Machine maintenance is a key aspect in ensuring smooth operations and the future of your business. That said, maintenance of your molding machine is an essential step in ensuring quality plastic production in injection molding. It’s better to have a preventative maintenance process than to have to make repairs that will delay production.
Getting to Know the Molding Machine
In the manufacturing of plastic parts via injection molding, the machine uses a mold that can be worn or damaged over time. And to ensure accuracy and value, there should be effective mold maintenance.
Mold maintenance refers to the cleaning and repairs that are needed to keep an injection mold in the best working order. Here are ways you can efficiently conduct mold maintenance.
Keep a Record
To determine when you should have maintenance on your machine, you must keep a record or a resume card. That way, you can count its use, care, and damage in detail. Also, you can keep track of which parts and components have been damaged with their severity. Keeping a record of its solutions can benefit you in the long run in case you encounter such a problem again.
Stick to a Regular Maintenance Schedule
Whether it’s an old or new one, every tool should be inspected and cleaned on a regular basis so that no problems occur in the future. It’s important to know when to inspect and clean any molding tools you may have because it will save time in the long run. Plus, it prevents the trouble of cleaning up any issues with your products later on in production.
A maintenance schedule is part of your maintenance plan. And a maintenance plan should also include detailed instructions for mold cleaning, proper maintenance, and what repairs can be done.
Surface Maintenance is Key in Preventing Corrosion
Proper surface maintenance of the plastic injection mold directly affects the surface quality of the product and is key in preventing corrosion. It goes without saying that it is crucial to select the appropriate anti-rust oil for the machine.
After production, you should carefully remove the residual injection molding. Copper rods, copper wire, and mold cleaners can be used to remove the residual injection molding and other deposits. After cleaning, leave the part to dry.
Also, do not clean hard objects such as the wire and steel bar to avoid scratching the surface. If there are rust spots caused by corrosion, you can use a grinder to polish off the rust, spray the area with anti-rust oil and store the mold in a dust-free space.
Product Quality Shows the Condition of the Injection Mold
The quality of the plastic part coming out of the injection mold can indicate whether the mold is in good condition or not. If the parts come out with rust on the surface, scorch marks, or in an odd shape, then the mold may have a water leak around a seal that needs to be repaired. The good quality of parts indicates a healthy mold condition. Therefore, include parts examination on the maintenance routine.
Production Environment Influences Molding
The surrounding environment in which your injection molding machines are kept affects how long they will last. External factors like temperature, pressure, humidity, and more should be taken into consideration because they can affect the quality of your molds as well as the part production.
Also, the environment can affect the maintenance schedule. Most plastic injection molds are made from uncoated steel which can rust in high heat and moisture environments. You must take into consideration the maintenance schedule and strategy with your environment to ensure that your molds won’t be affected.
Track and Test Parts
Several important parts of plastic injection molding should be tracked and tested: ejection, guide, and sealing parts are all used to ensure that the opening and closing movement of molding and ejection of plastic components is fluid. If any part of the process is interrupted due to damage it can affect production time. Therefore, the lubrication of molds and seals as well as checking for deformities or damage on all parts regularly should be kept up in order to avoid a halt in production.
Key Takeaway
When it comes to injection molding machines and tooling, it is important to make sure all of your equipment is in good shape. Having working injection molding machines and tooling is integral to producing quality products and staying efficient.
Having a detailed maintenance plan that includes factors such as the environment, sticking to a regular schedule, keeping a record, and examining up to the last bit will significantly prolong the health of the molding machine. Remember, preventative maintenance is better than having to repair and deal with the problem that can delay production and add more costs.
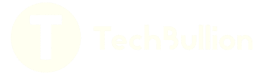