In the world of precision manufacturing, ensuring accurate wall thickness and concentricity is crucial. Industries such as medical tubing, aerospace, wire and cable, and industrial extrusion demand high levels of quality control, regulatory compliance, and material efficiency. To meet these needs, manufacturers require cutting-edge, real-time measurement solutions that allow for continuous process monitoring and defect detection.
Enter LaserLinc’s UltraGauge+™ series, an advanced ultrasonic measurement system designed to provide real-time, non-contact wall thickness and concentricity measurements. This breakthrough technology helps manufacturers increase productivity, reduce material waste, and ensure product integrity—all while seamlessly integrating into existing production lines.
Let’s explore how UltraGauge+™ is setting new standards for ultrasonic measurement technology and why manufacturers across multiple industries are turning to LaserLinc for unmatched accuracy and process control.
Why Ultrasonic Measurement is Critical in High-Specification Manufacturing
Ensuring Precision, Compliance, and Quality
For manufacturers producing tubing, pipes, and cables, precise wall thickness and concentricity are non-negotiable. Even the smallest deviations can lead to:
✔ Product failures, leading to costly recalls and warranty claims.
✔ Regulatory non-compliance, delaying production and increasing expenses.
✔ Excess material waste, driving up manufacturing costs unnecessarily.
By implementing advanced ultrasonic measurement solutions, manufacturers can maintain strict tolerances, optimize material usage, and improve product quality—ensuring a competitive edge in today’s market.
UltraGauge+™: A Game-Changer in Ultrasonic Measurement
1. Real-Time, In-Process Measurement
Traditional quality control methods require manual inspections and post-production testing, often leading to delays and production inefficiencies. With UltraGauge+™, manufacturers can:
✔ Monitor wall thickness, concentricity, and layer thickness in real-time.
✔ Receive immediate pass/fail alerts for out-of-spec products.
✔ Make process adjustments on the fly, reducing material waste and downtime.
By providing continuous, automated measurement, UltraGauge+™ allows manufacturers to eliminate inefficiencies and maintain product consistency.
2. Non-Contact, High-Precision Technology
Unlike traditional contact-based measurement tools, which can alter or damage delicate products, UltraGauge+™ uses non-contact ultrasonic waves to measure wall thickness without interfering with the material itself.
✔ Measures ultra-thin walls—ideal for medical tubing and high-precision components.
✔ Works with a wide range of materials, including plastics, metals, rubber, and glass.
✔ Provides accurate results regardless of material opacity, unlike optical systems.
This level of accuracy and adaptability makes UltraGauge+™ the go-to solution for manufacturers in industries requiring extreme precision.
3. Industry-Leading Thin-Wall Measurement Capabilities
One of the most impressive features of UltraGauge+™ is its ability to measure ultra-thin materials with exceptional accuracy.
✔ Detects wall thickness as thin as 0.001 inches (25μm) for polymer medical tubing.
✔ Measures metal tubing down to 0.003 inches (75μm), including nickel-titanium (NiTi) stent tubing.
✔ Ensures uniformity and defect-free manufacturing for critical applications.
For manufacturers of high-precision components, this technology ensures compliance with the most demanding industry standards.
To learn more about LaserLinc’s advanced ultrasonic measurement solutions, visit ultrasonic wall thickness gauge.
4. Seamless Integration with LaserLinc’s Total Vu™ HMI
The UltraGauge+™ series is designed for easy integration into existing manufacturing environments. When paired with LaserLinc’s Total Vu™ HMI, manufacturers gain:
✔ Comprehensive process visualization, including real-time SPC (Statistical Process Control).
✔ Automated data logging and reporting for quality assurance and compliance tracking.
✔ Customizable process control options, allowing seamless adaptation to production needs.
This combination of real-time measurement and process visualization gives manufacturers complete control over their production processes.
Industries Benefiting from UltraGauge+™ Technology
Medical Device Manufacturing
✔ Ensures defect-free tubing for catheters, stents, and drug delivery systems.
✔ Meets FDA and ISO 13485 compliance requirements.
✔ Minimizes waste and maximizes efficiency in high-precision extrusion processes.
Wire and Cable Production
✔ Guarantees uniform insulation thickness, preventing electrical failures.
✔ Detects variations in concentricity, ensuring consistent product quality.
✔ Reduces scrap rates and improves production efficiency.
Aerospace and Automotive Manufacturing
✔ Maintains strict tolerances for fuel lines, hydraulic tubing, and high-performance materials.
✔ Detects micro-defects that could compromise safety in mission-critical applications.
✔ Enhances quality control while reducing overall production costs.
By implementing UltraGauge+™, manufacturers across industries can achieve unparalleled accuracy, consistency, and efficiency.
For more details on how LaserLinc’s technology is transforming precision measurement, visit ultrasonic measurement.
Why Manufacturers Trust LaserLinc for Ultrasonic Measurement
1. Customizable Solutions for Every Industry
✔ UltraGauge+™ can be tailored to meet the specific needs of different production lines.
✔ Flexible sensor assemblies allow for seamless integration into existing and new manufacturing systems.
✔ Fully scalable, accommodating both small-batch and high-volume production environments.
2. Unmatched Accuracy and Reliability
✔ Industry-leading precision, delivering consistent, repeatable results.
✔ Reduces reliance on manual inspection, improving process control and consistency.
✔ High-resolution ultrasonic sensors ensure the most accurate measurements possible.
3. Backed by Decades of Expertise
✔ LaserLinc has over 20 years of experience in precision measurement solutions.
✔ Committed to continuous innovation, ensuring customers receive the most advanced technology.
✔ Dedicated customer support, ensuring smooth implementation and ongoing success.
With a proven track record in precision measurement, LaserLinc remains a trusted partner for manufacturers worldwide.
Final Thoughts: The Future of Ultrasonic Measurement with UltraGauge+™
In today’s fast-paced manufacturing world, precision and efficiency are more critical than ever. With LaserLinc’s UltraGauge+™ series, manufacturers gain a powerful tool for real-time, in-process measurement, allowing them to:
✔ Reduce waste and material costs through continuous monitoring.
✔ Improve product quality and compliance with industry regulations.
✔ Enhance efficiency with automated process adjustments and real-time feedback.
Whether you’re in medical tubing, wire production, or high-performance material manufacturing, UltraGauge+™ provides the accuracy, reliability, and flexibility you need to stay ahead of the competition.
To explore LaserLinc’s advanced ultrasonic measurement solutions and see how they can revolutionize your production process, visit LaserLinc today!
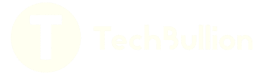