An efficient construction job site is one where tasks are completed in the least amount of time with minimal waste, while maintaining high standards of quality and safety. Efficient job sites not only reduce costs but also ensure that projects are completed on schedule, which is critical in the competitive construction industry.
A key factor in achieving such efficiency is the proper selection and use of equipment. The right equipment can streamline operations, reduce downtime, and enhance worker productivity, ultimately driving project success. In this article, we will explore how selecting the right equipment can significantly improve your construction job site’s efficiency, leading to better outcomes and more profitable projects.
Understanding Your Needs
Before selecting equipment, you should thoroughly assess the specific tasks involved in your project. Every construction site has unique demands, whether it’s earthmoving, lifting heavy materials, or precise finishing work. Understanding the nature of these tasks will help you determine the types of equipment that will be most effective.
Next, consider the scale and complexity of your project. Large-scale projects with multiple phases require more robust and versatile machinery, while smaller projects might benefit from more specialized or compact equipment. Evaluating the project’s scope ensures that the equipment you choose can handle the workload without unnecessary delays or complications.
Additionally, identify any unique challenges or environmental factors that could impact your equipment needs. For example, working in a confined urban space, on uneven terrain, or in extreme weather conditions may necessitate specialized machinery designed to operate efficiently under such circumstances. By thoroughly understanding your project’s needs, you can make better-informed decisions that will optimize job site efficiency from the start.
Choosing the Right Equipment
When you carefully choose the right equipment, you can significantly enhance the efficiency of your construction job site, leading to faster completion times, lower costs, and a safer work environment. Here is a closer look are some key categories of equipment and the factors to consider when making your choices.
Earthmoving Equipment
- Excavators: Versatile and powerful, excavators are essential for digging, trenching, and material handling. Their ability to rotate 360 degrees makes them highly efficient for a variety of tasks.
- Bulldozers: Ideal for pushing large quantities of soil, sand, or debris, bulldozers are indispensable for grading and clearing land. Their robust design allows them to operate in tough conditions.
- Graders: Graders are critical for creating smooth, flat surfaces. They are commonly used for road construction and site preparation, ensuring precise leveling and grading.
- Backhoes: Combining the capabilities of an excavator and a loader, backhoes are highly adaptable, making them suitable for a range of earthmoving tasks, including digging, lifting, and transporting materials.
Material Handling Equipment
- Cranes: Cranes are essential for lifting and moving heavy materials vertically and horizontally. Whether you’re working on a high-rise building or an industrial project, cranes provide the necessary reach and power.
- Forklifts: Forklifts are vital for moving materials around the job site, especially in warehouses and storage areas. Their maneuverability and lifting capacity make them a go-to option for material handling.
- Loaders: Loaders are used for loading and transporting materials such as soil, gravel, and debris. Their ability to handle large loads quickly makes them invaluable for site clean-up and preparation.
Specialized Equipment
- Concrete Pumps: For projects involving large amounts of concrete, pumps are crucial for delivering concrete quickly and efficiently to hard-to-reach areas, reducing labor time and improving consistency.
- Paving Machines: Essential for road construction, paving machines ensure a smooth and durable surface by evenly distributing asphalt or concrete across a roadbed.
- Drilling Equipment: From foundation drilling to creating boreholes for utilities, specialized drilling equipment is necessary for projects requiring precision and depth.
Factors to Consider
- Cost: Balancing the initial purchase or rental cost of equipment with its expected productivity and return on investment is key. Look for equipment that offers the best value for your budget while meeting your project needs.
- Maintenance Requirements: Equipment that requires frequent maintenance can lead to costly downtime. Choose machines known for their reliability and easy maintenance to keep your project on track.
- Fuel Efficiency: Fuel costs can add up quickly, especially on large projects. Opt for equipment that offers high fuel efficiency to reduce operational costs and environmental impact.
- Safety Features: Safety should always be a priority. Equipment with advanced safety features can protect workers and reduce the risk of accidents, contributing to a smoother, more efficient job site.
- Compatibility with Other Equipment: Ensure that your selected equipment can seamlessly integrate with other machinery and tools on the job site. Compatibility can enhance workflow and prevent delays due to mismatched or incompatible equipment.
Maximizing Equipment Utilization
To truly enhance job site efficiency, it’s not enough to simply choose the right equipment; you must also maximize its utilization. This involves a combination of proper maintenance, skilled operation, effective scheduling, and leveraging modern technology.
Proper Maintenance
- Regular Inspections: Routine inspections are essential to identify potential issues before they become serious problems. Regularly checking critical components such as hydraulics, engines, and tires can prevent unexpected breakdowns and costly repairs.
- Scheduled Maintenance: Adhering to a strict maintenance schedule based on manufacturer recommendations ensures that equipment remains in peak condition. Scheduled maintenance, such as oil changes, filter replacements, and system checks, extends the life of your machinery and keeps it running smoothly.
- Preventive Maintenance Programs: Implementing a preventive maintenance program helps address wear and tear before it leads to equipment failure. By proactively replacing parts and addressing minor issues, you can reduce downtime and keep your equipment operational for longer periods.
Operator Training
- Skilled Operators: Ensuring that operators are properly trained and experienced is critical to maximizing equipment efficiency. Skilled operators know how to get the most out of machinery while minimizing wear and tear.
- Safety Training: Safety training is essential not only for protecting workers but also for maintaining efficient operations. Operators who understand and follow safety protocols are less likely to be involved in accidents that could result in equipment damage or project delays.
- Efficient Operation Techniques: Training operators in efficient operation techniques, such as optimizing fuel use and reducing unnecessary idling, can significantly enhance productivity and lower operating costs.
Effective Scheduling
- Optimize Equipment Usage: Effective scheduling ensures that equipment is used to its fullest potential without overloading it. Properly timed shifts and staggered usage can prevent bottlenecks and ensure continuous progress on the job site.
- Minimize Downtime: By coordinating equipment usage and maintenance schedules, you can minimize downtime and avoid costly delays. Strategic scheduling allows for seamless transitions between tasks, keeping the project on track.
Technology Integration
- GPS Tracking: GPS tracking technology allows you to monitor the location and movement of equipment in real time. This ensures that equipment is where it needs to be and helps prevent theft or misuse.
- Telematics: Telematics systems provide valuable data on equipment performance, including fuel consumption, engine hours, and diagnostic alerts. This information helps you make informed decisions about maintenance, operation, and fleet management.
- Construction Management Software: Integrating construction management software streamlines project planning, scheduling, and resource allocation. These tools can optimize equipment usage, track progress, and ensure that all aspects of the project are running efficiently.
Safety Considerations
Prioritizing safety on the job site not only protects workers but also enhances overall efficiency. When safety is integrated into every aspect of the project—from equipment features to operator practices and job site protocols—it creates a stable environment where work can proceed without unnecessary interruptions, risks, or delays.
Equipment Safety Features
- Emergency Stop Buttons: Many modern machines come equipped with emergency stop buttons that allow operators to quickly halt operations in case of an emergency. These features are critical for preventing accidents and reducing the severity of incidents.
- Safety Guards: Safety guards protect workers from moving parts, reducing the risk of injuries. Properly installed and maintained guards are essential on machinery such as saws, grinders, and other equipment with rotating or reciprocating parts.
- Warning Systems: Equipment equipped with warning systems, such as alarms, lights, and sensors, can alert operators and nearby workers to potential dangers. These systems help prevent accidents by providing immediate feedback when something is wrong.
Operator Safety
- Personal Protective Equipment (PPE): Operators must be equipped with appropriate PPE, including hard hats, gloves, safety glasses, and steel-toed boots. PPE provides a vital layer of protection against common job site hazards.
- Safety Training: Comprehensive safety training for all operators is essential. This includes instruction on the safe use of equipment, awareness of job site hazards, and adherence to established safety protocols. Proper training helps prevent accidents and ensures that operators know how to respond to emergencies.
- Safe Operating Practices: Promoting safe operating practices is key to reducing risks. This includes guidelines on maintaining a safe distance from other equipment, avoiding distractions, and following manufacturer instructions for equipment use. Consistent adherence to these practices keeps both operators and other workers safe.
Jobsite Safety
- Clear Communication: Effective communication is vital for job site safety. Establishing clear lines of communication between workers, supervisors, and equipment operators helps prevent misunderstandings that could lead to accidents.
- Proper Signage: Adequate signage is essential for identifying hazards, providing instructions, and ensuring that everyone on the job site is aware of safety protocols. Signs should be placed in visible locations and be easy to understand.
- Hazard Identification: Regularly identifying and assessing potential hazards on the job site is crucial. This includes everything from loose materials and uneven surfaces to overhead power lines and weather-related risks. Proactively addressing hazards enables you to prevent accidents before they occur.
Better Job Site Efficiency is Within Your Reach
Improving construction job site efficiency hinges on a thorough understanding of your project needs, selecting the right equipment, maximizing equipment utilization, and prioritizing safety. And the benefits of efficient job sites are clear: reduced costs, faster project completion, and improved safety. As you move forward, consider exploring additional equipment options and staying updated on best practices. By continuously refining your approach, you can maintain a competitive edge and ensure your construction projects are both successful and profitable.
Read More From Techbullion And Businesnewswire.com
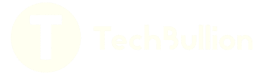