Plastic injection mould are complicated machines that require precision and consistency. They create plastic parts from various materials, including polypropylene, polyvinyl chloride, polyethylene, and more. Injection mould produces millions of products worldwide and can be found in multiple industries, from automotive to medical device manufacturing. As such, businesses must understand the importance of consistency in plastic injection mould processes.
This blog post will discuss why consistency is so important in plastic injection moulding and how businesses can ensure they have the best outcomes.
What is Consistency in Plastic Injection Mould?
When it comes to plastic injection moulds, consistency is critical. This means the mould must be uniform in shape and size, with no irregularities. The slightest imperfection can cause problems during the injection process, resulting in an uneven or deformed final product.
The mould must be made from high-quality materials and machined to precise specifications to ensure consistency. It is also essential to regularly check and maintain the mould to keep it in good condition. With proper care, a plastic injection mould can last for many years and produce thousands of perfect parts.
The Process of Plastic Injection Mould
The process of plastic injection mould is a manufacturing process that is used to create large numbers of identical parts or products. Injection mould is widely used for the mass production of plastic parts, including medical devices, consumer products, and components for the automotive industry.
Injection moulding consists of four main steps:
- The first step is to heat the plastic material until it is molten. This is typically done with a screw-type injection moulding machine, which uses a reciprocating screw to force the material through a heated barrel and into the mould cavity.
- The second step is injecting molten material into the mould cavity. This is done under high Pressure, and the material is injected into the cavity very quickly to cool and solidify before it flows out of the hole.
- The third step is to hold the Pressure while cooling occurs. This helps ensure that the product retains its shape during cooling.
- Finally, once cooled, the product can be ejected from the mould cavity and trimmed of any excess material (flash).
Importance of Consistency
It is essential to be consistent when plastic injection moulding to produce high-quality, repeatable parts. The process of plastic injection moulding involves injecting molten plastic into a mould cavity. The cavity is then cooled so that the plastic solidifies and takes on the shape of the hole.
Maintaining a consistent process to produce compatible, high-quality parts is essential. This means ensuring that the temperature of the molten plastic is constant, as well as the Pressure and speed at which it is injected into the mould.
It is also essential to ensure that the mould is consistently cooled so that the parts do not warp or deform. By being consistent with the process, it is possible to produce high-quality, repeatable parts with minimal defects.
The benefits of consistency in plastic injection mould
One of the main benefits of consistency in plastic injection mould is that it helps to ensure that products are manufactured to the same high standards. This is because all of the products produced using the same mould will be precisely the same, meaning there is no need for quality control checks on each product. This, in turn, leads to savings in time and money.
Another benefit of consistency is that it helps build a reputation for quality. If customers know they can rely on a company to produce consistently high-quality products, they are likelier to continue doing business with them. This can lead to long-term relationships and repeat business.
Finally, consistency also makes it easier to train staff and new employees. If everyone knows that the products will always be made the same way, it is much simpler to learn how to use the machinery and carry out the manufacturing process. This can save a lot of time and hassle in the long run.
Conclusion
Consistency in plastic injection mould is critical for the quality of a product. Achieving consistency requires careful attention to the processes of designing, prototyping, tooling, and production. With the proper knowledge and experience, it’s possible to consistently create high-quality parts that meet customer specifications.
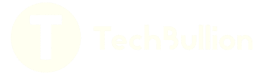