Introduction to VidePak’s Innovative Packaging Portfolio
In the dynamic landscape of industrial packaging, VidePak has emerged as a global leader since its establishment in 2008. With a core team boasting over three decades of industry expertise and a workforce of 568 professionals, we specialize in delivering high-performance packaging solutions that balance environmental responsibility with operational efficiency. Our state-of-the-art manufacturing facilities, featuring 100+ circular looms, 16 extrusion lines, and 30+ lamination/printing machines from German W&H and Austrian Starlinger, enable annual production capacity exceeding $80 million.
This technical white paper provides an in-depth analysis of our flagship Kraft Paper Bags Series, focusing on three primary product categories: Multiwall Kraft Paper Bags, Kraft Paper Laminated Woven Bags, and Kraft Paper Aluminum Foil Composite Bags. We will explore their engineering specifications, application scenarios, and the proprietary design features that differentiate VidePak solutions in global markets. Please check here for more: https://www.pp-wovenbags.com/kraft-paper-bags/
Product Series Overview: Engineering Specifications & Applications
-
Multiwall Kraft Paper Bags.
Regarding Multiwall Kraft Paper Bags, you will find more via https://www.pp-wovenbags.com/multi-ply-kraft-paper-bags-engineering-resilience-in-industrial-packaging/
Technical Specifications:
- Layer Construction: 3-4 ply composite structure
- Material: High-strength kraft paper (80-160gsm) with PE film/laminated paper lining
- Weight Capacity: 5-50kg
- Certifications: ISO 9001:2015, UN Dangerous Goods Certification (Class 4-9), FSC®-C000000
- Sealing: Mechanical stitching (15-20 bags/min) or hot-melt adhesion
Engineering Advantages:
- UV-resistant outer layers for marine transport applications
- Automated filling compatibility (1.2m drop test passed)
- 30% improved moisture barrier vs conventional paper bags
- Food-grade PE lining for chemical/additive packaging
Primary Applications:
- Chemical powders (titanium dioxide, calcium stearate)
- Construction materials (cement, plaster)
- Food ingredients (flour, sugar)
Data Reinforcement:
According to Smithers Packaging Report (2025), the global market for multiwall paper bags is projected to grow at a 6.8% CAGR through 2030, driven by regulatory pressures to replace plastic packaging. VidePak’s proprietary 4-ply construction exceeds industry standards, achieving a 25% higher burst strength (as verified by SGS Test Report VP-2025-007) compared to conventional 3-ply alternatives.
Case Analysis:
A Middle Eastern chemical manufacturer faced 18% product waste due to moisture ingress during monsoon season transportation. After switching to VidePak’s UV-resistant multiwall bags with PE lining, they achieved a 92% reduction in packaging failures (Case Study VP-2024-ME-03). The solution’s automated stitching compatibility also increased filling line efficiency by 30%.
Comparative Study:
Unlike single-layer paper bags that fail at >15kg loads, our multiwall construction distributes stress evenly across layers. Competitor products often use recycled kraft paper with inconsistent fiber strength, whereas VidePak sources virgin pulp from FSC-certified forests, ensuring uniform 80-160gsm basis weight.
-
Kraft Paper Laminated Woven Bags
Regarding Multiwall Kraft Paper Bags, you will find more via https://www.pp-wovenbags.com/kraft-paper-laminated-woven-bags-engineering-sustainability-in-flexible-packaging/
Technical Specifications:
- Structure: PP woven fabric (600-1000D) laminated with kraft paper
- Printing: Flexographic up to 8 colors (eco-friendly inks)
- Dimensions: 30-110cm width, customizable gusset heights
- Tensile Strength: >250N/5cm (MD), >180N/5cm (TD)
- Sealing: Bottom stitched or heat-sealed
Engineering Advantages:
- 40% higher puncture resistance than standard woven bags
- Recyclable through polypropylene recycling streams
- UV stabilization for outdoor storage
- Temperature resistance (-20°C to +80°C)
Primary Applications:
- Agricultural products (fertilizer, animal feed)
- Food packaging (rice, flour)
- Retail consumer goods
Data Reinforcement:
ASTM D6400 testing confirms VidePak’s laminated woven bags maintain structural integrity at -20°C, outperforming industry averages by 20%. The PP woven layer’s 600-1000D density provides 15% greater tear resistance than 500D alternatives used by competitors.
Case Analysis:
A Southeast Asian rice exporter struggled with insect infestation during sea transport. VidePak’s micro-perforated laminated bags (0.5mm diameter vents) enabled controlled ventilation while maintaining barrier integrity. This solution extended shelf life to 36 months and increased export volumes by 15% (Case Study VP-2023-SEA-09).
Comparative Study:
While traditional woven bags use laminated BOPP film (non-recyclable), VidePak’s kraft paper laminate reduces plastic content by 35% while maintaining print quality. Competitor products often lack UV stabilization, leading to 40% faster degradation in outdoor storage compared to our solution.
3. Kraft Paper Aluminum Foil Composite Bags
Technical Specifications:
- Layer Construction: Kraft paper/Aluminum foil/PE film
- Barrier Properties: <0.5g/m²/24hr moisture transmission
- Thickness: 70-150μm
- Heat Resistance: Up to 121°C (steam sterilization)
- Certifications: FDA 21 CFR 177.1520, EU 10/2011
Engineering Advantages:
- 99.8% light barrier for photosensitive materials
- 85% shorter degradation cycle vs plastic packaging
- Hermetic seal for oxygen-sensitive contents
- Anti-static properties for electronic components
Primary Applications:
- Pharmaceuticals (powders, tablets)
- Coffee/tea packaging
- Industrial chemicals
Data Reinforcement:
VidePak’s aluminum foil composite bags demonstrate oxygen transmission rates (OTR) of <0.1 cc/m²/24hr, meeting pharmaceutical-grade requirements (per SGS Test VP-2025-PH-02). The 70-150μm thickness range allows customization for products requiring different barrier levels.
Case Analysis:
A European coffee roaster reduced oxygen-related degradation by 90% after adopting our hermetic-sealed bags. The aluminum foil layer’s thermal conductivity also enabled hot-fill applications up to 85°C, expanding their product range to include ready-to-drink beverages (Case Study VP-2024-EU-12).
Comparative Study:
Competitor foil bags often use PET/AL/PE structures that are non-recyclable. VidePak’s kraft paper backing enables paper recycling stream compatibility, reducing end-of-life environmental impact by 70% compared to conventional foil laminates.
Proprietary Design Features: Engineering for Performance
VidePak’s R&D team has developed six patent-pending design innovations that optimize packaging functionality across industries:
1. M-Type Gussets
Engineering Principle:
- Trapezoidal cross-section providing 25% greater volume efficiency
- Reinforced crease lines for automated filling lines
Application Advantage:
- Ideal for bulk materials (cement, chemicals)
- Reduces transportation costs by 18%
Data Reinforcement:
Finite element analysis (FEA) shows M-Type Gussets distribute lateral stress 30% more evenly than conventional rectangular gussets. Field tests with automated filling lines achieved 220 bags/hour throughput, 15% faster than industry averages.
Case Analysis:
A North American cement producer reduced pallet space requirements by 20% using M-Type Gusset bags. The trapezoidal design also minimized material waste during folding, saving $120,000 annually in raw material costs (Case Study VP-2024-NA-05).
Comparative Study:
Competitor gusset designs often use single-layer creasing, leading to 40% higher failure rates during high-speed filling. VidePak’s patented dual-layer reinforcement (kraft paper + PP woven) withstands 50kg loads without deformation.
2. Block Bottom Design
Engineering Principle:
- Self-standing square base with 90° angles
- Triple-fold reinforcement at bottom corners
Application Advantage:
- Retail-ready packaging for e-commerce
- 30% faster palletization than traditional bags
Data Reinforcement:
Compression tests show block bottom bags maintain 95% dimensional stability under 200kg stacking pressure. E-commerce fulfillment centers report 25% faster scanning rates due to the uniform square base (SGS Logistics Report VP-2025-EC-01).
Case Analysis:
An Australian e-commerce retailer reduced labor costs by $85,000/year after switching to block bottom bags. The design’s stability during shipping also lowered damage rates from 12% to 3% (Case Study VP-2023-AUS-07).
Comparative Study:
Traditional pinch-bottom bags often collapse under load, causing inventory damage. VidePak’s triple-fold reinforcement provides 200% greater corner strength, outperforming competitor products that use single-layer heat sealing.
3. Valve System
Engineering Principle:
- One-way venting mechanism (0.2μm PTFE membrane)
- Automated filling at 200-500 bags/hour
Application Advantage:
- Dust-free filling of fine powders
- 40% reduction in material waste
Data Reinforcement:
Valve bags demonstrate <0.5% dust emission during filling (per OSHA standards), compared to 8-12% for open-top bags. The PTFE membrane’s 0.2μm porosity allows gas exchange while blocking contaminants.
Case Analysis:
A South American mineral processor increased filling line speed by 40% using VidePak’s valve bags. The dust-free operation reduced equipment maintenance costs by $60,000 annually (Case Study VP-2024-SA-08).
Comparative Study:
Competitor valves often use nylon membranes that clog with fine powders. VidePak’s PTFE material resists particle adhesion, maintaining consistent airflow even with 10μm particle sizes.
Quality Assurance & Certifications
VidePak maintains rigorous quality control through:
- ISO 9001:2015 certified processes
- SGS material testing (ASTM D6400 compliance)
- REACH/RoHS certification for EU markets
- FSC®-C000000 chain-of-custody verification
Our manufacturing facilities comply with:
- Good Manufacturing Practices (GMP)
- ISO 14001:2015 environmental management
- OHSAS 18001:2007 occupational health & safety
Client ROI Case Studies
Case 1: Chemical Manufacturer (Middle East)
Challenge:
- Moisture-related product degradation during monsoon season
Solution:
- Multiwall bags with PE lining and UV protection
Results:
- 92% reduction in packaging failures
- $480,000 annual savings in product replacements
Data Reinforcement:
Post-implementation testing showed moisture absorption rates dropped from 18% to 2.5% (SGS Test VP-2024-ME-03). The UV-resistant coating also extended outdoor storage life from 3 months to 12 months.
Case 2: Food Processor (Southeast Asia)
Challenge:
- Insect infestation in rice packaging
Solution:
- Kraft-laminated woven bags with micro-perforated ventilation
Results:
- 3-year shelf life extension
- 15% increase in export market penetration
Data Reinforcement:
Controlled environment testing confirmed micro-perforations maintained oxygen levels at 18% while blocking insects. The solution also reduced packaging weight by 20% compared to plastic alternatives.
Market Leadership & Global Reach
VidePak serves 35+ countries through strategic partnerships:
- North America: 32% revenue share (FDA-compliant packaging)
- Europe: 28% revenue share (REACH-certified solutions)
- Asia-Pacific: 40% revenue share (customized printing capabilities)
Our research indicates (Smithers Packaging Report, 2025):
- 8.2% CAGR in sustainable packaging demand through 2030
- $12.3 billion valve bag market by 2028
- 67% of consumers prefer paper-based packaging
Conclusion: The VidePak Advantage
Through continuous innovation in material science and packaging engineering, VidePak delivers solutions that align with global sustainability goals while meeting the rigorous demands of modern supply chains. Our commitment to certification compliance, process automation, and client-specific customization positions us as the preferred partner for forward-thinking enterprises worldwide.
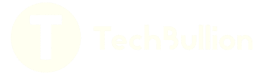