstand harsh environments.
- Moisture Resistance: Materials like closed-cell foam are ideal for environments prone to condensation.
An in-depth assessment of facility needs and operating conditions is crucial for choosing the right insulation materials.
Maintenance Matters: Regular Inspections for Maximum Efficiency
Even the best insulation systems require regular maintenance to ensure optimal performance. Over time, insulation can deteriorate due to physical damage, exposure to chemicals, or natural wear. Periodic inspections help identify issues such as:
- Damaged Insulation: Cracks, tears, or missing sections that compromise thermal performance.
- Moisture Intrusion: Wet insulation loses its effectiveness and can lead to corrosion.
- Aging Materials: Older insulation may no longer meet current efficiency standards.
Routine maintenance and timely repairs can prevent energy loss and extend the lifespan of insulation systems.
Industry Standards and Best Practices
Organizations like the National Insulation Association (NIA) and the Thermal Insulation Association of Canada (TIAC) provide guidelines and resources to ensure insulation systems meet industry standards. Following these best practices helps facilities achieve maximum efficiency while adhering to safety and environmental regulations.
For example, the NIA’s “Insulation Energy Appraisal Program” can help facilities quantify the energy savings and environmental benefits of proper insulation.
A Holistic Approach to Efficiency
Insulation is just one piece of the energy efficiency puzzle. Combining it with other strategies, such as equipment upgrades, heat recovery systems, and energy audits, can amplify results.
Facility managers should work with experienced professionals to design and implement a comprehensive energy efficiency plan that considers insulation alongside other improvements.
Helpful Resources for Industrial Insulation
For facility managers and engineers looking to upgrade their insulation systems, exploring available solutions and consulting with experts is essential. Northern Industrial Solutions provides tailored insulation services designed to meet the unique needs of industrial facilities. Their expertise in materials, installation, and maintenance ensures optimal performance and long-term value.
Optimizing Efficiency Starts with Insulation
Energy efficiency is no longer optional—it’s a necessity for industrial facilities aiming to reduce costs, enhance sustainability, and stay competitive. Insulation plays a pivotal role in this effort, offering significant benefits with a relatively low investment.
By prioritizing effective insulation systems, facilities can achieve substantial energy savings, improve safety, and contribute to a greener future. Whether upgrading existing systems or designing new ones, the right insulation solution can make all the difference.
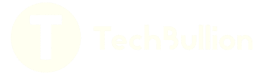