When it comes to running a business, many operations happen multiple times and run concurrently. As a result, there are many things to consider when trying to get these operational processes to flow smoothly. But with all these operations and procedures, there are bound to be errors and mistakes that arise from mismanagement, misinformation, and the like, especially when it comes to handling grease trap waste services. If these errors are not curtailed, they will lead to losses for the company in the long run.
What is Process Waste?
Process waste or lean waste is any process, step, or activity that customers are unwilling to spend on. A process that does not add value to your company to the customers or increase productivity in your company can be considered as waste. Common reasons why waste in a business needs to be mitigated are many. Some of these reasons are:
Costs
Consider the amount of money that goes to waste when a process yields no profit. If it is not beneficial to the company and is not something, customers are willing to pay for, putting funds into doing it results in waste.
Efficiency
Operational activities are how tasks get completed. But superfluous or unnecessary processes can lead to redundancy and waste on necessary materials. By cutting wasteful and unneeded processes, it grants efficiency to the operations.
Improve Quality
Removing unnecessary production practices and improving pre-existing useful processes tend to increase product quality during the manufacturing process.
The Birth of Lean Manufacturing
Since the 20th century, manufacturing processes within companies have had a lot of techniques or lean waste, and with time, greater manufacturing processes were needed. This brought about a need for lean manufacturing.
Lean manufacturing is a production methodology that focuses on reducing company process waste and, at the same time, boosts productivity. This manufacturing principle became widespread in the 1990s after a magazine featured the lean manufacturing processes used by the car manufacturer Toyota.
Lean manufacturing is based on the principle that process waste should be cut out from a company’s operations. There are seven basic process wastes, according to Toyota manufacturing company. But an extra process waste has also been identified by other parties. These are:
- Defects: Errors in productions that will take extra funds and time to rectify.
- Overproduction: Producing too much of a component of a product.
- Waiting: This could result in customers, employees, and machines being idle.
- Transportation: Unnecessary movement of goods due to communication errors.
- Inventory: Inappropriate handling of Inventory or storage space.
- Motion: Time and resources wasted by moving people and equipment to and fro.
- Over-processing: Taking extra time or processes to meet demands.
- Untapped potential: This refers to the wasted possibilities of individuals and equipment when they are not put to good use.
Many tools have been designed to promote lean manufacturing. One of such tools is the BeOneSolutions Lean Manufacturing SAP. By including the production process in sap b1, the add-on (beonesolution Lean Manufacturing SAP) can handle lean waste properly.
Conclusion
Lean manufacturing is still followed by major companies all over the world. As long as you run a company, process waste will always arise. Therefore, it is left for you always to use this methodology to reduce waste and improve your processes.
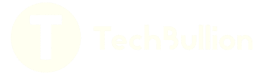