For small businesses, logistics and the work of getting products to consumers can get expensive.
Hidden costs and inefficiencies can drive these prices even higher — unnecessarily making it hard to get the best supply chain services for the money your business has.
Even small businesses can benefit significantly from finding these inefficiencies and solving them with changes in how they ship goods or procure raw materials.
With an audit of your supply chain process, you ensure that common supply chain issues don’t cut into your profit.
1. Start With the Big Picture
The best place to begin your audit is with mapping out your entire supply chain — documenting, as much as you can, every process, facility and business involved in getting goods to consumers.
Review the movement of essential business goods both on a large scale and on a small one. This means both macro movements — supplier to warehouse to consumer — and micro ones, like the movement of a package around a warehouse, mail room or office.
For example, one product may start in a factory, then move to a manufacturer’s warehouse. From there, it may be transferred to a retailer’s warehouse before eventually being distributed to various stores.
Keeping track of how products move from manufacturing to consumers will help you break down overall shipping costs into more manageable, easy-to-analyze groupings. It will also help you visualize how goods flow from supplier to customer — letting you know which suppliers and facilities are the most essential to your business.
Another may start with raw materials shipped to one of your business’s factories or facilities. There, a team will assemble the raw materials into finished products, package them, and ship them directly to customers.
When mapping your supply chain, you should avoid common supply chain mapping pitfalls — like forgetting about tier 2 or tier 3 suppliers, or those businesses that provide the resources your main suppliers depend on.
If you use supply chain management technology, take stock of it and note how it’s used.
2. Audit Your Suppliers
For small businesses, suppliers are likely one of the most important parts of your supply chain.
Once you have a rough outline of your business’s overall supply chain, you’ll want to take stock of the suppliers you work with.
This process can help you identify suppliers that are working well for your business — and help you find new ones that line up with your company values. For example, a food and beverage manufacturer that’s big on sustainability and ethical sourcing may use an audit to find a cacao supplier that operates in accordance with those values.
You should carefully consider the suppliers you choose to work with — but also be wary about switching from supplier to supplier whenever it’s convenient. In general, it’s better to have long-standing relationships with your suppliers. When you work with the same supplier, they’re more likely to think of your success as their success, too — meaning they may be more interested in providing advice, prioritizing your orders or . . .
Strong supplier relationships can also help you with strategic sourcing — suppliers with strong market knowledge may be able to help you find the best source for a particular product or raw material.
This means that, rather than just picking the supplier that offers the lowest price or fastest turnaround time, you may instead focus on building relationships with past suppliers that your business has found reliable.
Some small businesses are reluctant to focus on building relationships with their suppliers, because they may believe that their small size will lead to them being overlooked in favor of larger clients.
However, even the smallest businesses can build effective and reciprocal relationships with large suppliers, which are typically looking for clients of varying sizes, niches and strengths.
3. Review In-House Packaging Processes
Some small businesses outsource much of their packaging work. For those who keep even a small bit of the packaging process in-house, however, a process review will be essential.
This is because small inefficiencies in how your packages are put together can have a major impact on your overall logistics expenses.
For example, it’s not uncommon for issues with an outdated package strapping machine or poorly configured conveyor belt system to slow down the entire packing process and make it significantly less reliable.
With a simple equipment upgrade and change to conveyor layout, a business is typically able to make significant improvements to performance and reliability — but only if they know about these problems and their causes.
A similar strategy of reviewing your processes and looking for potential areas of improvement can help you build a more cost-effective and efficient internal packaging workflow.
4. Identify Metrics and KPIs to Measure Supply Chain Success
Once you’ve started to understand what your supply chain looks like, you can identify metrics and KPIs that will help you continue monitoring your supply chain into the future.
For example, if you’re concerned about the cost of your supply chain operations, then a KPI like cash-to-cycle time or gross margin return on investment (GMROI) will help you track the timeliness and cost of your shipments on average.
Breaking down these KPIs by supplier, product segment or niche may help provide even more insight into the performance of your supply chain. This can help you identify inefficiencies or problems with your supply chain down the line.
Optimizing Your Small Business Supply Chain
Simple changes to how your small business handles logistics can have a major impact on profit and shipping costs.
Mapping your supply chain will help you develop a full understanding of how your business and the suppliers you work with move goods to customers. It will also help you review internal shipping processes and review the suppliers you work with.
This information can help you continue to optimize supply chain operations and build strong supplier relationships well into the future.
Eleanor Hecks is editor-in-chief at Designerly Magazine. She was the creative director at a digital marketing agency before becoming a full-time freelance designer. Eleanor lives in Philly with her husband and pup, Bear.
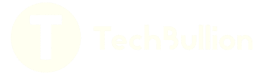