Aminur Rahman is blending mechanical engineering with automation and sustainability to shape a greener future for industries across the globe.
After making a significant impact in EV battery remanufacturing, he’s now bringing his expertise to the biotech sector. So how does he leverage his unique skill set to optimize manufacturing processes across diverse industries?
Aminur Rahman, a leading manufacturing expert, brings his extensive experience in the textile, automotive, and electric vehicle (EV) industries into the biotechnology sector.
“My move came from a desire to apply my skills in a new, meaningful way,” Rahman explains. “Both fields demand a focus on precision, sustainability, and innovation — whether it’s extending the life of EV batteries or improving processes in life sciences.
His diverse experience, from ERP Consultant to Design Engineer and beyond, has sharpened his expertise and given him valuable insights into how automation can transform various industries.
Groundbreaking Research for Sustainable Businesses
Rahman began exploring innovative manufacturing approaches over a decade ago. In his study on designing compound pressure vessels, published in the Global Journal of Research in Engineering, he discussed industries that manage high-pressure gasses, such as aerospace.
Unlike traditional pressure vessels, which can be bulky and material-intensive, Rahman’s study focuses on a compound design that reduces the amount of material needed while still maintaining safety and reliability.
“This kind of innovation could not only lower costs but also improve the efficiency of industries that rely on these vessels,” Rahman explained. Advanced simulation tools like SolidWorks and ANSYS allowed Rahman to model and test the compound vessel under various conditions, such as high pressure and temperature changes, without the need for costly real-world experiments.
“The results showed that the compound design not only performed better than traditional vessels but also withstand more stress with less material,” Rahman explained. “That’s a huge win for industries looking to be both cost-effective and environmentally conscious.”
Though the research hasn’t yet been applied in a practical setting, the findings have the potential to revolutionize how industries think about pressure vessel design.
“By minimizing material usage while enhancing safety, this compound design has the potential to revolutionize sustainable manufacturing practices,” Rahman explained. “This could significantly benefit industries that prioritize efficiency and innovation.”
Blending Mechanical and Electrical Expertise
Rahman’s engineering career began in one of Asia’s leading ready-made garment manufacturers. He’s been working on machinery design, finite element analysis (FEA), and integrating sensors and control systems for better monitoring and reliability.
“In the emerging markets, we have to customize existing equipment to align with customer needs,” Rahman said. “It’s about innovation with the resources you have.”
Later, at Grand Valley State University (GVSU), he focused on bridging the gap between mechanical and electrical engineering.
“When you design automation systems, you need to understand both sides — the mechanical and the electrical,” Rahman explains. “That’s how you make automation smarter and more efficient.”
He also worked on developing advanced learning modules and programmed PLCs (Programmable Logic Controllers) to streamline production cycles.
His work helped companies produce more parts in less time with fewer defects. Additionally, he integrated robotics into the production lines, optimizing material handling, assembly, and welding processes.
Extending the Life of EV Batteries
Rahman’s expertise has been instrumental in developing remanufacturing processes for electric vehicle (EV) components, particularly focusing on EV batteries.
“Our innovative techniques allow us to evaluate faulty batteries, pinpoint the issues, and repair or replace just the damaged components,” he explained. “This approach not only extends the lifespan of the battery but also significantly reduces waste.”
Rahman’s approach to remanufacturing involves a detailed process of disassembling battery packs, diagnosing faults, replacing damaged modules and components, and reassembling the batteries. This method not only reduces the need for new raw materials, such as lithium and cobalt, but also cuts down on the environmental impact of discarded batteries.
“My goal is to promote sustainability through efficient recycling,” Rahman explains. “By using recycled materials, we reduce the need for new mining operations, which has a significant environmental benefit.”
Rahman is optimistic about the future of innovation across a range of industries, particularly as he ventures into the biotech space. “Automation is about enhancing intelligence in production processes,” he said. “By focusing on process optimization in manufacturing we’re not just improving efficiency; we’re actively contributing to a more sustainable future.”
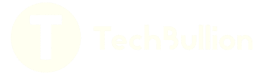