CNC (Computer Numerical Control) machining has revolutionized the manufacturing industry, enabling precise and efficient production of complex parts and components. This technology is widely used in various sectors, including automotive, aerospace, electronics, and medical devices. One of the key advantages of CNC machining is its ability to produce high-quality parts with tight tolerances, making it ideal for projects requiring precision and consistency.
China has emerged as a global hub for CNC machining due to its advanced manufacturing capabilities, skilled workforce, and competitive pricing. Many companies worldwide choose to OEM (Original Equipment Manufacturer) their CNC machining projects in China to leverage these benefits. However, navigating the landscape of Chinese manufacturing can be challenging, especially for those unfamiliar with the process.
This article aims to provide a detailed perspective on OEM CNC machining projects in China, covering essential aspects such as selecting the right supplier, understanding the production process, and ensuring.
What is CNC Machining
CNC machining is a manufacturing process in which pre-programmed computer software dictates the movement of factory tools and machinery. This process can control a range of complex machinery, from grinders and lathes to mills and routers. With CNC machining, three-dimensional cutting tasks can be accomplished in a single set of prompts.
The CNC process contrasts with—and thus supersedes—the limitations of manual control, where live operators are needed to prompt and guide the commands of machining tools via levers, buttons, and wheels. Today’s CNC systems are highly automated, resulting in greater precision, consistency, and efficiency in manufacturing.
CNC machines use a digital file as their input, a CAD (Computer-Aided Design) file created using software. The file is translated into code that the CNC machine can understand and execute. This process involves several steps, including creating the design, converting the design into a CNC-compatible format, setting up the machine, and executing the machining operations to produce the desired part.
How to OEM CNC Machining Projects in China
Outsourcing CNC machining projects to China presents several advantages, including cost-effectiveness, access to skilled labor, advanced manufacturing capabilities, and scalability. Here’s a comprehensive guide on how businesses can effectively OEM CNC machining projects in China:
Selecting the Right Supplier
Selecting the right supplier is crucial for OEM CNC machining projects in China. The supplier you choose will significantly impact your project’s quality, cost, and timeline. Therefore, conducting thorough research and due diligence is essential before deciding.
Identify potential suppliers through online directories, industry associations, and trade shows. Look for suppliers with experience in your specific industry and type of product. Check their credentials, certifications, and quality standards to ensure they meet your requirements. It’s also a good idea to request samples or case studies of previous projects they have completed to assess their capabilities.
Once you have shortlisted a few potential suppliers, visit their facilities. This will give you a firsthand look at their operations, equipment, and workforce. Ask about their production processes, quality control measures, and lead times during these visits. Discussing pricing and payment terms is important to avoid misunderstandings later.
Establishing Clear Communication
Effective communication is key to the success of any OEM project, and CNC machining projects in China are no exception. Language barriers and cultural differences can sometimes pose challenges, but these can be mitigated with clear and consistent communication.
Start by establishing a single point of contact at the supplier’s end who can understand and communicate in English if that is your primary language. Make sure to clearly define your project requirements, including technical specifications, materials, tolerances, and delivery schedules. Use detailed drawings, diagrams, and CAD files to convey your design accurately.
Regular communication is essential for monitoring the progress of your project and addressing any issues that may arise. Schedule regular update meetings or calls to discuss the project’s status, review any deviations from the plan, and make necessary adjustments. Project management tools and platforms can also streamline communication and collaboration with your supplier.
Understanding the Production Process
Understanding the production process is essential for successfully implementing OEM CNC machining projects in China. This knowledge will help you set realistic expectations, manage timelines effectively, and ensure quality control throughout the project.
The production process for CNC machining typically involves several stages, including design, prototyping, production, finishing, and quality control. Each stage requires careful planning and coordination to ensure the final product meets your specifications and standards.
Design and Prototyping
The first stage of the production process is design and prototyping. This involves creating a detailed design of the part or component you want to manufacture. The design is typically created using CAD software and includes all the necessary dimensions, tolerances, and material specifications.
Once the design is finalized, a prototype is produced to test the design and identify any potential issues. Prototyping is essential as it allows you to validate the design, make necessary adjustments, and ensure the final product will function as intended. Working closely with your supplier during this stage is important to ensure the prototype accurately represents your design.
Production and Finishing
After the design and prototype are approved, the production stage begins. This involves setting up the CNC machine, programming it with the necessary instructions, and producing the parts or components. Depending on the complexity and quantity of the parts, this stage can take anywhere from a few days to several weeks.
Once the parts are machined, they often undergo finishing processes to enhance their appearance, functionality, and durability. Common finishing processes include deburring, polishing, anodizing, and coating. The specific finishing process will depend on the material and intended use of the parts.
Quality Control
Quality control is a critical aspect of CNC machining projects. It ensures that the parts or components meet the required specifications and standards. Quality control typically involves inspecting the parts at various stages of the production process, using tools such as calipers, micrometers, and coordinate measuring machines (CMMs).
Quality control may include dimensional inspection testing for material properties, surface finish, and mechanical performance. Establishing clear quality control criteria and procedures with your supplier is important to ensure consistent and reliable results.
Conclusion
OEM CNC machining projects in China offer numerous advantages, including cost savings, access to advanced manufacturing capabilities, and a skilled workforce. However, it is essential to carefully select your supplier, establish clear communication, and understand the production process to achieve successful outcomes.
Clear communication, meticulous supplier evaluation, proactive project management, and adherence to quality standards are essential elements for achieving successful outcomes and fostering long-term partnerships with OEM suppliers in China.
Read More From Techbullion And Businesnewswire.com
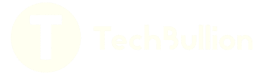