Introduction
Efficient manufacturing and supply chain process management is crucial for organizations to streamline operations, optimize resources, and deliver high-quality products to customers. By implementing robust process management strategies, businesses can enhance productivity, reduce costs, and improve overall efficiency. In this blog post, we will explore the key considerations and best practices for implementing effective manufacturing and supply chain process management. We will focus on the purchase order approval process and the importance of utilizing the best vendor management systems. These insights will help organizations establish a strong foundation for success in their manufacturing and supply chain operations.
Streamlining the Purchase Order Approval Process:
The purchase order approval process plays a critical role in manufacturing and supply chain management. It ensures that all procurement activities adhere to the organization’s guidelines and requirements. Consider the following essential steps for streamlining this process:
Centralized Approval System: Implement a centralized system that allows for efficient purchase order creation, submission, and approval. This ensures clear visibility and accountability throughout the approval chain.
Standardized Workflows: Define standardized workflows that outline the steps and individuals involved in the approval process. This helps eliminate bottlenecks, reduce errors, and maintain consistency.
Automated Notifications: Utilize automated notifications to alert relevant stakeholders when a purchase order is awaiting approval. This enhances communication, expedites the process, and reduces delays.
Real-time Tracking: Implement a system that provides real-time tracking of purchase orders throughout the approval process. This enables stakeholders to monitor progress, identify potential issues, and take proactive measures.
Leveraging the Best Vendor Management Systems:
Effective vendor management is crucial for maintaining strong supplier relationships and ensuring timely delivery of high-quality materials and components. Here are some considerations when selecting and utilizing vendor management systems:
Vendor Performance Evaluation: Implement a system that allows for comprehensive evaluation of vendor performance based on key metrics such as quality, on-time delivery, and responsiveness. This facilitates data-driven decision-making and supports continuous improvement.
Supplier Collaboration: Choose a vendor management system that enables seamless collaboration and communication between your organization and suppliers. This promotes transparency, fosters strong partnerships, and helps resolve issues promptly.
Supplier Database Management: Utilize a system that centralizes supplier information, including contracts, certifications, and contact details. This ensures easy access to critical supplier data and facilitates efficient vendor onboarding and management.
Integration with ERP Systems: Integrate your vendor management system with your organization’s Enterprise Resource Planning (ERP) system. This allows for seamless data flow, from purchase orders to inventory management, enhancing operational efficiency and accuracy.
Continuous Improvement and Data Analysis:
To drive efficiency and optimize manufacturing and supply chain processes, organizations should embrace continuous improvement and data analysis. Consider the following practices:
Performance Metrics and KPIs: Define and track key performance metrics and Key Performance Indicators (KPIs) that align with your organization’s goals. These metrics can include cycle time, lead time, on-time delivery, and inventory turnover. Regularly analyze the data to identify areas for improvement.
Root Cause Analysis: Conduct root cause analysis to identify the underlying causes of process inefficiencies or supply chain disruptions. This enables organizations to implement targeted solutions and prevent recurring issues.
Supply Chain Visibility: Establish a system that provides end-to-end visibility of the supply chain, from raw material sourcing to final product delivery. This allows for proactive management of potential disruptions and helps organizations make informed decisions.
Collaborative Planning: Foster collaboration between different departments, such as manufacturing, procurement, and logistics, to ensure alignment and synchronization. This promotes efficiency, reduces lead times, and minimizes waste in the manufacturing and supply chain processes.
Risk Management and Contingency Planning:
Effective manufacturing and supply chain process management requires proactive risk management and contingency planning. Consider the following practices:
Risk Assessment: Conduct thorough risk assessments to identify potential risks and vulnerabilities within the manufacturing and supply chain processes. This includes evaluating risks related to supplier reliability, market fluctuations, geopolitical factors, and natural disasters.
Supplier Diversification: Implement a supplier diversification strategy to mitigate the risk of relying heavily on a single supplier. Engage multiple suppliers for critical materials or components to ensure continuity of supply.
Contingency Planning: Develop contingency plans for various scenarios such as supplier disruptions, production delays, or changes in market demand. This includes having alternative suppliers, safety stock, and flexible production capacity to adapt to unforeseen circumstances.
Collaboration with Suppliers: Foster collaborative relationships with suppliers to facilitate effective risk management. Regular communication, sharing of forecasts, and early engagement with suppliers can help anticipate and address potential issues before they escalate.
Conclusion:
Implementing efficient manufacturing and supply chain process management is crucial for organizations to achieve operational excellence, cost optimization, and customer satisfaction. By streamlining the purchase order approval process, leveraging the best vendor management systems, embracing continuous improvement and data analysis, and implementing risk management strategies, businesses can enhance productivity, reduce costs, and maintain a competitive edge. With strong process management practices in place, organizations can optimize their manufacturing and supply chain operations, navigate challenges effectively, and deliver high-quality products to customers in a timely manner. Invest in robust process management strategies and systems to drive success in the dynamic and ever-evolving manufacturing and supply chain landscape.
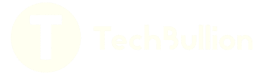