First, consider the type of materials you need to work with. Different CNC machine tools are designed for different types of materials such as soft metals, hardwoods, plastics, or composites. Knowing which material, you will be working with is essential in selecting the right tool for your job.
Second, think about what kind of accuracy and precision you require from your parts. Do you need highly accurate parts with tight tolerances? Or more basic components that don’t need to have exact dimensions? Once again this will help guide your selection process toward a specific type of CNC machine tool that can handle these requirements.
How complex CNC Parts are?
CNC machining is a very cost-effective and efficient way to produce parts, given the right set of tools and machines. The expertise and experience required to adequately program these complex machines are important factors in achieving desired outcomes with CNC technology.
Before beginning any job, it’s critical that you understand your application requirements, such as materials type and hardness, surface finish tolerances, accuracy needed for fitment or mating surfaces, etc., so the correct cutting tool selection can be made.
Hwacheon also provides a range of Special Machines which are needed for complex and specific applications like Polygon Turning, Gear Shaving, or chamfering/deburring. Hwacheon Twin Turret Lathes are ideal to reduce cycle times by bringing multiple operations under one setup and in the same machine, by using two (2) turrets with multi-tools each.
Also available is the unique Multi Low Profile Slant Bed in all ranges of turning machines from CNC Lathe to Vertical – 5 Axis Machining Centers.
This design ensures improved chip evacuation, better operator visibility at the cutting position, and optimal ergonomics while machining components with long overhangs at reduced floor space requirements.
Importance of the type of Material
CNC machines are capable of working on almost any kind of material, including aluminum, copper, mold steel or hardened steel, titanium, and Inconel. The type of material to be machined will influence the machine design and the spindle to be selected, as also the levels of performance, durability, load bearing, and precision that can be realized.
Physical properties and optimum cutting conditions of the material will also influence machine tool factors such as the maximum spindle speed, peak spindle motor horsepower, and max spindle motor torque needed.
Types of CNC Control Systems
The choice of CNC control should be a carefully considered and thought-out decision. The machine tool supplier you choose can offer advice on selecting the right CNC Control for your particular requirements.
You should consider how the latest technology might benefit from automated operations, or even remote servicing, as this could save both time and money in production costs down the line.
Furthermore, look for systems that are user-friendly with easy-to-read displays and intuitive interfaces to ensure productivity is maximized when using them. All these factors will help you make sure that you get maximum value out of your investment in cutting-edge machinery tools.
Cost of Procuring CNC parts
The time frame of the production process needs to be taken into consideration when deciding whether or not one machine is better than another. For more lengthy production processes, an expensive but highly efficient machine may prove to be a more cost-effective choice in the long run because of its higher output and lower operating costs. On the other hand, for shorter production cycles with fewer pieces requiring processing, a cheaper but less efficient machine might represent a better option.
Lastly, you need to evaluate the efficiency levels of each machine under different operating conditions. It is important to determine how much energy each consumes while running at various speeds and temperatures as well as its ability to handle materials of varying thicknesses and shapes. These factors will give you an idea about which model offers greater value for money in line with your specific requirements.
Availability of Work Space
For machines No matter how much space you have on your shop floor, proper planning is essential. You will need to make sure that the machine tool fits comfortably in its designated spot and that all safety requirements are met.
Additionally, you should keep ergonomics in mind when placing the machine tool as this can help protect workers from injury or fatigue. It is important to ensure that ample storage areas are available nearby so materials and tools can be stored close by while still allowing easy access when needed.
Tips for Choosing the Right CNC Parts
First and foremost, consider whether you need custom parts or if off-the-shelf products will work. If custom parts are required, then it’s important to have a detailed understanding of the specifications needed in order for them to be successful. This includes material type, finish requirements, and any other special features that may be necessary for optimal performance.
Additionally, examine how quickly the pieces must be produced as well as what quantities are required so that suppliers can provide accurate pricing estimates. Lastly, research different vendors carefully before committing to one in order to ensure quality control and cost-effectiveness over time.
Conclusion
Choosing the right CNC parts for your needs can be a daunting task. By understanding the basics of CNC and considering factors such as compatibility, cost, and quality you can ensure that you select the best components for your project.
Additionally, researching different suppliers to find one with experience in producing high-quality parts is essential to getting the most out of your purchase.
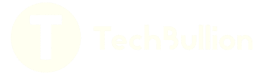