CNC (Computer Numerical Control) machining has revolutionized the manufacturing world, enabling the production of highly precise and complex parts for a wide range of industries. While the core focus of CNC machining is to achieve accuracy in the shape and dimensions of the parts, surface finishing plays an equally vital role in improving the overall quality, functionality, and appearance of the machined parts. The combination of precise CNC machining and advanced surface finishing processes results in parts that not only meet design specifications but also offer superior performance, durability, and aesthetic appeal. In this article, we will explore how surface finishing enhances CNC machined parts and why it is an essential part of the manufacturing process, with a focus on custom CNC parts and the role of BOYI CNC machining in achieving high-quality surface finishes.
The Importance of Surface Finishing in CNC Machining
Surface finishing refers to the process of modifying the surface of a material to achieve a specific finish, texture, or smoothness. It is a crucial step in CNC machining because the raw material used in the manufacturing process often has rough, uneven surfaces after the machining operations. Surface finishing techniques are employed to address these imperfections and enhance the final product. The benefits of surface finishing include:
- Improved Aesthetic Appearance: Surface finishing helps in achieving a visually appealing product. Whether it’s a shiny, polished finish or a matte surface, the finishing process can dramatically change the look of a part. In industries such as automotive, aerospace, and electronics, where custom CNC parts are often visible and interact with other components, surface finishing can significantly improve the product’s overall design.
- Increased Durability and Wear Resistance: CNC machined parts, particularly those that will be subjected to harsh environments or heavy usage, require additional protection. Surface finishing processes like anodizing, hard coating, or plating can enhance the material’s resistance to corrosion, abrasion, and wear. These protective coatings increase the lifespan of the parts, making them more suitable for demanding applications.
- Reduced Friction: Parts that have smoother surfaces experience less friction when interacting with other components, which can help to prevent wear and improve the overall efficiency of mechanical systems. Certain surface finishing processes, such as polishing, can reduce the surface roughness of custom CNC parts, leading to reduced friction and increased performance in applications like gears, bearings, and shafts.
- Enhanced Functionality: In some cases, surface finishing can be tailored to achieve specific functional properties. For example, surface textures may be applied to improve grip or to make parts more suitable for bonding or painting. Similarly, finishes such as shot peening can be used to increase the fatigue strength of parts, which is essential for components that undergo repeated stress cycles.
- Improved Cleanliness: Parts that are machined with a fine surface finish are easier to clean and maintain, especially in industries like food processing, pharmaceuticals, or medical devices, where hygiene and cleanliness are paramount. Smooth surfaces reduce the accumulation of dirt, debris, or bacteria, contributing to more hygienic products.
Common Surface Finishing Techniques in CNC Machining
There are various surface finishing methods that can be applied to CNC machined parts, each with its unique benefits. Some of the most common techniques include:
- Polishing: This process involves using abrasive materials to achieve a smooth and shiny surface. Polishing is commonly used for aesthetic purposes, particularly in industries such as jewelry, automotive, and medical devices. Custom CNC parts that require a mirror-like finish are often polished to remove any surface imperfections and enhance their visual appeal.
- Anodizing: Anodizing is a process used primarily on aluminum parts to create a protective oxide layer on the surface. This layer not only enhances the appearance of the part by providing a durable finish but also improves corrosion resistance. Anodizing is often used in industries such as aerospace, automotive, and electronics.
- Shot Peening: Shot peening is a process that involves bombarding the surface of a part with small spherical media (shots) to induce compressive stresses. This process is particularly beneficial for enhancing the fatigue strength and durability of parts subjected to cyclic loads, such as turbine blades and automotive components.
- Electroplating: Electroplating involves the deposition of a thin layer of metal onto the surface of a part using an electric current. This technique is commonly used to improve corrosion resistance, wear resistance, and aesthetic appeal. Materials such as gold, chrome, nickel, and copper are frequently used in electroplating.
- Laser Marking: Laser marking uses a focused laser beam to create permanent markings on the surface of CNC machined parts. This process is widely used for labeling, engraving, and creating identification marks on custom CNC parts in industries like aerospace, medical devices, and electronics.
- Bead Blasting: Bead blasting involves the use of abrasive beads (often glass or ceramic) to create a textured surface. This process is used to improve the surface finish by providing a matte or satin texture. It also helps in removing surface contaminants and preparing parts for subsequent coatings.
- Passivation: Passivation is the process of treating stainless steel parts to remove free iron and other contaminants from the surface. This results in a cleaner, more corrosion-resistant surface, which is particularly important in industries such as food processing, pharmaceuticals, and medical devices.
How BOYI CNC Machining Ensures Quality Surface Finishing
BOYI CNC machining is a company that has established itself as a leader in providing high-quality custom CNC parts and services. With a commitment to precision, efficiency, and innovation, BOYI CNC machining offers a wide range of surface finishing options to meet the diverse needs of its clients.
One of the key advantages of working with BOYI CNC machining is their ability to tailor surface finishes to the specific requirements of each project. Whether it’s achieving a smooth, polished surface for aesthetic purposes or applying a protective coating for enhanced durability, BOYI CNC machining has the expertise and equipment to deliver consistent and reliable results.
The company utilizes advanced technologies and state-of-the-art machinery to achieve exceptional surface finishes on custom CNC parts. With a focus on quality control, BOYI ensures that every part meets the desired specifications, from dimensional accuracy to surface smoothness. By employing industry-leading surface finishing techniques, BOYI CNC machining is able to provide parts that not only meet the functional demands of the application but also enhance the visual appeal and longevity of the product.
Conclusion
In CNC machining, surface finishing is a critical process that can significantly enhance the quality, performance, and aesthetics of the final product. By using various surface finishing techniques, manufacturers can improve the appearance, durability, and functionality of CNC machined parts, making them more suitable for a wide range of applications. Custom CNC parts, particularly those used in industries such as aerospace, automotive, and electronics, can benefit greatly from surface finishing processes like polishing, anodizing, shot peening, and electroplating.
BOYI CNC machining, with its expertise and advanced equipment, plays a crucial role in providing high-quality surface finishes for custom CNC parts. Their commitment to precision and quality ensures that each part not only meets the technical requirements but also offers improved performance and durability. By investing in surface finishing, manufacturers can optimize the functionality and appearance of their CNC machined parts, ultimately leading to more reliable and long-lasting products.
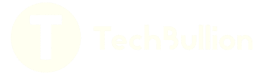