A steam trap is an automatic valve used to discharge condensed steam (condensate) and non-condensable gasses with little escape of steam. Steam traps are used in heating systems or mechanical processes to ensure steam is not wasted.
Steam traps are an effective and essential part of a piping system as they help conserve energy by preventing the escape of steam. Any wastage of steam can lead to a loss in the total efficiency and productivity of the running plant.
To fully understand their importance, we will be examining the functions of a steam trap in a piping system, as well as the different types of steam traps in the market and common steam trap problems.
Why Do You Need A Steam Trap in a Piping System
Steam traps are essential in a piping system because:
- Steam traps remove air and non-condensable gasses from the system in which it is installed. This function is necessary for steam to enter the equipment.
- The steam trap is also designed to close in the presence of steam. This will prevent the loss of steam before the heating potential is realized.
- To Discharge Condensed Steam (Condensate): A piping system will produce condensed steam (condensate) as a result of the cooling process. This condensed steam will accumulate in the piping system and can cause damage if it is not properly discharged. A steam trap will discharge the condensed steam so that it does not accumulate and cause damage.
- To Discharge Non-Condensable Gasses: A piping system will also produce non-condensable gasses as a result of the cooling process. These gasses can be harmful to the equipment in the piping system if they are not properly discharged.
A steam trap will discharge the non-condensable gasses so that they do not accumulate and cause damage.
- A steam trap is needed in a piping system to stop latent heat loss, increase efficiency in a heating system and reduce the cost of heating, and facilitate the separation of non-condensable gasses like carbon dioxide.
- Finally, Steam traps can help to prevent water damage by draining condensate from the system and extend the life of equipment by preventing corrosion.
Types of Steam Traps
There are different types of steam traps available on the market, and each type has its own set of benefits and drawbacks.
Mechanical Traps
Mechanical traps use the movement of a float to open and close the trap. As the float moves up and down, it opens and closes the valve. Mechanical traps are reliable and have a long lifespan. However, they can be clogged by debris, and they are not as responsive as other types of traps.
Thermostatic Traps
Thermostatic traps use a sensing element to open and close the trap. As the temperature of the steam changes, the sensing element opens and closes the valve.
Thermostatic traps are more responsive than mechanical traps and can hold back some condensate until it is cooled enough to allow the opening of the trap valve. This is actually one of the major drawbacks of a thermostat trap as condensates need to be discharged as they are formed.
Thermodynamic Traps
Thermodynamic traps use the difference in density between steam and condensate to open and close the trap. As the steam condenses, the density of the condensate increases and the trap opens. When the steam is gone, the trap closes.
Thermodynamic traps are very responsive and can handle large loads of condensate.
How To Select the Right Steam Trap for Your Application
There are a few factors to consider when selecting the right steam trap for your application.
The pressure of the System
The operating pressure is the maximum pressure that the system can operate at. Select a steam trap that can handle the operating pressure of the system. The pressure of the system will also affect the performance of the steam trap.
In general, steam traps can handle a wide range of pressures, but there are some steam traps that are designed specifically for high-pressure or low-pressure systems.
The temperature of the System
The temperature of the system will also play a role in the overall performance of the steam trap. For example, if the system is operating at a very high temperature, the steam trap will need to be able to withstand that temperature without failing.
Conversely, if the system is operating at a very low temperature, the steam trap will need to be able to open and close properly despite the low temperature.
Type of System
The type of system will also play a role in the performance of the steam trap. Closed systems are sealed and do not allow air to enter. Open systems are not sealed and allow air to enter.
The capacity of the System
The capacity of a condensate return system should be based on the maximum heat loss from all connected steam traps. The total heating surface, expressed in square feet, can be determined by adding the surface areas of all connected radiators, coils, and heat exchangers.
Common Problems of Steam Traps
There are common problems that are associated with steam traps such as; freeze-up, steam binding, air binding, pressure drops or surges, and water hammers. Steam trap failures can be problematic and lead to disastrous effects such as reduced efficiency, waste of energy, and increased costs of production.
To detect a steam trap failure easily and manage the issue effectively, it is usually advisable to have a steam trap monitor installed. This will help provide accurate failure alert reporting and prevent downtimes in production.
Wrapping Up
Steam traps are an essential part of piping systems. Without them, not only will there be physical damage to industrial piping systems, but there will also be a significant negative impact on production and other industrial processes.
As a matter of necessity, in every industry where there is an application for steam traps, there must be measures put in place to ensure the maximum functionality of the steam traps.
There are steam trap monitor solutions that are built to help businesses squeeze out the most use from their piping systems without hassle. Businesses can deploy them to cut production costs, increase functionality, and anticipate and manage disruptions.
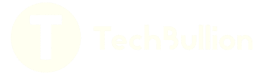