Maintaining high-quality standards is essential for any organization aiming to remain competitive and efficient. Traditional, manual quality management processes often need help to keep up with the demands of modern businesses, leading to inefficiencies and increased risk of error.
Automated quality management (AQM) offers a powerful solution by streamlining quality assurance processes, reducing human error, and ensuring consistent compliance with industry regulations. By implementing AQM, organizations can enhance operational efficiency, drive continuous improvement, and maintain high product or service quality across all operations.
What is Automated Quality Management?
Automated quality management refers to the use of technology-driven systems to monitor, analyze, and enhance quality control processes without significant manual intervention. AQM integrates with your organization’s existing workflows, offering real-time insights, automatic documentation, and consistent quality assessments.
Why Implement Automated Quality Management?
The implementation of AQM offers several advantages:
- Enhanced Accuracy: Automation reduces human error by standardizing quality checks and reports.
- Increased Efficiency: It can handle large volumes of data and tasks faster, allowing your team to focus on more strategic areas.
- Cost Reduction: Automation helps lower operational costs by reducing the need for manual oversight, minimizing product defects, and lowering rework rates.
- Consistent Compliance: With built-in monitoring systems, AQM helps organizations comply with regulations by automatically flagging and addressing discrepancies.
Step-by-Step Guide to Implementing Automated Quality Management
1. Assess Your Current Quality Management System (QMS)
Before diving into automation, evaluate your existing quality management practices. Understand what aspects of your current system need improvement—whether it’s compliance monitoring, error reporting, or document management.
Key areas to assess:
- Error tracking and root cause analysis
- Documentation and audit processes
- Compliance with regulatory standards
- Frequency and depth of manual interventions
Pinpointing the weaknesses in your manual system can guide you to what functionalities are critical when selecting an automated solution.
2. Define Objectives and KPIs
Setting clear goals for what you want to achieve with an automated quality management system is essential. This could include reducing manual oversight, improving response time to quality issues, or enhancing product consistency. Defining specific Key Performance Indicators (KPIs) will help you measure the success of your AQM implementation.
Some KPIs to consider include:
- Reduction in error rates: Track how often defects are caught and corrected.
- Time to resolution: Measure the time taken to resolve quality issues.
- Compliance adherence: Ensure that all regulatory standards are met consistently.
Setting these benchmarks ensures that your automated system performs to expectations and provides measurable value.
3. Choose the Right AQM Tools and Software
Once you’ve identified the areas that need automation and set your goals, it’s time to choose the right AQM tools. Several types of systems are available, each tailored to specific industries and needs.
Key features to look for in AQM software:
- Real-Time Monitoring: Instant feedback on quality deviations allows for immediate action.
- Automated Reporting: Efficiently generates reports and documentation to ensure compliance.
- Root Cause Analysis: Helps identify and rectify recurring quality issues.
- Scalability: As your business grows, the AQM system should be able to scale accordingly.
Consider solutions that integrate seamlessly with your existing platforms, whether that be CRM software like HubSpot, an ERP, or customer support systems.
4. Pilot Test and Train Your Team
Before a full-scale rollout, it is advisable to run a pilot test with the selected automated quality management system. This trial phase helps you identify potential challenges and allows your team to familiarize themselves with the new tools.
During the pilot, monitor key metrics like error rates, time to resolution, and user adoption. Gathering feedback from your team is crucial, as their input can highlight areas that need further refinement.
5. Full Deployment and Continuous Improvement
Once the pilot phase proves successful, it’s time for full-scale implementation. However, AQM is not a set-it-and-forget-it solution. Continuous monitoring and updating are essential to ensure your system evolves with changing regulations and organizational needs.
Moreover, AQM systems often provide insightful analytics. Use this data to refine your quality management processes over time, addressing bottlenecks and improving efficiencies. Always be open to scaling up your AQM as your business expands, ensuring that your quality standards grow along with your operations.
Integrating AQM with Customer Feedback Systems
In addition to streamlining internal processes, automated quality management can significantly improve customer-facing operations. Integrating AQM with customer feedback systems provides invaluable insights into product performance, customer satisfaction, and areas needing improvement. Automated solutions can aggregate and analyze feedback data in real-time, alerting you to quality issues customers experience before they escalate.
For instance, in a call center environment, automated tools can monitor interactions to ensure that agents follow scripts and maintain a high service level.
If certain patterns of dissatisfaction are detected, the system can automatically generate reports and suggest areas of improvement, all without the need for manual oversight. This leads to enhanced customer satisfaction and higher retention rates.
Leveraging AI for Predictive Quality Management
One of the most advanced features of modern AQM systems is the use of artificial intelligence for predictive quality management. By leveraging AI, organizations can monitor current operations and predict future quality issues before they occur.
AI algorithms analyze historical data to identify patterns that lead to defects or errors. Once detected, the system can either alert human managers or, in some cases, take preemptive action to avoid the issue altogether.
For instance, in manufacturing, AI can predict when a machine might malfunction, allowing maintenance teams to address the problem before it affects product quality.
This predictive capability is a game-changer, as it minimizes downtime, reduces costs, and ensures a consistently high level of product quality.
Summing Up
Implementing automated quality management in your organization is a strategic move that significantly improves efficiency, compliance, and overall product or service quality. You can ensure a smooth transition and long-term success by following a structured approach, assessing your current system, setting clear objectives, selecting the right tools, and continuously refining the process.
With the additional integration of customer feedback and AI-driven predictive insights, AQM improves internal operations and enhances customer satisfaction, positioning your business as a leader in quality management for years to come.
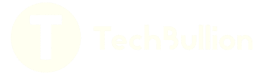