“One of the major challenges that food manufacturing organizations often face has to do with meeting demand in the wake of ever-changing consumer expectations,” said Matt Frauenshuh, CEO of Fourteen Foods and Principal of Frauenshuh Inc.
This is especially evident given everything going on in the world right now – in 2020 at the onset of the pandemic, consumer behaviors changed rapidly and only the most efficient and productive facilities were able to adapt in kind.
In most situations, improving productivity is less the product of any one major move and is more about a series of smaller and more strategic ones. When taken together, they add up to the meaningful change that you need to pave the way for years of success to come. Based on that, if you’re looking for new opportunities to capitalize on to improve productivity in food manufacturing, there are a number of important steps that you’ll want to keep in mind.
1. It Starts With Training
By far, one of the best ways to improve productivity when it comes to food manufacturing involves prioritizing employee training whenever possible.
“If you want your staff to maximize their own productivity within the context of your organization, it stands to reason that they need to know as much about how to do that as possible, which is where thorough and continuous training comes into play,” said Frauenshuh.
Not only do they need to be aware of the proper safety protocols that they should be following, but they also need to better understand their own responsibilities within the context of the larger whole.
Note that this extends not only to the new employees that you’re bringing into the fold but to your existing ones as well. Ongoing education needs to become and remain a top goal for your food processing organization.
2. Focus on Quality Control
Another way to improve productivity in food manufacturing involves empowering your existing quality control systems as much as possible, along with implementing new ones. X-ray systems can be used to check products for foreign objects that should be there, for example, which is a great way to avoid delays in production or even a costly recall situation. Climate and temperature control systems should be implemented to help avoid these types of situations that could introduce contaminants to your products.
3. Don’t Neglect Energy Efficiency
Another method to increase productivity in food manufacturing that a lot of organizations often overlook involves emphasizing energy efficiency whenever possible. Note that this doesn’t just have to do with the energy efficiency of your own equipment, although that is very much important. It also extends to the larger facility that you operate in, too.
Invest in things like LED light bulbs and energy-efficient products. Not only do they last longer, but they also use less energy to operate – generating potentially huge cost-savings in the process. That money can then be funneled back into other areas of your business where it can make the biggest impact.
4. Embrace Automation
For a modern food manufacturing facility, the importance of embracing automation literally cannot be overstated.
In food manufacturing, there are a lot of processes that, while essential, take up a lot of someone’s time. By automating things like sorting and packaging, you can free up the attention of those employees so that they can focus on the tasks that truly need their attention.
Not only that, but you also increase both the speed at which these tasks can be completed and the quality of the finished product, too. Automation helps to eliminate potential issues like human error, generating consistent and dependable results across the board.
5. Preventative Maintenance is Key
Finally, one of the best ways to improve productivity in food manufacturing involves making preventative maintenance a top priority.
Think for a moment about the cost associated with just one hour of unplanned downtime for a critical piece of machinery. Not only do you have to pay to fix whatever the issue is (assuming you can get parts for necessary repairs right away), but you also have to think about the cost associated with the period when this machine was not performing.
The issue is that most organizations still take a reactionary approach to maintenance – they wait for a piece of equipment to break so that they can fix it. Preventative maintenance, on the other hand, allows you to address a small problem today before it has a chance to become a much bigger (and costlier) one tomorrow.
In the end, improving productivity in food manufacturing should always be a top priority. Not only does it help you extract more value from the resources you’ve already invested in (both in terms of equipment and employees), but it helps preserve profit margins in an industry that is growing increasingly competitive all the time. In all likelihood, it will be a combination of the above techniques that help to generate the results that you’re after – bringing with it a leaner, more efficient, and more profitable organization before you know it.
About Matt Frauenshuh
As Chief Executive Office for Fourteen Foods and Double Seven Development, Matt Frauenshuh has led his family’s business to become the largest Dairy Queen franchisee in the U.S. Fourteen Foods currently owns and operates over 240 DQ Grill & Chill Restaurants in 13 states. He leads the company modeling the core values of faith and family. Matt has sat on the boards of the National Prayer Breakfast CEO Panel and United Heroes League.
Matt has a bachelor’s degree in business economics from St. Olaf College. He received his MBA from the University of Minnesota’s Carlson School of Management. Matt is on the national board for The Salvation Army.
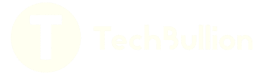