Materials testing is a key component of quality assurance in a number of industries. These tests verify that materials meet the necessary standards for strength, durability, and performance. While the focus often falls on sophisticated testing equipment, consumables-such as abrasive papers, test specimens, and mounting compounds-are equally vital. These seemingly small components can have a significant impact on test results accuracy and reliability.
High-quality consumables work smoothly with testing equipment, minimizing variability and resulting in consistent outcomes. On the other hand, substandard consumables introduce uncertainties that compromise data integrity, potentially leading to costly errors and equipment wear.
The purpose of this article is to examine the importance of consumables in material testing, exploring how their quality affects test accuracy. It will also highlight the risks of using inferior consumables and provide best practices for selecting and maintaining these important components. By understanding their significance, you can make informed choices to ensure accurate, reliable, and repeatable testing results.
The Impact of Consumable Quality on Test Accuracy
The accuracy of material testing heavily depends on the quality of consumables used during the process. High-quality consumables are engineered to deliver consistent performance, eliminating variables that can distort test results.
Premium consumables are manufactured according to quality standards, guaranteeing uniform properties. For example, the abrasive materials used in sample preparation provide a consistent surface finish, which is critical for accurate hardness and microstructural analyses. Similarly, standardized test specimens enable repeatable results across different testing sessions, reducing error margin.
Contamination is a common issue that impacts test results. High-quality consumables prevent this risk by maintaining purity throughout production. Clean and uncontaminated mounting materials, for instance, make sure that microscopic evaluations remain clear and accurate, free from external interference.
Using quality consumables also protects testing equipment. Subpar materials can cause unnecessary wear and tear, leading to frequent maintenance or costly repairs. For example, using well-made polishing cloths minimizes abrasive damage to polishing machines, extending their operational life and maintaining performance.
Risks Associated with Inferior Consumables
While it might be tempting to cut costs by using cheaper consumables, the long-term risks far outweigh the initial savings. Inferior consumables compromise material testing accuracy but also lead to operational inefficiencies and equipment damage.
Low-quality consumables often vary in composition and performance. This inconsistency can result in unreliable test data, making it difficult to assess material properties accurately. For instance, using poorly manufactured abrasive papers might produce uneven finishes on test specimens, leading to errors in hardness or tensile strength measurements. Such discrepancies can hinder compliance with industry standards and affect product quality.
Substandard consumables can significantly impact testing equipment lifespan and functionality. Abrasives that are overly harsh or improperly designed can wear out polishing machines or grinding wheels. Similarly, poor-quality mounting compounds may clog or damage microscopic evaluation tools. Over time, these issues lead to increased maintenance needs, unplanned downtime, and expensive repairs or replacements.
Although inferior consumables might seem cost-effective initially, their frequent replacement and the additional time required for troubleshooting errors can lead to higher overall expenses. Moreover, inaccurate test results can result in product recalls, delays, or reputational damage, further amplifying costs. Investing in high-quality consumables from the outset is a cheaper choice in the long run.
Best Practices for Selecting and Maintaining Consumables
To maximize material testing accuracy and avoid risks associated with inferior consumables, it is critical to adopt best practices in their selection and maintenance. These measures increase test reliability and improve operational efficiency.
Start by sourcing consumables from reputable suppliers known for consistent quality. Verify that the products meet industry standards, such as ASTM or ISO, to confirm compatibility with your testing requirements. Request certifications or quality assurance documentation to validate their performance.
Make sure that the consumables you select are suitable for both the materials being tested and the testing equipment. For example, using abrasives that match the hardness of your test material can prevent excessive wear on surfaces and deliver more accurate results. Similarly, choose mounting compounds that do not react with the material being analyzed to avoid distortions in microscopic evaluations.
Establish a regular inspection schedule to identify signs of wear, contamination, or degradation. Replace items as necessary to maintain testing consistency. For instance, dull abrasive papers or worn polishing cloths should be discarded promptly to avoid compromising surface quality during sample preparation.
Training personnel on the importance of using high-quality consumables and the proper methods of handling and storing them. Develop standard operating procedures (SOPs) that outline cleaning, usage, and replacement protocols. Following these guidelines enhances consistency and reduces errors during testing.
Investing in Quality Consumables for Accurate Testing
Material testing accuracy and reliability are directly influenced by the quality of the consumables used. High-quality consumables contribute to consistency, minimize contamination risks, and protect testing equipment from unnecessary wear and damage. Conversely, using inferior materials can lead to unreliable results, increased operational costs, and even long-term harm to testing systems.
To maintain testing precision, it is essential to adopt best practices. These include sourcing consumables from reputable suppliers, assuring material compatibility, and implementing regular inspection and replacement routines. Additionally, training staff and enforcing standard operating procedures helps maintain testing integrity and extend consumable lifespan.
Investing in quality consumables is not merely an operational expense—it is a strategic decision that increases material testing accuracy, efficiency, and reliability. By prioritizing this often-overlooked aspect of testing, organizations can safeguard their results, optimize costs, and uphold the highest standards in material evaluation.
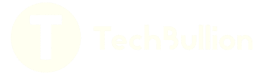