Cost estimators use their knowledge of engineering, construction, and manufacturing to calculate the cost of producing goods or completing projects. They work in a variety of industries, including electricity supply, construction, and automotive manufacturing. If you are interested in becoming a cost estimator, there are several steps you can take.
First, it is important to obtain the right qualifications. A college degree in engineering, economics, mathematics, or construction management is highly recommended for aspiring cost estimators. You should also pursue any professional certifications that may be applicable to your chosen field, such as a Certified Cost Estimator/Analyst (CCEA) credential from the Society of Cost Estimating and Analysis.
You should also gain practical experience in the field. Estimators often start out as trainees and are gradually given more responsibility as their knowledge and understanding of the industry increases. Many employers will provide on-the-job training, so look for positions that include this type of learning opportunity.
The next step is to build a portfolio of your cost estimations and other relevant work samples. This will help to demonstrate your skills and abilities to potential employers, as well as provide a record of the projects you have worked on.
Finally, stay current with industry trends and news related to cost estimating. Join professional organizations such as the American Society of Professional Estimators or the Society of Cost Estimating and Analysis to access resources, training, and networking opportunities. Keeping up with the latest developments in the industry will help you stay ahead of your competition.
By following these steps, you can start on the path toward becoming a successful cost estimator. With dedication and hard work, you can build a career that will help you make a real difference in the manufacturing and construction industries.
What does a cost estimator do?
Cost estimators analyze data to determine the cost of production for goods and services. They examine financial records, including past performance, sales, and economic trends. In addition to gathering data from existing records, they also review material requirements, labor costs, overhead expenses, and other items that could influence the cost of a product or service.
Cost estimators then use the data they collect to create cost estimates and reports, which are typically used in budgeting decisions. They may also be called upon to analyze bids from vendors to ensure that all costs have been accounted for. Finally, cost estimators monitor the progress of projects and report any changes in costs or unforeseen expenses.
What are the skills a cost estimator needs?
Cost estimators need a variety of skills in order to be successful. Strong analytical and problem-solving abilities are essential to creating accurate estimates. Cost estimators also need strong math and financial skills, including an understanding of basic accounting principles. They must also be highly organized with excellent attention to detail, as mistakes can significantly impact projects.
In addition, cost estimators need to have excellent communication skills, in order to stay up-to-date on the latest information and keep clients informed of changes. Finally, they must be able to work under tight deadlines and handle stress. With these skills, a successful cost estimator can help prevent projects from going over budget or taking longer than expected.
What are some challenges I may face as a cost estimator?
As a cost estimator, you may face the challenge of making accurate estimates in the face of rapidly changing market conditions. This can be particularly challenging if you are working with limited information or if there is not enough data available to make an informed estimate. Additionally, you may also face challenges associated with obtaining reliable cost inputs from vendors and suppliers.
Inaccurate or incomplete data can lead to inaccurate estimates and this may affect your ability to provide accurate cost estimations. Additionally, you may also face the challenge of dealing with difficult clients who are not willing to accept your estimates. Ultimately, it will be up to you to develop effective strategies for overcoming these challenges in order to produce accurate and reliable cost estimates.
It is important to remember that cost estimating requires a great deal of skill, experience, and knowledge in order to develop accurate estimates. As such, it is essential to continuously update your skills and knowledge in order to remain competitive in the industry.
What are some common mistakes made by cost estimators?
- Not adequately researching the project scope: Cost estimators must go beyond simply reviewing job specs and descriptions; they need to take time to research the construction process, materials needed, labor costs, and other factors that may impact the budget.
- Not accounting for unexpected costs: unexpected costs can arise such as permits fees or taxes and cost estimators must account for these in their projections.
- Not accounting for inflation: Cost estimators should also factor in the potential costs of inflation over the lifespan of the project as this can cause significant budget and timeline changes.
- Overly optimistic estimates: Cost estimators must be realistic when making their estimates, as overestimating can lead to project delays and overspending.
- Not properly vetting subcontractors: It’s important for cost estimators to thoroughly vet potential subcontractors and make sure they have the necessary qualifications, experience, and insurance coverage needed to complete the job.
- Lack of communication with owners: Cost estimators should make sure to communicate clearly with the project owners and keep them up-to-date on any changes to the budget. This type of transparency helps ensure that there are no surprises later on in the process.
- Not accounting for contingencies: Contingency planning is essential for cost estimators, as it allows them to plan for unforeseen circumstances and ensure that the project is completed on time and on budget.
- Not understanding the value of quality: Cost estimators must be aware of the importance of quality, as using cheap materials or cutting corners can lead to costly repairs and delays down the line. Quality should always be considered when making estimates.
- Not double-checking calculations: It’s important for cost estimators to double-check their calculations to ensure that all costs are accounted for. This helps to minimize errors and keep projects on track.
- Not taking into account change orders: Change orders are a common occurrence in construction projects and cost estimators must make sure they take these into consideration when making their estimates.
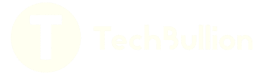