Choosing the right actuator can be challenging, especially when balancing power efficiency and performance. Rotary actuators convert energy into controlled rotational movement, and their applications span many industries—from robotics to aerospace. Finding one that minimizes energy use while maintaining high functionality is key for long-term operational success. In this guide, we’ll outline how to select the best rotary actuator that suits your needs without compromising performance.
Understanding Different Types of Rotary Actuators
Before selecting a rotary actuator, it’s important to understand the different types available on the market. Each has unique features that can affect energy consumption and performance.
- Pneumatic Rotary Actuators: These actuators use compressed air to generate motion. While they are often inexpensive and quick to operate, inefficiencies in air compression can sometimes lead to higher energy costs.
- Hydraulic Rotary Actuators: Known for their strength, hydraulic actuators are ideal for heavy-duty applications. However, the need for constant fluid pressure results in significant energy consumption over time.
- Electric Rotary Actuators: These are favored for their energy efficiency and precision control. They use electricity directly, which minimizes energy loss, making them a top choice for applications where power conservation is critical.
Knowing the strengths and weaknesses of each type will help you make a more informed decision. While pneumatic and hydraulic options provide power, electric actuators often offer the greatest energy savings.
Key Factors in Minimizing Power Consumption
Efficient energy use in actuators is not solely dependent on the type of power source. Several additional factors are crucial in minimizing power usage without sacrificing performance.
- Torque Requirements: Choosing an actuator with the right torque output for your application is crucial. Actuators with excess torque capacity waste energy, while those with insufficient torque strain to perform, leading to inefficient operation. Carefully assess your torque needs to ensure optimal energy consumption.
- Duty Cycle: The duty cycle refers to how often the actuator will operate. For high-frequency use, selecting a model designed for continuous operation can help reduce energy use. Actuators not built for frequent cycling tend to overheat or degrade more quickly, consuming more energy as they age.
- Efficiency Rating: Manufacturers often provide efficiency ratings for their actuators. Choosing one with a high rating ensures you get the most power for the least amount of energy. An efficient rotary actuator will reduce operational costs and extend your system’s lifespan by reducing the strain on components.
Choosing Materials and Design for Energy Efficiency
Materials and overall design can greatly impact the energy efficiency of your actuator. Lightweight materials and streamlined designs reduce the mechanical resistance that actuators must overcome, thus lowering power consumption.
- Lightweight Construction: Actuators made from lightweight yet durable materials such as aluminum or composite plastics reduce their load to move. This allows for lower energy use, especially in electric models where weight directly influences energy consumption.
- Low-Friction Components: Opt for actuators with low-friction seals, bearings, and other internal components. Lower friction reduces the energy required to generate movement, ensuring your actuator operates efficiently over time.
- Compact Design: Smaller, compact actuators typically require less power, especially when the task doesn’t require a large machine. These designs help streamline power use without impacting the actuator’s ability to perform.
Practical Tips for Maximizing Efficiency
Several practical strategies can help you minimize energy use without compromising functionality when evaluating rotary actuators.
- Optimize Your Application’s Load: One of the most direct ways to reduce power consumption is to fine-tune the load the actuator handles. If your system carries too much weight or resistance, it forces the actuator to work harder, leading to unnecessary energy waste.
- Control Systems Matter: Advanced control systems can regulate the power an actuator uses. Look for actuators with built-in feedback systems, as these allow for more precise adjustments in real-time, preventing energy waste.
- Regular Maintenance: Actuators, like any mechanical component, degrade over time. Regularly lubricating moving parts and checking for wear ensures that your system continues to operate efficiently.
Electric Rotary Actuators: The Most Energy-Efficient Option
Electric rotary actuators minimize power consumption by using electrical energy directly, avoiding the inefficiencies of pneumatic and hydraulic systems. Advances in motor technology enhance their precision, smoothness, and efficiency, making them ideal for energy-conscious applications. They also support sustainability by eliminating compressed air or hydraulic fluid, reducing energy losses. Factors like torque, duty cycle, and materials help balance energy efficiency, performance, and long-term reliability.
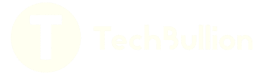