It’s no exaggeration to say power supplies in the healthcare sector are a matter of life and death. Used to supply electrical power to all manner of critical medical devices, healthcare providers must ensure their power supplies are both safe and constant.
It’s therefore no surprise that the global medical power supplies market is estimated to be worth $955.4 million, and is projected to grow at a compound annual growth rate of 7.3% to reach a value of $1459.7 million by 2028.
How do medical power supplies work?
The primary job of power supplies is to convert electric current from a source to the right voltage, current and frequency to power the device. Other functions include:
- Limiting the current drawn by the device to safe levels
- Shutting off the current if there’s an electrical fault
- Power conditioning to prevent electronic noise or voltage surges from reaching the device
- Power-factor correction, which increases the power quality should it lag
- Storing energy in case of the source power being interrupted
The importance of cooling
Another key aspect of keeping the power constant is having some sort of cooling system. As noted by XP Power: “A power converter designed to minimise stresses on components during normal operation can still suffer from poor reliability if subject to excessive heat in the end installation. As a result, good thermal management is essential for maximising reliability and service life.”
The two main ways of regulating the temperature of power supplies are conduction and convection cooling. The former involves transferring heat from one hot part to another cooler part by direct contact, while the latter involves transferring heat through natural air flow.
How do medical power supplies remain safe?
Because of the safety requirements involved in healthcare, medical power supplies need to be compliant with IEC 60601-1-2, a global standard for the safety of medical electrical equipment and systems.
Many are connected to the patient or operator via applied parts — for example, by the conductive pads of an electrocardiograph — meaning medical power supplies must feature certain means of protection (MOP) under the IEC 60601-1-2 to keep both the patient and operator safe.
The exact safety standard differs depending on the device and who exactly is being protected, and can be either a means of patient protection (MOPP) or a means of operator protection (MOOP). The three main types of MOPs are:
Insulation
Insulation is a material that does not permit the flow of electrical current. Depending on the type of medical device, it will require either basic or double insulation.
The former involves a single layer of insulation, such as plastic insulation around each conductor of an AC power cord, while the latter involves both basic and supplementary insulation. Supplementary insulation provides protection from hazardous voltages if there is a failure of the basic insulation, with one example being the plastic case of an external power supply.
Clearance and creepage
Clearance and creepage requirements relate to the distance between conductors, with gaps needed to reduce the risk of fires and electrical shocks. Clearance involves the shortest air path between two conductors, while creepage is the shortest distance between two conductors along the insulating surface. The creepage must be greater than or equal to the clearance.
MOPPs require more creepage than MOOPs — for example, MOOPs with one layer of insulation need at least 2.5mm of creepage, while the equivalent MOPPs require at least 8mm.
Isolation voltage tests
Isolation voltage refers to the highest voltage that can be applied to a device without compromising its isolation. This is a non-conductive element that allows a signal to transmit electricity through a circuit and block unwanted signals to prevent circuit damage and protect the user from electrical damage.
Different devices have different isolation voltages, with factors like the level of insulation and type of device influencing this. A device’s isolation voltage is determined by applying a test voltage for a specified amount of time and observing if there is any leakage current.
What types of medical power supplies are there?
Medical power supplies are either standalone pieces of equipment or built into the appliances that they power. They have an open or enclosed frame, a modular design so that they can be installed in separate parts, or an encapsulated design, where the device is enclosed in a casing.
Power types
Medical power supplies are also categorised by the mechanism used to convert and transfer the input power to the output power. They fit into two categories: linear and switching power supplies.
Linear power supplies – Linear power supplies process AC inputs using a power transistor in the linear operating region to provide one or more DC outputs and generate the required voltage.
Switching power supplies – Switching power supplies directly filter AC mains input to obtain a DC voltage, with a switching element or regulator constantly switching it on and off for higher power density and reduced power consumption.
Because power is lost when components operate in their linear operating region, switching power supplies are typically more efficient than linear power supplies.
Applied parts
The general application of medical power supplies falls into three categories. As touched upon earlier, many medical devices are connected to a patient, and the parts that do are referred to as applied parts. The degree to which different devices do this is used to distinguish them under the IEC 60601-1-2, with three different classifications. Each has different electrical protection requirements, which impacts the power supplies it requires
Class B (body) – This type is not conductive, such as laser treatments, and has the highest level of allowable patient leakage current.
Class BF (body floating) – Class BF devices electronically touch the patient, such as an ultrasound machine.
Class CF (cardiac floating) – This directly connects to a patient’s heart, like medical devices for dialysis or ablation, and has the lowest level of allowable patient leakage current.
Author Bio:
Kyle Olsan is a professional writer and blogger who uses his expertise, skills, and personal experience in digital marketing to craft content that resonates with audiences. Deep down, he believes that if you cannot do great things, then you can do small things in a great way. To learn more, you can connect with him online.
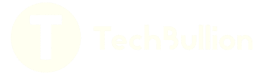