Introduction: Why the Right Labelling Machine Matters
In the competitive world of product packaging, the role of a labelling machine cannot be overstated. Accurate labelling not only ensures compliance with industry regulations but also plays a critical role in establishing brand identity and consumer trust. Imagine shelves filled with products; it’s the precise, cleanly applied labels that often capture attention and convey professionalism.
The right labelling machine can dramatically enhance operational efficiency while minimising costs associated with errors and rework. It’s not merely a tool—it’s an investment in your brand’s reputation and the seamless operation of your production line. With numerous options available, choosing the right one requires a blend of insight, planning, and foresight.
Understanding Your Labelling Requirements
Identifying the type of products you need to label
Labelling requirements vary widely depending on the product. Are you labelling cylindrical bottles, flat boxes, or irregularly shaped items? Each product shape demands a specific type of labelling technique and machine compatibility. For instance, bottles may require wraparound labelling, while cartons need front-and-back labels. Determining your product type is the first step towards narrowing down your options.
How label size, shape, and material affect machine choice
Not all labels are created equal. Labels can be glossy, matte, paper-based, or plastic. Each material interacts differently with adhesives and surfaces, making it vital to choose a machine capable of handling the specific combination. Size and shape further complicate matters. Oversized or unusually shaped labels may require custom configurations to achieve flawless application.
Considering the volume of labelling: High vs low production needs
Production volume plays a significant role in selecting the right equipment. For businesses with low production demands, a manual or semi-automatic machine may suffice. However, high-volume operations necessitate fully automatic systems capable of delivering consistent performance at speed. Failing to align machine capacity with your operational needs can lead to inefficiencies and bottlenecks.
Types of Labelling Machines: Which One Suits Your Business?
Manual, semi-automatic, and fully automatic labelling machines
Manual labelling machines are ideal for small-scale operations, offering simplicity and cost-effectiveness. Semi-automatic machines bridge the gap, providing a balance between manual effort and automation. For high-volume production, fully automatic machines are indispensable. These systems are designed for speed, consistency, and integration with existing production lines.
Rotary vs inline labelling machines: What’s the difference?
Rotary labelling machines excel in handling high-speed operations with precision, especially for round or uniquely shaped containers. Inline machines, on the other hand, are more versatile and suitable for medium-speed production lines. Your choice depends on the nature of your products and the scale of your operation.
Choosing between label applicators and label printers
Label applicators are perfect if you already have pre-printed labels, while label printers allow you to print and apply labels in one seamless process. Businesses requiring customisation or on-demand printing may find printers more beneficial, while applicators are ideal for standardised labelling needs.
Key Features to Look for in a Labelling Machine
Label accuracy and precision
Poorly aligned labels can tarnish your brand’s image. A good labelling machine ensures consistent placement with minimal deviation, maintaining a polished and professional appearance for every product.
Speed and efficiency: Matching machine capacity to production line
Speed matters. Your machine should align with your production line’s pace to prevent delays. Assess the number of labels a machine can apply per minute and choose one that complements your throughput requirements.
Ease of use and user-friendly interfaces
A machine with an intuitive interface simplifies operation and reduces training time for staff. Look for features such as touchscreen controls, adjustable settings, and easy changeovers for different label types.
Customisation options for different packaging sizes
Flexibility is key. A machine capable of handling various packaging sizes and shapes ensures adaptability as your product line evolves. Customisation options, such as adjustable guides or multiple application heads, add significant value.
The Importance of Machine Durability and Reliability
Investing in quality: Why durability matters for long-term use
Labelling machines are long-term investments. Opting for a high-quality, durable model ensures consistent performance and reduces the frequency of repairs or replacements.
How to evaluate machine reliability and uptime potential
Downtime can cripple production schedules. Reliable machines with robust construction and tested components minimise interruptions. Look for reviews and reliability metrics from manufacturers to gauge performance.
Labelling Machine Maintenance: Keeping It Running Smoothly
Regular maintenance tips to avoid downtime
Routine maintenance, such as cleaning sensors and replacing worn parts, prolongs a machine’s lifespan. Establish a maintenance schedule to keep your machine running efficiently.
How to assess the service and support offered by manufacturers
Strong after-sales support is invaluable. Ensure your supplier provides accessible customer service, quick replacement parts, and comprehensive training to address any operational issues.
Common issues and how to prevent them
Misaligned labels, adhesive build-up, and sensor malfunctions are common problems. Regular inspections and prompt troubleshooting can prevent these issues from escalating into major disruptions.
Labelling Machine Technology: Should You Go Digital?
Benefits of digital labelling machines in modern industries
Digital labelling machines offer unparalleled precision and customisation. They streamline operations with automated adjustments, ensuring consistent label application regardless of batch variations.
Integration with your existing production line and software systems
Modern machines can integrate seamlessly with software systems, allowing for real-time monitoring, data collection, and improved workflow management. This integration enhances operational efficiency and reduces manual intervention.
Exploring advanced features like barcode printing and QR codes
Barcode and QR code capabilities are becoming standard in many industries. A machine that supports these features can improve product tracking, inventory management, and consumer engagement.
Cost vs. Value: What to Expect When Buying a Labelling Machine
How to balance initial cost with long-term savings
While upfront costs can be daunting, investing in a quality machine pays off in the long run. Consider energy efficiency, maintenance costs, and operational efficiency when assessing value.
Understanding return on investment (ROI) for labelling machines
Calculate your ROI by factoring in increased production speed, reduced waste, and improved label accuracy. A well-chosen machine can recoup its cost through these efficiencies.
Budget-friendly options without compromising quality
For businesses on a budget, refurbished or entry-level machines can be an excellent starting point. Ensure these options still meet your operational requirements and come with a warranty.
Choosing a Labelling Machine Supplier: What to Consider
How to evaluate reputation and experience of suppliers
A reputable supplier offers not only high-quality machines but also expertise in recommending the right model for your needs. Research customer reviews and case studies to gauge credibility.
Warranty, training, and customer service support from suppliers
Comprehensive warranties and thorough training are non-negotiable. A supplier committed to customer success provides ongoing support, ensuring smooth operations even post-purchase.
How to navigate the decision-making process with expert advice
Consulting industry experts or trusted advisers can simplify the decision-making process. Their insights help you weigh options objectively and avoid costly mistakes.
Ensuring Compliance with Labelling Regulations
Understanding industry standards and legal requirements for labelling
From nutritional information to safety warnings, labelling regulations are stringent. A machine that ensures compliance protects your business from penalties and enhances consumer trust.
How to ensure your labelling machine complies with packaging regulations
Choose machines capable of adapting to evolving regulations. Features like adjustable print settings and programmable software make compliance straightforward.
Staying updated on label requirements and technology updates
Industry standards can change frequently. Staying informed about technological advancements and regulatory shifts ensures your labelling process remains up-to-date and competitive.
Future-Proofing Your Labelling Machine Investment
Trends in labelling technology: What to expect in the next 5 years
Automation, AI integration, and eco-friendly labelling options are shaping the future. Investing in machines that embrace these trends ensures longevity and relevance.
How to choose a machine that adapts to future business needs
Scalability is crucial. Select a machine that can accommodate higher volumes, new product lines, or advanced labelling techniques as your business grows.
Considering scalability for growing businesses
Expandable systems and modular designs allow businesses to add capabilities without replacing the entire machine, offering cost-effective adaptability.
Conclusion: Making the Right Choice for Your Labelling Needs
Choosing the best labelling machine is more than a technical decision—it’s a strategic investment. By evaluating your specific requirements, understanding the available technologies, and considering long-term goals, you can select a machine that not only meets your current needs but also grows with your business. A well-chosen labelling machine ensures efficiency, compliance, and a polished brand image, transforming your packaging process into a cornerstone of success.
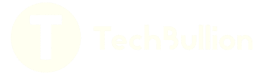