Air filter pleating machine is critical equipment in the filter manufacturing industry, ensuring precise pleating and forming of filter media for a variety of uses. Like any industrial machine, it relies on different systems to operate effectively, among which pneumatic systems play a key role in automation, pressure control, and pleat formation. However, pneumatic system problems can cause operational disruptions, reduced efficiency, increased downtime, and affect production quality. Common problems include air leaks, pressure fluctuations, actuator failures, and valve failures. Prompt identification and troubleshooting of these problems are essential to maintaining stable production and avoiding expensive repairs.
Identifying Common Pneumatic System Problems in Air Filter Pleating Machine
Before troubleshooting, it is essential to understand the common pneumatic system problems that may occur in air filter pleating machines. Some of the most common problems include Air leaks and drops in air pressure, which can cause incorrect pleating and reduce machine efficiency. Inconsistent air pressure and pressure fluctuations can affect the uniformity of pleats, resulting in product defects. Actuator failure, cylinders and other pneumatic components may not extend or retract properly. Clogged or dirty air filters and contaminated air can hinder airflow and cause the system to lose pressure. Solenoid valve failure and defective valves can prevent air from reaching necessary components.
Diagnosing air leaks in an air filter pleating machine pneumatic system
Air leaks are one of the most common problems in pneumatic systems, often resulting in reduced pressure and inefficient machine operation. Here’s how to identify and fix air leaks in an air filter pleating machine: Listen for a hissing sound. A high-pitched hissing sound usually indicates a leak in a hose, fitting, or seal.
Spraying soapy water on the pneumatic connections can reveal bubbles of air escaping. Inspect hoses and fittings for cracks, loose connections, or worn seals that could cause leaks. Tighten or replace components. Loose fittings should be fixed, and damaged hoses or seals replaced to restore air pressure. Regularly checking for air leaks can significantly improve machine performance and avoid unnecessary energy consumption.
Troubleshooting inconsistent air pressure
Inconsistent air pressure can cause irregular pleats, which can lead to filter failure and production delays. To troubleshoot air pressure fluctuations in an air filter pleating machine, follow these steps: Inspect the air compressor to ensure that the compressor is operating at the correct pressure setting and is not faulty. Check the pressure regulator to make sure that a faulty regulator can cause a drop or surge in pressure; adjust or replace it if necessary. Monitor the air supply line. Any blockage, leak, or restriction in the supply line can cause unstable pressure.
Drain water from the air system. Moisture buildup in the airlines can affect airflow and should be removed using an air dryer or drain valve. Maintaining steady air pressure is essential to producing high-quality pleats with uniform depth and consistency.
Fixing Actuator Failure in an Air Filter Pleating Machine
Pneumatic actuators, such as cylinders and pistons, play a vital role in the operation of an air filter pleating machine. If they fail, the machine may not be able to complete the pleating process correctly. Common causes of actuator failure include:
Air supply problems: If the actuator is not moving as expected, check that the air is reaching the actuator at the correct pressure.
Dirty or clogged actuator seals: Dirt and debris can impede actuator movement; cleaning or replacing the seals may solve the problem.
Lubrication problems: Pneumatic actuators require proper lubrication; dry or sticky cylinders may need oiling.
Worn Actuator Components: Internal wear can cause actuator failure, requiring repair or replacement.
Ensuring that the actuator is functioning properly is critical to smooth pleating operations and avoiding production interruptions.
Troubleshooting a Faulty Solenoid Valve
The solenoid valve controls the flow of compressed air within the air filter pleating machine. If the solenoid valve fails, air may not reach the necessary components, causing operational issues. Troubleshooting a faulty solenoid valve includes:
Checking electrical connections: Make sure the solenoid valve wiring is intact and connected properly.
Testing the valve coil: A burnt coil can cause the valve to not function properly; replace it if necessary.
Cleaning the inside of the valve: Dirt buildup can impede airflow; disassemble and clean the valve if necessary.
Verifying airflow through the valve: Use a pressure gauge to check that air is flowing as expected.
Preventive Maintenance of Pneumatic Systems
Troubleshooting pneumatic system problems in air filter pleating machines is critical to maintaining high productivity and ensuring consistent filter production. By identifying common problems such as air leaks, pressure fluctuations, actuator failures, clogged air filters, and solenoid valve failures, operators can take proactive steps to resolve these issues quickly. Implementing a preventive maintenance program can greatly reduce unexpected breakdowns. Regular inspections, timely replacements, and proper lubrication ensure that your pneumatic system operates at optimal efficiency.
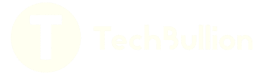