In the ever-evolving landscape of electronic connectivity, the distinction between molded cable assembly and overmolded cable assemblies has long been a topic of intrigue. These two seemingly distinct techniques, molded and overmolded, are, in fact, two sides of the same precision-engineered coin. In this extensive guide, we unravel the intricacies of these cable assembly methods, delving into their shared characteristics, unique features, and diverse applications.
Molded and Overmolded Cable Assemblies: A Unified Perspective:
At first glance, the terms “molded” and “overmolded” may appear disparate, but in reality, they share a fundamental commonality — the transformative power of precision engineering. Both cable assembly techniques hinge on encapsulating cables and connectors within protective layers, typically composed of thermoplastic or rubber materials. It’s in the nuanced details of the molding process and the extent of coverage that these two methods diverge.
Key Advantages of Molded and Overmolded Cable Assemblies:
- Enhanced Durability: The hallmark feature of both molded and overmolded cable assemblies is their ability to fortify connections against external elements. Whether it’s shielding internal components from moisture, dust, or mechanical stress, these assemblies excel in extending the lifespan of electronic connections.
- Customization Options: The flexibility of molding materials empowers manufacturers to tailor cable assemblies to specific requirements. From creating cables with varying levels of flexibility to fine-tuning resistance to chemicals, the customization options are vast and varied.
- Strain Relief Mastery: Both techniques offer exceptional strain relief capabilities, mitigating the risks associated with tension and bending. This is especially beneficial in applications where cables undergo frequent movement, ensuring longevity and reliability.
Expanding on the Advantages of Overmolded Cable Assemblies:
While molded and overmolded cable assemblies share foundational benefits, it’s in the realm of overmolding that we witness an expanded horizon of possibilities.
- Seamless Integration: Overmolded cable assembly takes the concept of protection to the next level by not only encapsulating cables and connectors but also integrating parts of the connected devices. This seamless integration eliminates the risk of debris or liquids infiltrating connection points, presenting a sleek and unified appearance.
- Enhanced Strain Relief Redux: The extended overmolded layer not only contributes to the seamless integration but also provides heightened strain relief. This makes overmolded assemblies particularly well-suited for applications demanding repeated bending or flexing.
- Aesthetic Customization: Overmolding isn’t just about functionality; it’s an opportunity for aesthetic expression. Manufacturers can select from a diverse palette of materials and colors, not only enhancing the functional aspects of the assembly but also aligning it with brand aesthetics.
Conclusion:
In the realm of electronic connectivity, the synergy between molded and overmolded cable assemblies emerges as a cornerstone of innovation. These precision-engineered techniques offer a harmonious blend of durability, customization, and strain relief. Whether opting for the precision of molded assemblies or the integrated protection and aesthetic flexibility of overmolded solutions, the key lies in aligning the choice with the specific demands of the project. As the connectivity landscape continues to evolve, understanding the nuances of these cable assembly methods becomes not just a choice but a strategic imperative for engineers and manufacturers aiming for unparalleled reliability and functionality.
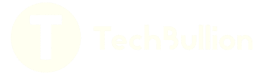