The eCommerce business model is at the pinnacle to get the buyer and the seller’s attention for a long-term perspective to enhance the sales channel. eCommerce business operations should run vividly, minimizing hurdles. The warehouse acts as the lifeline for every business model out of all the processes. Be assured good warehouse management always helps in the smooth running of the products diversely.
In 2019, a study by McKinsey & Company revealed, around $300 billion is used every year to serve the purpose of the warehousing cost and excludes the cost of correcting errors or mistakes.
It helps in handling thousands of thousands of products and manages the shipping of the products to a large audience in real-time. The process seems to be complicated to process the warehouse management. If overlooked, it may cause trouble in everyday operations. Such issues are faced regularly.
Explore in detail the challenges that warehouse operations undergo and how to overcome such challenges:
Challenge #1: Inventory Setup
Inventory issues keep growing as the number of products increases. Eventually, a shortage of space comes into play in terms of problems. The warehouse management is affected primarily because of the inventory setup or location they are built-in. And such issues affect warehouse management more broadly.
With inefficient Warehouse Management, comes slow, cost-consuming management strategies. Sometimes the picker takes a long time to load packages from the ships and has no exact idea of the location, which may result in the delay of the process and customer dissatisfaction.
Solution:
The need of the time is to come out with the best inventory set up at the right location to run the warehouse operations vividly. The best way to resolve such challenges is by looking into the warehouse management system and the barcode scanner. Such scanners are of great use as it automatically directs the pickers to the correct location to get the packages with a clear idea of the products to be shipped and scanned.
Challenge #2: Warehouse Optimization
Few warehouses run manually and have no right processes to pick the products to deliver or ship in real-time. Picking the shipped packages should be done at the right time to process the property’s delivery quickly. In case of any delay, the entire process gets disrupted to manage the inventory system.
Solution:
To perform the picking process quickly to avoid the entry of SKUs manually, instead chose to invest in the latest technology that uses barcodes or QR codes to complete the entire process. As an eCommerce businessman, you can set up a system operated directly by the providers to deliver at the correct address without much delay.
Automation of warehouse management can minimize the pressure on human beings and help lessen their effort to process warehouse management optimization.
Challenge #3: Inaccuracy of the Inventory
In some cases, the warehouse managers do not have much accessibility to the inventory in terms of visibility. The excess of the stock increases the maintenance of the warehouse cost, and insufficient stock lowers the cash flow in the sales channel to manage the market at its best. It may result in running out of stock at times of need which may harm the Business for long-term growth.
The inadequate inventory management may lead to customer dissatisfaction and orders are not placed at the right time to get the benefits of the services. As per a survey held by Wasp Barcode Technologies, about 43% of the small businesses do not track the manual or inventory method. Peoplevox adds that about 34% of the shipping gets delayed because of the invalidity of the orders in the stock.
Solution:
The one-step solution to such a warehouse management system is improving the inventory system with the latest use of the software to gather the data in real-time using the barcode or sequence number and many more. This process helps users take note of every item present in the warehouse and its movement within the warehouse along with the transportation to reach the final destination.
What’s most critical in eCommerce business management is handling the inventory counting either by using the excel sheet or with the help of any retail solution.
Challenge #4: Occupied Space
What comes to mind when we talk about warehouses is space. The lack of space may result in inappropriate functioning of the warehouse in locating the products and what quality of products are stored in the warehouse. Even work accidents are considered or taken seriously to take care of the employees.
Solution:
The best way to operate the warehouse is the adequate space to store more and more products to enhance the warehouse utility and its operations. When the vertical space is improved, it becomes easy for the pickers to pick the products quickly and minimize the process’s inventory and cost. Logistics Management in 2018 revealed that 68% of the warehouse capacity is managed by the manufacturer effectively.
Challenge #5: Process Diffusion
Warehouse employees have to generate a pick ticket or relatable documents to increase the number of people under its umbrella—the picker hands over the access to the checkers, who later gives them to the stager. The stager submits the keys to the loader, and the process continues in such a way. The entire process kills time and makes the process inadequate and ineffective for the proper utilization of the warehouse.
Solution:
Barcode technology acts as a great tool to minimize the unnecessary process automatically. The utilization of the automatic system is growing fast to manage the warehouse system at its pace to come out with productive output. Avoid backward techniques by adopting the latest Barcode technology to work the warehouse operation flexibly.
Achieve Your Business Outcomes with WMS
Shiprocket Fulfillment fulfills critical business outcomes, including counting the stock, managing the store, picking and packing the shipped packages, shipping and delivering the items in real-time, and looking into the returns matters vividly and with a lot of efficiencies with the help of barcode pasted over everything. Make use of barcodes at times of shipping of the packages.
The best part of such technology is that it helps track the products sequentially from packaging to delivery of the items at door-step in real-time. The entire process can be managed only by the warehouse experts who briefly understand the process and work on it.
The process follows every step in its best way for customer satisfaction and overcoming the warehouse challenges appropriately.
Conclusion
Warehouse challenges are simple to resolve with the help of a great Warehouse Management System. The automatic use of the system resolves all the issues or queries to operate the warehouse magnificently in a gigantic manner. With the proper warehouse management comes the best services for customer satisfaction or fulfilling customer-centric goals.
Take a hand forward to Vinculum to get the best Warehouse Management Solutions to eliminate the challenges simply and effectively.
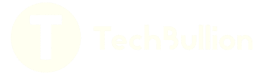