Conformal coatings are a type of electrical insulation coating applied to an object’s exterior. In this article, we’ll share what you should look for when choosing the best conformal coating for your application and how to evaluate it before you buy.
There are several things to remember when looking for the best conformal coating. First, consider the type of material you’ll be coating. Conformal coatings are available in various materials, each with its benefits and drawbacks. Some typical materials used for conformal coatings include:
* acrylics
* polyurethanes
* silicones
Each type of material has advantages and disadvantages, so choosing the one that best suits your needs is essential. For example, acrylics offer excellent durability and chemical resistance, but they can be difficult to remove if you need to make repairs. Silicones, on the other hand, are much easier to remove but don’t offer as much protection against chemicals.
Once you’ve decided on the type of material you want, look at the different brands available. Not all conformal coatings are created equal, and some brands will better suit your needs than others. When evaluating brands, pay attention to things like:
* cure time
* Thickness
* Flexibility
* chemical resistance
Finally, make sure you understand the application process before you buy
What Is The Silicone Conformal Coating?
A silicone conformal coating is a type of coating that is applied to electronic components and printed circuit boards (PCBs) for protection. The primary purpose of a conformal coating is to insulate and protect the surfaces of electronic devices from moisture, dust, chemicals, and other environmental hazards. Silicone conformal coatings are made from silicone polymers and provide superior moisture resistance and dielectric properties compared to different conformal coatings.
There are two main types of silicone conformal coatings: solvent-based and water-based. Solvent-based coatings are typically made from dimethylsiloxane (DMS) or hexamethyldisiloxane (HMDS), while water-based coatings are typically made from polydimethylsiloxane (PDMS). Silicone conformal coatings can be applied to electronic components and PCBs using various methods, including spraying, dipping, brushing, and screen printing.
Silicone conformal coatings are widely used in the electronics industry to protect electronic devices from moisture, dust, and other environmental hazards. They are commonly used in aerospace, military, and medical applications where reliability and performance are critical.
The main advantage of silicone conformal coating is that it provides superior moisture resistance and dielectric properties compared to other conformal coatings. Silicone conformal coatings are also resistant to a wide range of chemicals, making them ideal for harsh environments. Another advantage of silicone conformal coatings is that they can be applied using various methods, including spraying, dipping, brushing, and screen printing.
The Benefits Of Silicone Conformal Coating
Silicone conformal coating provides many benefits for printed circuit boards (PCBs), including:
- Protection from the environment: Silicone conformal coating protects PCBs from environmental threats, including moisture, humidity, dust, and chemicals.
- Improved reliability: Silicone conformal coating can improve the reliability of PCBs by providing a barrier against electrical shorts and corrosion.
- Enhanced thermal stability: Silicone conformal coating can help improve PCBs’ thermal stability, making them less susceptible to temperature-related issues such as solder joint defects.
- Increased lifespan: The protective nature of silicone conformal coating can help to extend the lifespan of PCBs by protecting them from damage.
For more about silicone conformal coating, you can pay a visit to DeepMaterial at https://www.epoxyadhesiveglue.com/category/epoxy-conformal-coating/ for more info.
Why Has The Demand For Silicone Conformal Coatings Increased?
Due to their superior performance in several key areas, the demand for silicone conformal coatings has increased in recent years. Silicone conformal coatings have excellent moisture resistance, making them ideal for use in environments where high humidity is a concern. They also have good dielectric properties, making them ideal for protecting electronic components from voltage spikes and other electrical hazards. In addition, silicone conformal coatings are highly resistant to chemicals and temperature extremes, making them an ideal choice for applications where these factors are concerned.
The Types Of Silicone Conformal Coatings And What They Are Used For
There are three types of silicone conformal coatings: UV-curable, acrylic, and polyurethane. Each type has its unique properties and is used for different applications.
UV-curable silicone conformal coatings are typically used in applications with high temperatures. They cure quickly and can withstand temperatures up to 250°C.
Acrylic silicone conformal coatings have excellent moisture resistance and can be used in various applications. They are commonly used in the food and beverage industry due to their ability to resist bacteria and other contaminants.
Polyurethane silicone conformal coatings are the most versatile type of coating and can be used in indoor and outdoor applications. They have excellent moisture resistance and can withstand extreme temperatures, making them ideal for use in harsh environments.
What are the benefits of using silicone conformal coatings?
How To Evaluate A Good Silicone Conformal Coating
A good silicone conformal coating should protect your PCB from various environmental factors, including moisture, dust, and chemicals. It should also be able to withstand high temperatures and provide electrical insulation. There are a few key things to look for when evaluating a silicone conformal coating:
-The thickness of the coating should be between 2 and 10 mils. Anything thicker than ten mils may be too difficult to remove during repair or rework, and anything thinner may not provide adequate protection.
-The coating should have a low viscosity so that it can easily flow into all the nooks and crannies of your PCB. A higher density might cause the coating to pool in certain areas or not adhere properly to the surface.
The cure time should be relatively short, so you can immediately put your PCB into service. A longer cure time means that the volatile components of the coating will evaporate before they can cure fully, which could result in inadequate protection.
-The coefficient of thermal expansion (CTE) should match that of your PCB material as closely as possible. If the CTE mismatch is too significant, it can cause cracking or delamination of the coating during temperature changes.
-The dielectric constant (DK) and dissipation factor (DF) should be as low as possible. A high DK or DF can cause signal interference and degrade your circuit’s performance.
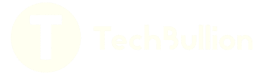