In this exclusive TechBullion interview, we’re thrilled to speak with Shashank Sawant, a distinguished leader in competency and career development within the oil and gas industry, recognized for his innovative approaches to workforce optimization and technical excellence Shashank brings a wealth of experience and insight into building a culture that prioritizes continuous improvement and excellence. Throughout our conversation, he shares valuable strategies for defining core values, fostering a commitment to quality at all levels, and integrating continuous improvement into daily operations. Shashank offers a comprehensive look at how tech companies can stay resilient and adaptable amid rapid advancements in AI, quantum computing, and other emerging technologies, from empowering employees to developing competency frameworks and embracing agile methodologies. Join us as Shashank reveals how these practices enhance individual and team performance and position organizations to thrive in a future defined by innovation and quality.
What do you believe is the first step for tech leaders aiming to create a culture of quality and competence within their organizations?
The first step is to define core values and expectations. Articulate what quality and competence mean for your company and make sure every single person in the organization understands it. Building a strong culture of quality and competence is essential for organizations to achieve excellence in performance.
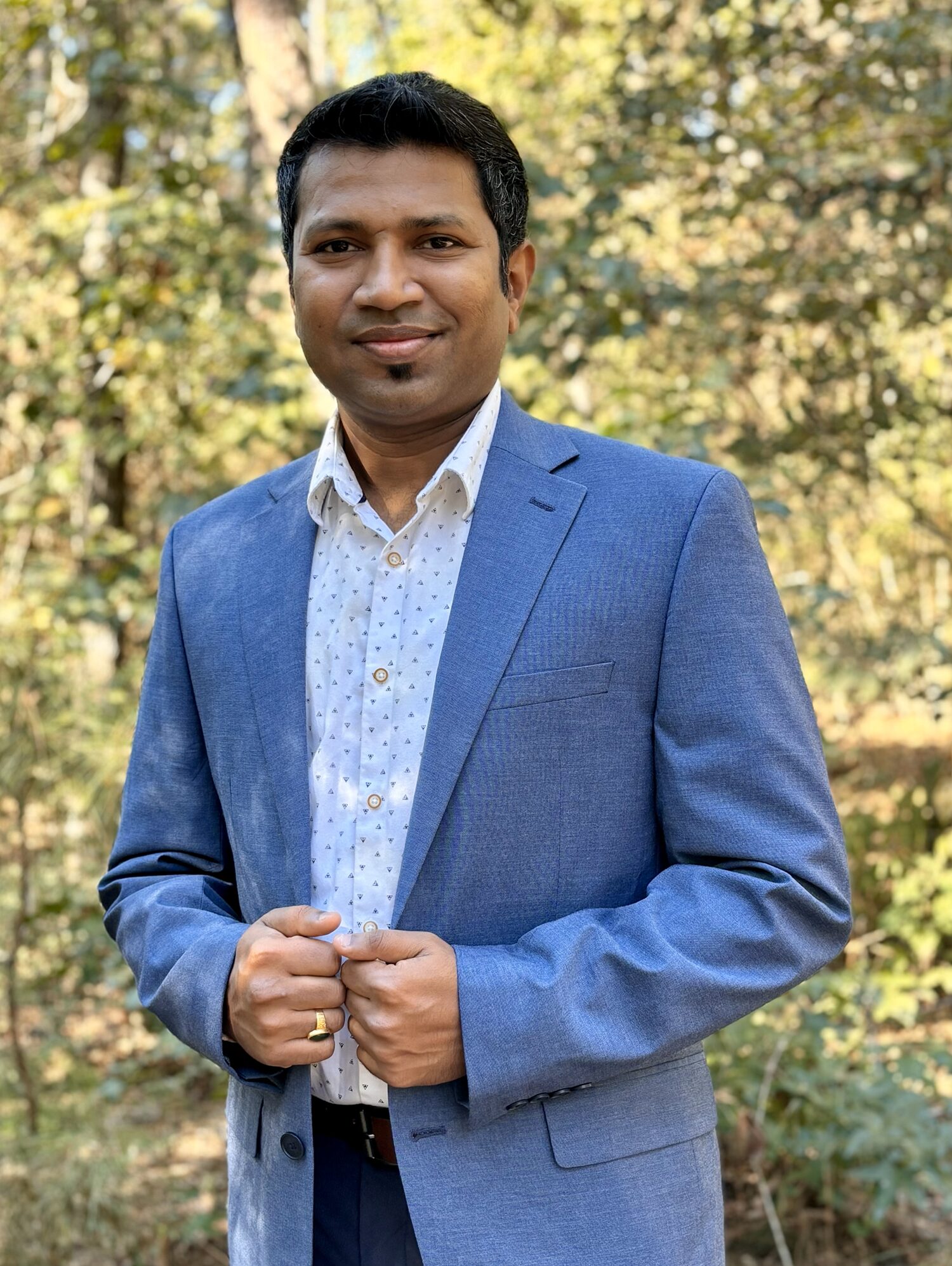
Shashank Sawant
Continuous improvement is crucial in tech, but how does this approach translate into everyday practice? What benefits do you see it bringing to both individuals and teams?
Continuous improvement in tech companies often manifests through incremental changes and iterative processes. By weaving continuous improvement into the fabric of daily operations, tech companies foster a dynamic and progressive work environment.
In practice, continuous improvement can be integrated into daily operations through several key actions. Daily morning meetings allow teams to briefly discuss progress, address roadblocks, and outline the next steps, fostering a routine of reflection and adjustment. Regular feedback from both customers and team members helps pinpoint areas for enhancement and encourages a growth mindset within the team. Conducting post-project reviews is another essential practice, focusing on what went well and identifying potential improvements to drive future efficiency. Additionally, implementing Agile methodologies ensures projects are adaptable to change, enhancing flexibility and responsiveness across the team.
Continuous improvement offers numerous benefits for both individuals and teams. For individuals, it fosters skill development, as ongoing learning and adaptation help them stay current and relevant in their fields. This process also enhances job satisfaction, as tangible improvements boost morale and engagement. Additionally, it contributes to professional growth, providing opportunities that lead to career advancement. For teams, continuous improvement enhances collaboration by encouraging frequent communication and constructive feedback, which strengthens teamwork. It also drives higher productivity, as streamlined processes and clear objectives increase efficiency. Furthermore, it promotes innovation, creating a culture that values creative problem-solving and forward-thinking solutions.
How can competency frameworks help promote a commitment to quality, and what can organizations do to ensure these frameworks are aligned with their long-term goals?
A competency framework promotes quality by setting clear expectations for essential skills and behaviors, ensuring that all team members meet a high standard. It supports career development by providing a structured roadmap for personal and professional growth, helping individuals enhance their competencies over time. By enabling consistent evaluation, the framework highlights areas for improvement, which drives overall performance. Additionally, it aligns individual goals with organizational objectives, fostering a shared commitment to quality across the team. With clearly defined competencies, the framework also fosters accountability, making it easier to hold team members responsible for their performance.
This kind of structure supports continuous improvement and drives a culture focused on excellence.
Organizations can ensure competency frameworks align with their long-term goals by:
- Involving Leadership: Engage top management in defining and updating competencies, ensuring they reflect strategic objectives.
- Regular Reviews: Periodically review and update the framework to match evolving goals and industry standards.
- Employee Feedback: Gather feedback from employees at all levels to ensure the framework is realistic and actionable.
- Clear Communication: Communicate how competencies tie into the organization’s vision and long-term strategy.
- Integrated Training: Align training and development programs with the competency framework to support goal achievement.
Incorporating these steps creates a dynamic and relevant competency framework, seamlessly integrated with long-term goals. It’s all about staying proactive and adaptable.
Aligning individual skills with company-wide quality objectives can be challenging. How can leaders effectively communicate these goals to ensure everyone understands their role in achieving them?
Leaders must first live with the example and encourage them to follow company-wide quality objectives in terms of policy. The Clarity in the communication and consistency in the follow-ups will give a clear picture if the changes are being followed up from top to bottom.
Contribution in Quality: Show each individual how their roles and skills contribute to the larger quality goals. Concrete examples will help them to understand their importance in the company’s quality goals. For example, manufacturing a single hydraulic component O ring costs $0.5 but may cost millions of dollars if it’s not up to quality standards.
Frequent Updates: Regular check-ins, meetings, and updates will reinforce the objectives and keep them top of mind. Having continuous engagement with employees will help management to achieve the goal. Stand-down lesson learning or lunch and learning will give an open platform for discussion.
Training: Utilize tools like a Learning Management System or internal communication channels for ongoing learning and feedback loops. The updated learning must be reassigned periodically to keep the tempo and achieve the necessary objective.
Gauging Understanding: performing frequent Gauge R&R will allow management to understand if the quality is being followed every time. This will give an idea of whether companies need any changes in training since Gauge R&R will help to understand the gaps.
Recognition and Rewards: Acknowledge and celebrate when an individual meets or exceeds these objectives, This positive reinforcement promotes continuous alignment and motivation. Creating initiatives such as zero quality issues or identifying someone Quality Champion will lead the competitiveness among the employees or teams.
Quality consistency is essential, especially across large teams. Can you share any examples or best practices for ensuring alignment and consistency in quality across an organization?
To achieve consistent quality, it is essential to establish clear standards by developing comprehensive guidelines that are well-documented and easily accessible to all team members. Training and development should be a regular practice, with sessions designed to keep everyone updated on the latest quality practices. Conducting quality audits periodically helps monitor adherence to these standards and highlights areas for improvement. Additionally, creating feedback mechanisms encourages team members to share insights and suggestions, fostering a culture of continuous improvement. Defining and tracking quality metrics is also crucial for measuring performance and identifying trends. Strong leadership involvement is needed to actively promote and support quality initiatives, while cross-functional collaboration between departments ensures a unified approach to quality throughout the organization.
One notable example is Toyota’s implementation of the Toyota Production System (TPS). TPS emphasizes continuous improvement and respect for people. It includes practices like Just-In-Time (JIT) production and Kaizen (continuous improvement), ensuring every employee is involved in maintaining high-quality standards. This system has enabled Toyota to maintain consistency in quality across its global operations.
Another example is the training facility, where I taught workmanship standard courses for newly hired technicians. During this training, our main focus was always on the quality and reliability of the product. We made sure employees understood and followed the quality standards, the topic of 6S practice helps them to keep their work area up to the standards so that they can reduce waste time and deliver products with high quality. These practices help create a culture of quality that permeates every level of the organization, ensuring long-term consistency.
As tech advances in fields like AI and quantum computing, quality assurance will likely face new challenges. How do you see quality practices evolving, and what can companies do now to prepare for these future demands?
As AI and quantum computing advance, quality assurance practices will need to evolve to address new complexities and opportunities. Here is how quality practices might change and what companies can do to prepare.
Evolving quality practices include:
1) AI-Driven Automation: AI will streamline and automate many QA processes, reducing human error and increasing efficiency. Machine learning models can predict quality issues before they arise allowing companies & individuals to take measures proactively.
2) Real-Time Monitoring: Technologies like IoT and cyber-physical systems will enable real-time monitoring of the production process, ensuring immediate detection and correction of quality deviations.
3) Proactive Analytics: Leveraging big data and analytics, companies can predict potential quality issues and optimize processes to prevent them.
4) Remote Audits: The adoption of remote auditing technologies will allow for efficient, cost-effective quality assessment across global operations.
To prepare for future demands, companies should focus on several key strategies. Investing in training is essential as technology advances, enabling the workforce to develop skills in emerging areas such as AI and quantum computing. Adopting agile methodologies allows teams to remain flexible and responsive to technological advancements and market shifts. Encouraging cross-functional collaboration ensures a unified approach to quality management, aligning diverse teams toward shared goals. Finally, consistently staying updated on emerging trends and innovations in quality management helps organizations maintain a competitive edge and proactively adapt to future changes.
By embracing these practices and preparing proactively, companies can ensure they are well-equipped to meet the quality demands of the future. Running campaigns like Quality is Everyone’s Business will help engage employees so they remain focused on upcoming changes. Fostering a culture of quality isn’t just about frameworks or policies.
What strategies have you found effective for encouraging a personal commitment to continuous improvement across all levels of an organization?
To cultivate a genuine commitment to continuous improvement, companies can implement several key strategies. Leading by example is essential; demonstrating a personal dedication to quality and improvement can inspire others to follow suit, with initiatives like the “Quality & Me” campaign reinforcing this mindset. Empowering employees by giving them autonomy to identify and solve issues fosters trust and encourages proactive initiatives. Encouraging employees to conduct quality stand-downs and share best practices further embeds quality into each step. Recognizing and rewarding contributions to quality improvement is equally important; acknowledgments, such as through quality observation cards, motivate others and enhance vigilance. Providing continuous learning opportunities helps ensure employees understand the quality policy and maintain relevant skills through regular training and competence management programs. Updating processes periodically, like conducting gauge R&Rs, helps management confirm that employees are implementing quality measures consistently, fostering transparency and collaboration. Finally, it is vital to provide resources so employees have the tools they need to support quality initiatives effectively, ensuring quality is integrated into every step.
By implementing these strategies, we can nurture a culture of quality where every individual feels personally invested in the pursuit of excellence.
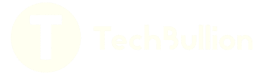