In CNC machining, precision is essential for making high-quality parts that meet specified criteria. Beyond measurements and tolerances, surface finish plays an important role in determining the overall performance, durability, and look of CNC machined components. The finish on a machined surface is more than just an aesthetic consideration; it influences how parts interact with one another, how they withstand stress and wear, and how they function in their intended applications. Understanding how different surface finishes—especially those tailored for industrial surface finish standards—affect these factors is critical for engineers and manufacturers looking to improve their products.
1. The Importance of Surface Finish in CNC Machining
Surface finish describes the texture and smoothness of a machined part’s surface. It is determined by variances in surface height and is commonly stated in terms of roughness average (Ra), with lower Ra values signifying smoother surfaces. To attain the desired smoothness, a variety of finishing procedures are used, including grinding, polishing, bead blasting, and chemical treatments. The surface finish used on a part can affect both its functionality and attractiveness.
When selecting the proper CNC surface finish, producers must examine the part’s intended application. A smooth finish may be critical for components used in high-stress settings or where strict tolerances are necessary. A rougher surface, on the other hand, may be useful for sections that require friction or where aesthetic considerations are secondary.
2. Surface Finish and Performance
Surface treatment has a considerable impact on the performance of CNC machined items. Different finishes influence how parts interact with their surroundings, including their capacity to resist wear, friction, and corrosion.
- Friction Reduction: One of the most essential characteristics of a smooth CNC surface finish is its ability to reduce friction. A lower friction coefficient in moving parts, such as gears, bearings, and sliding components, can increase efficiency, reduce energy consumption, and lengthen component life. In contrast, a rough surface texture can increase friction, resulting in rapid wear and eventual failure in high-performance applications.
- Wear Resistance: Surface roughness might affect wear resistance. A smoother surface finish helps to reduce contact stress and the possibility of abrasive wear. A fine surface finish is critical for lifespan in applications where parts are subjected to repeated contact or sliding motion, such as those used in the automobile and aerospace industries. A rough finish may trap debris and create points of weakness where wear can propagate, reducing the durability of the part.
- Corrosion Resistance: Surface finish has a significant impact on the corrosion resistance of machined items. A rough surface may have small crevices and imperfections that trap moisture and chemicals, resulting in localized corrosion. In contrast, a polished or chemically treated finish can act as a barrier, preventing corrosive chemicals from accumulating. This is especially crucial in locations where parts are subjected to severe chemicals, dampness, or high temperatures.
- Heat Resistance: A part’s surface quality can affect its capacity to dissipate heat. In applications where heat buildup is an issue, such as electronic components or high-speed machinery, a smooth surface finish can improve heat dissipation, preventing overheating and failure. In contrast, rough surfaces can behave as insulators, trapping heat and causing localized hot spots that may compromise performance.
3. Surface Finish and Durability
Durability is a critical consideration in any machined part, as it determines the part’s lifespan and ability to function under stress. The choice of surface finish can have a direct impact on the durability of a part, influencing factors such as fatigue resistance, hardness, and structural integrity.
Fatigue Resistance: Surface imperfections can serve as stress concentrators, where cracks may initiate under cyclic loading. A smoother CNC surface finish can help distribute stress more evenly across the part, reducing the likelihood of crack formation and improving fatigue resistance. This is particularly important in parts subjected to repeated loading and unloading, such as in structural components or rotating machinery.
Hardness: In some cases, surface finish treatments can enhance the hardness of a part. Processes like surface hardening, chemical treatments, or anodizing can create a harder outer layer, improving wear resistance and extending the life of the component. These treatments can also provide additional protection against scratches and dents, which can compromise the integrity of the part.
Structural Integrity: Surface finish can influence the overall structural integrity of a part, especially in applications where high strength is required. A rough surface finish may contain microcracks or voids that can propagate under stress, leading to premature failure. By contrast, a smooth, well-finished surface can enhance the part’s ability to withstand mechanical loads without compromising its strength.
4. Surface Finish and Aesthetic Considerations
While performance and durability are critical, the appearance of a CNC machined part is also an important factor in many industries. Surface finish can dramatically affect the visual appeal of a part, influencing its marketability and customer satisfaction.
Visual Appeal: In consumer products, such as electronics, automotive parts, and household appliances, the surface finish can determine the overall aesthetic quality of the product. A brushed or polished finish can convey a sense of quality and refinement, while a poorly finished surface may give the impression of low craftsmanship. The choice of surface finish can also be used to differentiate products and create a unique visual identity.
Brand Perception: The surface finish of a product can influence how customers perceive the brand. High-quality finishes suggest attention to detail and premium craftsmanship, which can enhance a company’s reputation and appeal to discerning customers. Conversely, a rough or inconsistent finish may reflect poorly on the brand, even if the part’s performance is not compromised.
Customization: Surface finish also offers opportunities for customization and branding. Techniques such as engraving, anodizing, or laser etching can be used to add logos, serial numbers, or other identifying marks to a part, creating a personalized touch that sets the product apart from competitors.
5. CNC Surface Finish Considerations
When choosing the appropriate surface finish for a CNC-machined object, various criteria should be considered:
Material: Different materials react differently to surface finishing techniques. Metals may require polishing or anodizing, whilst plastics may benefit from bead blasting or chemical treatments. Understanding material qualities is critical for getting the desired finish.
Application: The surface finish that is acceptable for the part depends on its intended use. A fine finish may be required in high-performance applications, such as aerospace or automotive components, to ensure optimal performance. In contrast, industrial pieces and prototypes may not necessitate the same level of polish.
Cost: Obtaining a high-quality CNC surface finish may increase production costs due to additional processing processes, such as polishing or coating. Manufacturers must combine the necessity for a great finish with financial limits, ensuring that the advantages of the chosen finish justify the added expense.
Conclusion
Surface finish plays an important role in the performance, durability, and look of CNC machined products. Finish selection has an impact on everything from friction and wear resistance to aesthetic appeal and brand impression. By carefully evaluating the application, material, and cost, manufacturers may choose the best CNC surface finish to maximize their products and assure long-term success.
Read More From Techbullion And Businesnewswire.com
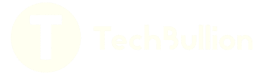