Metal testing machines are vital assets in industries that rely on accurate material testing to guarantee product quality and safety. These machines provide crucial data on material properties, including strength, durability, and hardness, which are necessary for making informed decisions about manufacturing and engineering processes. However, like any equipment, metal testing machines are subject to wear and tear over time, potentially affecting their performance and accuracy.
Extending the lifespan of metal testing machines maximizes their value, minimizes downtime, reduces maintenance costs, and guarantees consistent testing reliability. By implementing effective maintenance strategies and understanding common challenges, businesses can significantly enhance the longevity of these essential tools. The purpose of this article is to explore the importance of regular maintenance, the challenges involved in maintaining metal testing machines, and how best practices can be used to ensure their durability and reliability.
The Importance of Regular Maintenance for Metal Testing Machines
Regular maintenance is the cornerstone of extending metal testing machines’ lifespan. Without proper upkeep, even the most advanced material testing equipment can experience performance issues, leading to inaccurate results and costly repairs. Maintenance routines allow for smooth machine functioning but also prevent minor issues from escalating into significant problems.
A key aspect of maintenance is calibration, which ensures accurate machine measurements. Over time, metal testing machines may experience calibration drift due to continuous use, vibrations, or environmental factors such as temperature and humidity changes. Regular calibration aligns the machine’s settings with industry standards, such as ASTM or ISO requirements, safeguarding test results’ reliability.
Another critical component is cleaning and lubrication. Dust and debris can accumulate on mechanical parts, causing friction and wear that reduce efficiency. Regular cleaning prevents contaminants buildup, while proper lubrication minimizes friction, ensuring smoother operation and extending moving parts’ life.
Maintenance also includes routine inspections, which help identify signs of wear and tear, such as loose components or unusual vibrations. Early detection of these issues allows timely interventions, preventing breakdowns and costly replacements.
In addition to prolonging equipment lifespan, regular maintenance increases safety. Faulty machines can harm operators and compromise testing accuracy. A well-maintained machine operates more reliably, reducing accidents and resulting in consistent, accurate test results. By committing to a structured maintenance schedule, businesses can protect their investment and optimize metal testing machines’ performance.
Common Challenges in Maintaining Metal Testing Machines
Maintaining metal testing machines presents several challenges, particularly for businesses that rely on continuous and heavy usage. These challenges, if not addressed effectively, can lead to reduced equipment performance, higher repair costs, and even complete operational failure.
One of the most common issues is wear and tear caused by constant use. Metal testing machines test materials with varying properties, exposing them to stress, abrasion, and impact. Over time, this can lead to the degradation of critical components, such as grips, sensors, and moving parts, which compromises the accuracy and reliability of the equipment.
Another significant challenge is calibration drift. Prolonged use, environmental factors, and aging components can deviate machine measurements from standardized values. This drift can result in inaccurate test results, potentially leading to flawed conclusions about material properties. Regular calibration is required to counteract this issue, but it requires expertise, time, and resources.
Environmental factors also play a key role in metal testing machines’ lifespan. Exposure to dust, humidity, or temperature fluctuations can accelerate wear on sensitive components. Among other things, moisture can lead to rust and corrosion, particularly on machines with metal parts exposed to harsh environments.
Additionally, operator errors can exacerbate maintenance issues. Improper handling, insufficient training, or neglecting routine maintenance schedules can cause unnecessary strain on the machine, further reducing its lifespan. Addressing these challenges requires a combination of preventative measures, proper training, and proactive maintenance.
By understanding and mitigating these common challenges, businesses can make sure their metal testing machines remain in peak condition, delivering consistent and reliable performance over the long term.
Best Practices for Extending Metal Testing Equipment Lifecycle
Extending metal testing equipment lifespan requires a proactive approach that combines regular maintenance, proper usage, and investment in high-quality tools and resources. By following the best practices, businesses can maximize equipment efficiency, reliability, and durability.
1. Implement a Comprehensive Maintenance Schedule
A structured maintenance schedule is fundamental to keeping metal testing machines in optimal condition. This includes regular cleaning to prevent debris buildup, lubrication of moving parts to reduce friction, and routine inspections to identify wear and tear early. Maintenance schedules should also incorporate calibration checks to guarantee accurate measurements, aligning the machine with industry standards.
2. Protect Equipment from Environmental Factors
Metal testing machines used in controlled environments can significantly increase their longevity. Minimize exposure to dust, humidity, and temperature fluctuations by placing machines in clean, climate-controlled rooms. Using protective covers when equipment is not in use can also prevent contaminants from affecting sensitive components.
3. Use High-Quality Replacement Parts and Consumables
When components wear out or need replacement, always use high-quality parts compatible with the specific machine model. Inferior parts can compromise performance and increase the risk of damage to other components. Additionally, select consumables like grips, anvils, or tools for metal testing that are designed for the intended application to reduce unnecessary strain on the machine.
4. Train Operators and Staff
Proper operator training assists in the correct use of material testing equipment. Staff should understand the machine’s capabilities, limitations, and maintenance requirements to prevent mishandling. Providing ongoing education about best practices and troubleshooting can reduce operational errors that lead to equipment damage.
5. Monitor and Track Performance
Keeping detailed records of maintenance activities, performance metrics, and any issues encountered can help identify trends and predict potential problems. Tracking this data allows businesses to make informed decisions about maintenance schedules and equipment upgrades so that tools for metal testing remain reliable.
By following these best practices, businesses can extend the lifespan of their material testing equipment, reduce downtime, and improve overall testing efficiency. Proper care and maintenance protect advanced tools investment and support consistent, high-quality results in material testing operations.
Maximizing Metal Testing Machine Value
Extending the lifespan of metal testing machines is a crucial step toward achieving consistent performance, minimizing downtime, and maximizing return on investment. By addressing common challenges like wear and tear, calibration drift, and environmental factors, businesses can prevent unnecessary repairs and maintain the reliability of their metal testing tools.
Adopting best practices such as regular maintenance, operator training, and the use of high-quality replacement parts guarantees that these essential machines continue to deliver accurate and dependable results. Creating a structured maintenance schedule and monitoring equipment performance further increases their longevity, reducing costs and improving operational efficiency.
Investing in the care and upkeep of material testing equipment is not just about preserving machinery—it’s about safeguarding testing processes and product quality. With proper maintenance, businesses can confidently rely on their metal testing machines to meet the demanding requirements of today’s industries, guaranteeing success and sustainability for years to come.
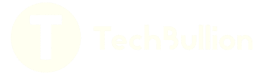