Recent studies have unveiled groundbreaking methods for analyzing stress distribution in mechanical joints, such as bolted and pinned connections, using Thermoelastic Stress Analysis (TSA). This research, conducted with meticulous experimental setups and advanced analytical techniques, offers critical insights into the behavior of mechanical fasteners, which are essential components in various structural and mechanical systems. The findings could significantly influence industries where bolted joints are crucial, such as aerospace, automotive, and civil engineering.
Bolted and pinned joints are ubiquitous in mechanical and structural systems, serving as the primary means of connecting separate components. These joints play a vital role in maintaining the integrity of structures, but they are often considered potential weak points due to the complex stress distributions that occur at the interfaces, such as between the bolt and plate. Traditional methods for analyzing these stresses, including both analytical and numerical approaches, frequently struggle to provide accurate predictions, particularly when boundary conditions are not well-defined.
Thermoelastic Stress Analysis (TSA) emerges as a powerful tool to address these challenges. TSA is an experimental technique that measures temperature changes in a material subjected to cyclic loading. These temperature changes directly correlate with the stress distribution within the material, offering a detailed map of how stresses are distributed across the joint. The studies in question harness TSA in conjunction with an Airy stress function, a mathematical approach used to simplify the complex equations governing stress fields in two-dimensional elasticity problems, to achieve a more accurate and comprehensive analysis of stress in bolted and pinned joints.
The primary objective of this research was to utilize TSA, coupled with the Airy stress function, to accurately determine the stress components in pin-loaded plates—an essential part of mechanical fasteners. The researchers aimed to overcome the limitations of traditional stress analysis methods by providing a full-field, detailed understanding of stress distribution, particularly at the critical interfaces between the pin and plate.
The experimental setup involved using aluminum plates with steel pins inserted into holes with slight diametral clearances. These plates were subjected to sinusoidal loading to simulate real-world conditions. The TSA data was collected using a state-of-the-art liquid nitrogen-cooled infrared camera, capable of capturing the minute temperature changes that occur under cyclic loading. This temperature data was then processed through the Airy stress function, allowing for the calculation of individual stress components across the entire plate, including at the crucial pin-plate interface.
Key parameters in the experiment included the use of a 6061 T6511 aluminum plate and a 4140 steel pin, both selected for their relevance in practical engineering applications. Precise measurements of the pin-hole clearance and other dimensions were taken to ensure the accuracy of the stress analysis. The research also incorporated traction-free boundary conditions, which were iteratively applied to refine the points at which the pin and plate lose contact under load. This approach enabled a more accurate representation of the real stress conditions that occur in mechanical joints.
The research yielded several significant findings that validate the effectiveness of the hybrid TSA approach. One of the key discoveries was that the total contact area between the pin and the hole exceeded 180°, a result confirmed by residual markings observed on both the pin and the hole after testing. This finding indicates that the hole deforms under load, leading to increased contact with the pin, which in turn affects the overall stress distribution within the joint. This behavior is crucial for understanding how mechanical joints perform under load and highlights the importance of accounting for such deformations in design and analysis.
Additionally, the TSA results showed strong correlation with predictions from Finite Element Method (FEM) analyses, further validating the accuracy of the TSA approach. One of the major advantages of TSA, as demonstrated by this research, is its ability to determine the individual components of stress without the need for knowing the material’s elastic modulus. This capability sets TSA apart from other experimental methods, such as moiré, holography, speckle, or digital image correlation, which often require detailed knowledge of the material properties or involve more complex data processing.
The research also highlighted TSA’s versatility and convenience. Unlike other methods, TSA does not require the use of a photoelastic model, surface pattern, or ruling. It provides a straightforward yet powerful means of analyzing stress distribution in mechanical joints, making it a valuable tool for engineers and researchers seeking to improve the design and safety of these critical components.
The findings from this research have significant implications for industries where bolted and pinned joints are integral to structural integrity. By providing a more accurate and detailed understanding of stress distribution, the hybrid TSA approach can lead to better-informed design decisions, improved safety, and increased durability of mechanical systems. This is particularly relevant in fields such as aerospace, automotive, and civil engineering, where the failure of a single joint can have catastrophic consequences.
Moreover, the research contributes to the ongoing development of more reliable and effective methods for stress analysis in mechanical fasteners. The hybrid TSA technique addresses many of the limitations of traditional methods, offering a robust tool for engineers and researchers alike. As the demand for safer and more efficient structural designs continues to grow, the insights gained from this research are likely to pave the way for future innovations in the field.
In conclusion, these studies demonstrate the power and versatility of Thermoelastic Stress Analysis when combined with advanced analytical techniques like the Airy stress function. The research not only advances our understanding of stress distribution in mechanical fasteners but also provides a practical tool for improving the design and safety of these essential components. As industries continue to seek out ways to enhance structural integrity, the findings from this research are poised to play a pivotal role in shaping the future of mechanical joint analysis.
For more information about this research or to request interviews with the researchers, please contact: A. A. Khaja (Department of Mechanical Engineering, University of Wisconsin, Madison, WI, 53706, USA), A. R. Kaliyanda ( Cummins, Inc., Columbus, IN, 47202, USA), Wael A. Samad ( Department of Mechanical Engineering, University of Wisconsin, Madison, WI, 53706, USA), & R. E. Rowlands (Department of Mechanical Engineering, University of Wisconsin, Madison, WI, 53706, USA). https://link.springer.com/chapter/10.1007/978-1-4614-4235-6_14 and https://link.springer.com/article/10.1007/s11340-013-9822-6
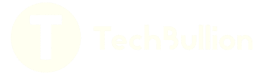