Investment casting, also known as lost-wax casting, is one of the oldest and most versatile manufacturing processes used to create highly detailed and complex metal parts. From its historical roots to its modern-day applications, investment casting has been indispensable in industries where precision, quality, and material properties are critical. At Yonglihao Machinery, we utilize state-of-the-art technology and advanced techniques to provide high-quality investment casting services that meet the demanding requirements of aerospace, automotive, medical, and other sectors.
This article delves into the investment casting process, its benefits, applications, and how Yonglihao Machinery has perfected the technique to produce components with exceptional accuracy and reliability.
What is Investment Casting?
Investment casting is a manufacturing process that involves creating a wax model of the desired part, coating it with a heat-resistant ceramic shell, and then melting away the wax to leave behind a hollow mold. This mold is then filled with molten metal to produce the final part. The technique is renowned for its ability to produce complex shapes with fine details and tight tolerances, making it ideal for parts that would be difficult or impossible to produce using other methods.
The key advantage of investment casting is its ability to work with a wide range of metals, including steel, aluminum, brass, and titanium. The parts produced by this process often require little to no further finishing, making it a highly efficient and cost-effective solution for high-precision components.
The Investment Casting Process: Step-by-Step
The investment casting process is a precise and multi-step procedure, each stage contributing to the high-quality end product. Here’s an overview of the key stages involved in the process:
Pattern Creation:The first step in investment casting is creating a wax model of the part. This pattern is typically produced by injecting wax into a mold, which is then cooled and solidified. The wax pattern must match the exact dimensions and surface finish of the final part.
Assembly of the Wax Pattern:Multiple wax patterns are often attached to a central “gate” or sprue, forming a “tree” of parts. This is especially useful for mass production, where several components are cast simultaneously.
Shell Building:The wax patterns are dipped into a slurry of fine sand and a binder to create a thick ceramic shell. The shell is then allowed to harden, forming a rigid mold around the wax. The shell is built up in several layers, with each layer being heated to remove any moisture and ensure the shell’s strength.
Wax Removal (De-waxing):The shell is then heated in an autoclave or furnace to melt away the wax. The wax is completely removed, leaving behind a hollow ceramic shell. This is why the process is also referred to as “lost-wax casting.”
Mold Firing:After the wax is removed, the shell is fired at high temperatures to further strengthen it. This step ensures the shell can withstand the high temperatures of molten metal without breaking or cracking.
Metal Pouring:The mold is preheated and then molten metal is poured into the cavity left by the wax. The metal fills the mold and takes on the shape of the original wax pattern. The type of metal used depends on the specific requirements of the part, including strength, weight, and corrosion resistance.
Cooling and Shell Removal:Once the metal has cooled and solidified, the ceramic shell is broken away, revealing the cast metal part. This process is typically done by vibration or hammering.
Finishing:After the shell is removed, the part undergoes finishing processes such as sandblasting, grinding, or polishing to remove any rough edges, improve surface quality, or achieve specific tolerances. In some cases, additional processes like heat treatment or surface coatings may be applied to further enhance the material properties of the part.
Benefits of Investment Casting
Investment casting offers a variety of advantages over other manufacturing methods. These benefits include:
Complex Geometries and Fine Details:Investment casting is capable of producing parts with intricate shapes, sharp corners, and fine details that would be difficult to achieve with traditional machining or forging methods. This makes it ideal for industries where complex and high-performance components are required.
High Precision and Tolerances:The process provides excellent dimensional accuracy, often with tolerances as tight as ±0.1 mm. Parts produced by investment casting generally require little to no finishing work, reducing both labor and material costs.
Material Versatility:Investment casting can be used with a wide variety of materials, including high-performance alloys like stainless steel, titanium, and superalloys. These materials are commonly used in aerospace, automotive, and medical applications for their strength, durability, and corrosion resistance.
Minimal Waste:Because the process uses a wax pattern that can be reused for multiple casts, investment casting minimizes material waste compared to other manufacturing processes, making it an environmentally friendly choice.
Cost-Effective for Small to Medium Production Runs:While the initial setup for investment casting can be expensive, the process becomes cost-effective for small to medium-sized production runs. This is particularly true when the parts are complex and would require expensive tooling or specialized equipment in other manufacturing methods.
Applications of Investment Casting
Investment casting is used in a wide range of industries, primarily where high precision and complex shapes are required. Some of the most common applications include:
Aerospace:Investment casting is extensively used in the aerospace industry to produce components such as turbine blades, engine parts, and structural components. These parts must meet stringent standards for strength, weight, and durability, and investment casting offers the precision and material properties needed for these critical applications.
Automotive:Automotive manufacturers use investment casting to produce engine parts, brake components, transmission parts, and other high-performance components that must withstand harsh operating conditions. The ability to cast complex shapes with high strength and low weight makes investment casting ideal for automotive applications.
Medical Devices:The medical industry relies on investment casting to produce surgical instruments, implants, and other medical devices that require both precision and biocompatibility. The process can be used with a variety of materials, including stainless steel and titanium, which are often used in implants due to their strength and resistance to corrosion.
Industrial Equipment:Investment casting is also used in the manufacturing of components for industrial machinery, such as pumps, valves, and housings. The process enables the production of durable and reliable parts that can endure the stresses of industrial applications.
Military and Defense:Components used in defense applications, such as weapons systems, vehicle parts, and communication devices, benefit from the high strength and precision that investment casting provides. The ability to create intricate parts with high reliability is critical in military and defense manufacturing.
Investment Casting at Yonglihao Machinery
At Yonglihao Machinery, we specialize in providing top-tier investment casting services that meet the demanding needs of industries such as aerospace, automotive, medical, and more. Our advanced facilities, experienced team, and commitment to precision ensure that every part we produce exceeds industry standards.
Whether you require a complex, high-performance part for aerospace or a precise medical device component, Yonglihao Machinery has the expertise and technology to bring your design to life with unparalleled quality and efficiency. From prototyping to large-scale production, we offer investment casting solutions that are tailored to your specific requirements.
Conclusion
Investment casting is a highly versatile and precise manufacturing method that offers significant benefits for producing complex parts in various industries. By combining traditional techniques with modern innovations, Yonglihao Machinery continues to provide industry-leading investment casting services that help businesses achieve their production goals efficiently and cost-effectively.
For more information about our investment casting services or to discuss your next project, contact Yonglihao Machinery today. Let us help you bring your ideas to life with the precision and quality that only investment casting can deliver.
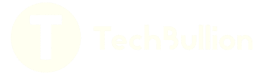