Efficiency in operations is everything when you’re running a warehouse. You and your staff need to be able to find items quickly, because late shipments can mean lost customers, increased operating costs, and even the loss of your warehousing business.
But these days, it’s easier than ever to operate your warehouse efficiently and well. There are so many tools at your disposal, from processes and strategies, to software and gadgets. These five tips will help you improve your warehouse shipping processes, for reduced costs, happier customers, and more motivated employees.
1) Optimize Your Warehouse Layout
When your warehouse floor plan is optimized, your staff will operate better and turn around inventory faster, and that will mean reduced operating costs on your end. Design your warehouse layout so that space is used effectively, but also consider the needs of traffic flow, work processes, and storage. Popular items that are shipped more often should be easily accessible, while less popular items can be stored in a less accessible location. Multiple pick-pack-and-ship work stations might be in order, especially for your most popular items.
Don’t rest on your laurels when it comes to layout design. You’ll never find a warehouse layout that meets all of your needs for the life of your business — things change, sometimes rapidly, and it’s worthwhile to reevaluate your warehouse layout quarterly to see if you can’t reorder some processes or rearrange some parts of the layout.
2) Document, Document, Document
Documentation might seem tedious, but it’s necessary if you want to run your warehouse right. Recording shipments as they arrive and documenting where items are stored in the warehouse can help your teams function at maximum efficiency. Documenting processes can help you streamline them, and documenting costs can help you pinpoint potential savings. You can save a lot of time and money simply by documenting and reviewing processes and costs.
Of course, you’ll also need to track metrics to determine whether your cost-saving measures are actually saving any costs and whether your processes are as efficient as they could be. Measure key metrics, like return on investment, as you work to optimize performance and minimize costs.
3) Harness Technology
From order tracking software to RFID tracking tags and impact sensors, you have a wealth of technological tools at your disposal to improve your warehouse processes. Automating your warehouse is a must if you’re still using manual processes to record and track inventory. RFID trackers can automatically record shipments and their contents as they arrive, eliminating the need for human employees to spend time examining shipments and scanning in items. You can use impact sensors to track the conditions shipments are exposed to in transit, so you can identify potential sources of damage and make necessary changes to your supply chain to address them. Many logistics companies have realized savings of up to 60 percent in shipping costs as a result of using shock and vibration sensors to reduce shipping damage.
4) Balance Inbound, Outbound, and In-Stock Movements
The physical movement of stock through your warehouse needs to be synchronized like a carefully choreographed ballet. When in-bound, outbound, and in-stock movements are not properly synchronized, in-bound stock can get in the way of removing outbound stock, creating physical bottlenecks that result in frustration and longer order processing times. Stock that is not regularly moved out of the warehouse is stock that is just sitting there, taking up space that could be filled with more popular items that will sell faster and make you more money. Items that aren’t in stock but are in demand cause similar losses.
There’s an art and science to making sure your inventory levels are just right at all times, and that your levels of in-bound, outbound, and in-stock inventory are optimized. Try the Just in Time (JIT) inventory management technique to balance stock movements. This highly synchronized method of inventory control can help save you money by minimizing the number of goods in the supply chain.
5) Limit Options to Say Organized
Staff are most likely to work efficiently when they have minimal options. The fewer shipping carriers you have to choose from or the fewer package sizes available to pick-and-pack teams, the less time will be wasted on making these choices. Standardize processes and work to make sure that team members understand their tasks, and that those tasks don’t overlap. Processes should contain the minimum number of steps needed to complete them, and workstations should contain the minimum number of supply options without depriving teams of what they need.
Optimizing warehouse layouts can make sure that the most popular items are right to hand for staff that need them. Reducing packing supply and equipment options cuts down on the amount of time spent on choices like container size or packing material. Rather than rendering teams less effective, providing the minimum equipment necessary to get the job done right can help team members perform tasks more quickly and easily.
There’s room for process improvement in many warehouses, especially since shipping and logistics can be such a dynamic industry. Stay on top of your warehouse shipping processes, and always be on the lookout for ways to optimize efficiency and cut costs. Like a rosebush under the care of a thoughtful gardener, your warehouse will grow and thrive as a result.
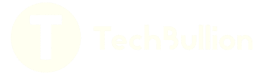