Overview
Level sensors are essential devices in various industries, playing a crucial role in monitoring and controlling the level of liquids, powders, and other substances within containers or tanks. They provide accurate and reliable information about the amount of material present, ensuring efficient operations, preventing overflows or underflows, and maintaining overall process control. From the food and beverage industry to chemical processing, water treatment, and oil and gas sectors, level sensors are indispensable tools for optimizing production processes and ensuring safety.
Introduction to Level Sensors
Types of Level Sensors
Contact Level Sensors
Capacitive Level Sensors
Capacitive level sensors are versatile and widely used for detecting the level of both conductive and non-conductive materials. They operate on the principle of capacitance, which changes when the sensor comes into contact with the material being measured. The sensor consists of two electrodes, typically a probe and the container wall, which form a capacitor. When the material level rises and comes into contact with the probe, the dielectric constant of the material affects the capacitance value. This change in capacitance is then converted into a level measurement signal.
Capacitive level sensors have several advantages. They are non-invasive, meaning they do not require direct contact with the material, which makes them suitable for applications with corrosive or viscous substances. They can also handle a wide range of materials, including liquids, powders, and granules. However, they may be affected by changes in the dielectric constant of the material, which can lead to inaccuracies in measurement. Proper calibration and compensation techniques are often required to ensure accurate readings.
Conductive Level Sensors
Conductive level sensors are used primarily for liquid level detection and are based on the conductivity principle. These sensors consist of a probe that is immersed in the liquid. When the liquid level reaches the probe, an electrical circuit is completed, allowing current to flow. The presence or absence of current flow indicates the level of the liquid.
Conductive level sensors are simple and cost-effective, making them suitable for applications where high precision is not required. They are commonly used in water treatment plants, fuel tanks, and other liquid storage systems. However, they are limited to conductive liquids and may not be suitable for non-conductive materials. Additionally, the presence of impurities or contaminants in the liquid can affect the conductivity and, consequently, the accuracy of the level measurement.
Float Level Sensors
Float level sensors are mechanical devices that use a buoyant float to detect the level of a liquid. The float is attached to a stem or a rod, which moves up and down as the liquid level changes. The movement of the float is then converted into an electrical signal or a mechanical indication of the level.
Float level sensors are reliable and easy to install, making them popular in a variety of applications. They are commonly used in fuel tanks, water tanks, and other liquid storage systems. They can handle a wide range of liquid densities and are not affected by changes in the dielectric constant or conductivity of the liquid. However, they require regular maintenance to ensure the float and stem are free from debris and corrosion. Additionally, the mechanical nature of these sensors can lead to wear and tear over time, which may affect their accuracy and reliability.
Non-Contact Level Sensors
Ultrasonic Level Sensors
Ultrasonic level sensors are non-contact devices that use sound waves to measure the level of a material. They emit high-frequency ultrasonic waves that travel through the air and reflect off the surface of the material. The sensor then measures the time it takes for the reflected waves to return, which is used to calculate the distance to the material surface and, consequently, the level of the material.
Ultrasonic level sensors are versatile and can be used for both liquid and solid materials. They are non-invasive and do not require direct contact with the material, which makes them suitable for applications with corrosive or hazardous substances. They are also relatively easy to install and maintain. However, they can be affected by environmental factors such as temperature, humidity, and dust, which can interfere with the sound wave propagation and lead to inaccurate measurements. Proper calibration and compensation techniques are often required to ensure accurate readings in different environmental conditions.
Radar Level Sensors
Radar level sensors are advanced non-contact devices that use electromagnetic waves to measure the level of a material. They emit radar signals that travel through the air and reflect off the surface of the material. The sensor then measures the time it takes for the reflected signals to return, which is used to calculate the distance to the material surface and, consequently, the level of the material.
Radar level sensors offer several advantages over other types of level sensors. They are highly accurate and can handle a wide range of materials, including liquids, powders, and granules. They are also unaffected by changes in the dielectric constant or conductivity of the material, making them suitable for applications with varying material properties. Additionally, they are not affected by environmental factors such as temperature, humidity, and dust, which makes them highly reliable in harsh industrial environments. However, they are more expensive than other types of level sensors and require specialized installation and calibration techniques.
Optical Level Sensors
Optical level sensors use light to detect the presence or absence of a material. They consist of a light source and a photodetector, which are typically mounted on opposite sides of a container or tank. When the material level rises and covers the light source or photodetector, the light path is interrupted, indicating the level of the material.
Optical level sensors are simple and cost-effective, making them suitable for applications where high precision is not required. They are commonly used in liquid level detection systems, such as fuel tanks and water tanks. However, they are limited to applications where the material is transparent or semi-transparent to light. Additionally, they can be affected by changes in the refractive index of the material, which can lead to inaccuracies in measurement.
Applications of Level Sensors
Industrial Applications
In industrial settings, level sensors are crucial for process control and automation. They are used in chemical processing plants to monitor the level of raw materials, intermediates, and finished products in storage tanks and reactors. Accurate level measurements ensure that the correct amounts of materials are used in the production process, preventing overflows and underflows that can lead to production delays and safety hazards.
In the food and beverage industry, level sensors are used to monitor the level of ingredients in mixing tanks, storage silos, and packaging lines. They ensure that the correct amounts of ingredients are added to the production process, maintaining product quality and consistency. Additionally, level sensors are used in water treatment plants to monitor the level of water in storage tanks and reservoirs, ensuring that the water supply is maintained at optimal levels.
Oil and Gas Industry
In the oil and gas industry, level sensors are used in various applications, including crude oil storage tanks, natural gas storage facilities, and offshore platforms. Accurate level measurements are essential for ensuring the safe and efficient storage and transportation of oil and gas. Level sensors are also used in refineries to monitor the level of liquid hydrocarbons in distillation columns and storage tanks, ensuring that the production process operates smoothly and safely.
Environmental Monitoring
Level sensors are also used in environmental monitoring applications, such as groundwater level monitoring and flood detection. In groundwater level monitoring, level sensors are installed in wells to measure the water level, providing valuable data for water resource management and environmental studies. In flood detection systems, level sensors are used to monitor the water level in rivers, lakes, and other bodies of water, providing early warning of potential flooding events and allowing for timely evacuation and mitigation measures.
Selection Criteria for Level Sensors
Choosing the right level sensor for a specific application requires careful consideration of several factors, including the type of material being measured, the operating environment, the required accuracy and precision, and the available budget. The following are some key selection criteria to consider when choosing a level sensor:
Material Compatibility
The level sensor must be compatible with the material being measured. For example, if the material is corrosive or abrasive, the sensor should be made of materials that can withstand these conditions. Additionally, the sensor should be suitable for the specific type of material, whether it is a liquid, powder, or granule.
Operating Environment
The operating environment can significantly affect the performance and reliability of a level sensor. Factors such as temperature, humidity, pressure, and the presence of dust or other contaminants should be considered. For example, in a high-temperature environment, a sensor that can withstand extreme temperatures should be selected. Similarly, in a dusty environment, a sensor that is not affected by dust particles should be used.
Accuracy and Precision
The required accuracy and precision of the level measurement depend on the specific application. For example, in a chemical processing plant where precise control of material levels is critical, a highly accurate level sensor should be used. In contrast, in a water storage tank where a rough estimate of the water level is sufficient, a less accurate sensor may be suitable.
Budget
The cost of level sensors can vary significantly depending on the type and features of the sensor. While it is important to select a sensor that meets the application requirements, it is also essential to consider the available budget. In some cases, a more expensive sensor may offer better performance and reliability, but in other cases, a less expensive sensor may be sufficient for the application.
Conclusion
Level sensors are vital tools in various industries, providing accurate and reliable level measurements for a wide range of applications. With the variety of level sensor types available, it is important to carefully consider the specific requirements of the application when selecting a sensor. By choosing the right level sensor, industries can optimize their production processes, ensure safety, and maintain efficient operations. As technology continues to advance, level sensors will continue to play a crucial role in modern industrial automation and process control.
Related Articles
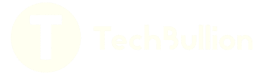