Lean manufacturing principles have sparked major breakthroughs in automotive innovation, increasing productivity, decreasing waste, and promoting efficiency. The remarkable contributions of Amey Phatale, a renowned professional whose work demonstrates the power of these principles, are highlighted in this article as it examines the transformative impact of Lean manufacturing on the automotive industry.
Lean manufacturing, also known as lean production , focuses on minimizing waste without sacrificing productivity. Originating from the Toyota Production System, this methodology emphasizes continuous improvement, respect for people, and standard work practices. By streamlining processes and eliminating non-value-added activities, Lean manufacturing enhances operational efficiency and product quality. In the automotive industry, where competition is fierce and margins are thin, adopting Lean manufacturing principles can mean the difference between success and failure. These principles enable manufacturers to produce high-quality vehicles at lower costs, meet customer demands more effectively, and respond swiftly to market changes.
Amey Phatale’s journey in the field of Lean manufacturing is a testament to the transformative potential of these principles. His career is marked by a series of notable achievements that have significantly impacted the organizations he has worked with.
Amey began his career as an intern at Cumberland Plastic Solutions, where he utilized $250,000 worth of plastic scrap material to develop recipes for future utilization. His creative strategy helped him land a full-time position at Hanon Systems Alabama as a production engineer. He reduced heat exchanger scrap by $840,000 a year by implementing a Kanban Card System here. His skills in lean manufacturing brought him a job at Magna International, where he was employed in a sequencing or Just-In-Time (JIT) facility.
At Magna International, Phatale led numerous continuous improvement projects, achieving substantial cost savings and efficiency gains. He successfully stabilized the production launch of the composite liftgate while reducing waste by $180,000. He oversaw initiatives on the Liftgate Assembly Line as well, where he reduced labor costs by 16% and saved $675,000 a year. Additionally, he improved operations on the FASCIA lines, saving $810,000 annually by reducing labor by 14%, and on the FEM line, saving $675,000 annually by reducing labor by 15%. By reducing labor by 47% on the Liftgate Bonding Line, his efforts yielded an annual savings of $945,000. Amey then got the opportunity to work in another plant of Magna International as Sequencing engineer. Here, he implemented labor optimization solutions on one of the largest FASCIA assembly lines, which led to a 30% labor reduction and annual savings of $2.3 million. Leading the charge on design for manufacturability (DFM) and the Jeep Grand Cherokee and Dodge Durango FASCIA line launches, he helped save 50,000 square feet of space, which is worth $12 million .
Phatale’s remarkable performance history brought him a position as Senior Process Engineer at electric vehicle startup Rivian Automotive. At Rivian, he made significant contributions in their battery shop. He led continuous improvement projects on the battery sub-module marriage station, increasing throughput by 600% and contributing to a $1.2 billion annual revenue increase. He also reduced scrap on battery modules, saving $20 million in 2023. Furthermore, he enhanced battery safety performance using lean manufacturing techniques, improving thermal runaway time by 580% and time to consumption by 228%.
Throughout his career, Amey has successfully navigated numerous challenges. At Hanon Systems, he implemented a Kanban Pull System, significantly reducing inventory, defects, overproduction, scrap, and over processing. At Magna International, his detailed PFMEA work improved product quality, and his cycle time analysis and layout optimization efforts resulted in substantial labor cost reductions. At Rivian, he addressed process control issues by implementing a potting process reaction plan and defining sub-module marriage specifications.
Amey shares his knowledge and experience with the engineering community through various publications. His work is accessible via [IJSR](https://www.ijsr.net/search_author_results.php?authors=Amey%20Phatale). Additionally, he actively mentors interns and entry-level engineers, ensuring they make a meaningful impact on their work.
As an experienced professional, Phatale emphasizes the importance of quality systems as the backbone of manufacturing businesses. He advocates for data integrity, noting that analysis is only as good as the data available. In his opinion, promoting team collaboration has been crucial for achieving swift and long-term success.
The expert predicts that innovation in manufacturing will be driven by openness, cooperation, and constant improvement. The principles of Lean manufacturing will continue to evolve, integrating advanced technologies and methodologies to meet the ever-changing demands of the automotive industry.
These principles have a significant impact on the automotive industry and beyond, as demonstrated by Amey Phatale’s contributions to Lean manufacturing. His achievements demonstrate the potential for continuous improvement and innovation in manufacturing processes, driving efficiency, reducing costs, and enhancing product quality. As the industry continues to evolve, the insights and experiences of professionals like Amey will be invaluable in shaping the future of automotive innovation.
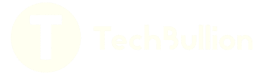