Manufacturing businesses cannot afford any downtime. When one area in a plant goes down, it affects other areas as well. Even one minute of downtime can have far-reaching consequences, and every minute counts when it comes to getting things up and running again. Fortunately, businesses find they can take steps to reduce the risk of downtime and minimize damage to their bottom lines. The following tips become of great help in keeping downtime to a minimum in any manufacturing organization.
Be Proactive
Preventative maintenance reduces unplanned downtime and can keep planned downtime to a minimum. Furthermore, preventative measures rely on knowing what needs to be done when. A digital log of all assets and the maintenance history associated with each becomes of great help at this time.
This log needs to include more than the date of the last maintenance service. It should include information about the length of time needed to complete each task in the process. This makes planning future maintenance tasks easier for all involved. In addition, this information becomes of great help in learning the effectiveness of preventative maintenance when it comes to minimizing downtime.
If computer systems do go down, it is helpful to have a managed IT services provider on call. The provider becomes of great help in getting these systems up and running again quickly. This gives the manufacturing plant owner peace of mind knowing they have kept downtime to the shortest period possible.
Communication Remains Key
Managers and employees must remain in constant communication to improve efficiency across departments. Individuals in authority positions need to emphasize the relationship between business profits and downtime. Never assume employees see the connection as supervisors do.
Furthermore, this communication makes employees feel as if they are a valuable part of the organization and their input is important when it comes to operational strategies. Employee engagement remains key to higher productivity, as happy and motivated employees contribute more to company efforts when it comes to minimizing downtime.
Create a Technology Plan
Technology continues to advance at a rapid rate. For this reason, every manufacturing plant needs a technology plan in place. Furthermore, this plan needs regular review to ensure it remains pertinent.
Modernizing the plant helps reduce unplanned downtime. Furthermore, it provides other benefits, such as allowing the business to budget for upgrades over a period rather than trying to find money to make upgrades all at one time.
Set Goals
Employees need to know what the company goals are. When they have this information, productivity improves, and errors become less common. This helps to increase uptime. Each employee knows where they fit into the process and can make suggestions on how to improve manufacturing processes.
Ask for their input when it comes to decreasing downtime. As they spend time on the line, they know what works and what doesn’t better than those who don’t spend time on the floor of the plant. When an employee makes a suggestion that improves business operations, including suggestions regarding minimizing downtime, recognize this individual. Doing so leads to more productivity.
Business owners might find they struggle to minimize downtime in their manufacturing plants. However, doing so remains imperative. Not only will the business save money when downtime is kept to a minimum, but everyone is happier. They aren’t sitting idle watching work back up. Nobody wants to see this, so begin using these tips today. Doing so will ensure downtime becomes less of a concern, which everyone will appreciate.
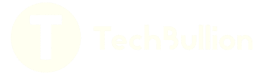