When it comes to manufacturing toys, safety and durability are non-negotiable. Toys must withstand rough handling, frequent drops, and rigorous playtime without falling apart.
One of the most effective ways to ensure both safety and durability in toys is through ultrasonic plastic welding technology.
In this article, we’ll explore how toys ultrasonic plastic welders work to create strong, reliable joints in plastic toys, ensuring that they meet safety standards while maintaining high durability. We’ll delve into the importance of ultrasonic welding in toy manufacturing, the advantages it offers, and how it plays a critical role in maintaining the safety of toys.
The Importance of Safety and Durability in Toys
Toys are a significant part of a child’s development and entertainment, but they are also regulated products. Stringent safety standards exist worldwide to ensure that toys are safe for children. These regulations govern various aspects, including the materials used, design, and assembly of toys.
- Durability: Toys need to be able to withstand the wear and tear of daily use. Whether it’s a plastic doll, an action figure, or a toy truck, it must endure being dropped, thrown, or bitten without falling apart.
- Safety: Toys must be free from harmful substances like lead, BPA, or phthalates. Moreover, they must be constructed in a way that minimizes risks like choking hazards. Small parts need to be securely attached, and the materials must not break into hazardous pieces during use.
This is where toys ultrasonic plastic welders come into play. By providing a clean, precise, and robust method for assembling plastic parts, these welders ensure that toys meet safety and durability standards, without relying on adhesives or mechanical fasteners that could break or degrade over time.
How Toys Ultrasonic Plastic Welders Work
Ultrasonic plastic welding is a process that uses high-frequency ultrasonic vibrations to create heat through friction, which causes materials to bond together. The energy from these vibrations causes the plastic to melt locally, and pressure is applied to form a strong bond once the material solidifies.
Key Components of a Toys Ultrasonic Welder
- Transducer: This converts electrical energy into high-frequency mechanical vibrations.
- Booster: This amplifies the ultrasonic energy.
- Horn (Sonotrode): The horn focuses the vibrations onto the plastic parts to create a localized heat source.
- Fixture/Anvil: This holds the parts in place under pressure during the welding process.
The Process of Ultrasonic Welding
The process begins when the plastic parts to be joined are positioned in the welding system. The toys ultrasonic plastic welder generates ultrasonic vibrations through a transducer. These vibrations are focused onto the plastic joint using the horn.
As the energy is applied, the plastic at the joint melts, and pressure is maintained to ensure a strong bond. Once the ultrasonic vibrations stop, the plastic solidifies, forming a robust, permanent bond between the parts.
The beauty of ultrasonic welding is that it creates a solid joint without requiring external materials like adhesives, screws, or nails. This results in a cleaner, faster, and more reliable process, especially when compared to traditional joining methods like gluing or mechanical fasteners.
How Ultrasonic Welding Ensures Durability in Toys
Below shows how ultrasonic welding ensures durability in toys.
1. Strong, Seamless Joints
Ultrasonic welding creates a seamless bond between plastic parts, which is especially important for toys that must withstand a lot of rough handling.
The heat generated during the process melts the plastic at the joining interface, allowing the materials to fuse together and form a solid bond once cooled. These welded joints are extremely strong, reducing the likelihood of breakage, even in high-stress areas.
- No Adhesives: Unlike toys that rely on adhesives to bond parts, ultrasonic welding creates a joint with the plastic itself, eliminating the risk of glue or adhesive degradation over time. As a result, toys welded with ultrasonic technology are more durable, and their components stay intact for longer periods.
- Precision: Toys ultrasonic plastic welders offer precision, allowing manufacturers to target specific areas for welding. This precision is crucial for ensuring that toy parts remain securely joined, even when subjected to the rough treatment typical of children’s play.
2. No Risk of Toxic Materials
In the toy industry, one of the major concerns is the use of toxic chemicals such as phthalates or BPA, often found in some adhesives or coatings.
These chemicals pose health risks and violate safety standards in many countries. Since ultrasonic welding uses no adhesives, it eliminates the need for these harmful materials in the joining process.
By relying on ultrasonic welding machine technology, manufacturers can ensure that toys are free from toxic substances. This is particularly important for children’s toys, as they are likely to come into direct contact with the mouth and skin during play.
3. Improved Impact Resistance
Toys often face the stress of being dropped, thrown, or crushed. Ultrasonic welding provides a more resilient bond that enhances the overall impact resistance of plastic toys.
In comparison to glued or riveted joints, ultrasonic welding joints maintain their integrity under higher forces, reducing the likelihood of the toy breaking apart or suffering from weak points.
4. Precision in Small Parts
In toys that contain small, intricate parts, ultrasonic welding ensures that even the smallest components are securely joined. For example, tiny toys with small limbs, eyes, or accessories benefit from plastic toys ultrasonic welder technology.
The precision of ultrasonic welding ensures that these smaller components are securely attached, reducing the risk of them detaching and posing a choking hazard to children.
How Ultrasonic Welding Ensures Safety in Toys
Safety is a top priority in toy manufacturing. Toys ultrasonic welders help manufacturers meet stringent safety standards by providing a method for securely attaching parts that are safe for children to handle.
1. Eliminating Small Detachable Parts
Many toys feature small components, such as buttons, figurines, or accessories, which can pose a choking hazard if not securely attached. With ultrasonic welders, small parts are joined tightly to the main body of the toy, ensuring that they don’t break off easily. This reduces the risk of a child swallowing or choking on small pieces.
2. Avoiding Sharp Edges
In addition to making strong bonds, ultrasonic welding can also help create smoother edges around the joint areas. The welding process melts the plastic in a controlled manner, preventing sharp edges that could potentially harm children. This is especially important in toys with complex shapes or detailed designs.
3. Compliance with Safety Standards
Ultrasonic welding systems play a key role in helping manufacturers meet international safety standards for toys. Regulations like EN71 (Europe), ASTM F963 (USA), and other international standards require toys to be robust, non-toxic, and free from small detachable parts.
Using ultrasonic welding ensures that toys meet these requirements, as it allows for stronger, more reliable joints that adhere to the highest safety standards.
Advantages of Toys Ultrasonic Plastic Welders in Toy Manufacturing
Toys ultrasonic plastic welders offer the following advantages:
1. High Production Speed
Ultrasonic welding systems are fast, which is crucial for toy manufacturers who often need to produce large volumes of products quickly. The process typically takes just a few seconds to complete, allowing for rapid assembly. With automated ultrasonic welding machines, manufacturers can achieve high throughput and efficiency without sacrificing quality.
2. Cost-Effectiveness
Ultrasonic welding is a cost-effective method for joining plastic parts. It reduces the need for expensive consumables such as adhesives, fasteners, or mechanical joints, which can increase production costs. Additionally, the speed and precision of ultrasonic welding reduce labor costs, further making it a budget-friendly solution for toy manufacturers.
3. Environmentally Friendly
Unlike traditional bonding methods that rely on adhesives or chemical agents, ultrasonic welding is an environmentally friendly process. It requires no solvents or chemicals, reducing emissions and waste. This makes it an attractive choice for toy manufacturers seeking sustainable manufacturing processes.
Conclusion
Toys ultrasonic plastic welders provide a reliable, efficient, and safe solution for manufacturing durable toys that meet the highest safety standards. By using ultrasonic welding technology, manufacturers can ensure that plastic parts are securely joined without the need for adhesives, screws, or fasteners.
This creates strong, durable joints that can withstand the wear and tear of daily play, while also ensuring the toys are free from harmful chemicals and small parts that could pose a choking hazard.
For those seeking more information or looking to explore handheld ultrasonic plastic welding machine solutions, Dizo ultrasonic welders offer innovative and flexible systems that can meet a wide range of production needs.
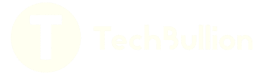