Robotic Process Automation (RPA) has been transforming the manufacturing industry over the past few years. RPA involves the use of software robots or bots that can automate repetitive and rule-based tasks that were once performed by humans. These bots can mimic human actions, such as typing, clicking, and navigating through software applications, to execute tasks with speed and accuracy.
RPA has become increasingly popular in the manufacturing industry due to its potential to improve efficiency, productivity, and quality control. Unlike traditional manufacturing processes, which rely heavily on manual labor, robotic process automation manufacturing can automate repetitive tasks, freeing up workers to focus on more complex and value-added activities.
Additionally, RPA can reduce costs by streamlining processes and reducing the need for human labor. This can be especially beneficial for manufacturers operating in high-cost regions, where labor expenses can be a significant portion of the overall cost of production.
RPA is changing the face of manufacturing by enabling manufacturers to automate repetitive tasks, reduce errors, increase production rates, and reduce costs. As a result, RPA has become an essential tool for manufacturers looking to remain competitive in a rapidly changing industry.
The benefits of RPA in manufacturing
Robotic Process Automation (RPA) is a game-changer for the manufacturing industry. Here are some of the benefits of RPA in manufacturing:
- Increased Efficiency and Productivity: RPA enables manufacturers to automate repetitive and rule-based tasks that were previously performed manually. By automating these tasks, RPA can increase efficiency and productivity by reducing the time required to complete them. This, in turn, can lead to increased output and revenue.
- Improved Quality Control: RPA can also improve the quality of manufacturing processes by reducing the risk of errors and inconsistencies. Bots can be programmed to perform tasks with a high degree of accuracy, leading to consistent and high-quality output.
- Cost Savings: By automating repetitive tasks, RPA can reduce the need for human labor, leading to cost savings. This can be especially beneficial for manufacturers operating in high-cost regions, where labor expenses can be a significant portion of the overall cost of production.
- Increased Flexibility: RPA can be programmed to handle different types of tasks, allowing manufacturers to adapt to changing production needs. This can be especially useful in industries with fluctuating demand.
- Improved Worker Safety: RPA can perform tasks that are dangerous or difficult for humans, leading to improved worker safety. For example, RPA can be used to handle hazardous materials or perform repetitive tasks that can cause strain injuries.
- Enhanced Data Analytics: RPA can collect and analyze data from different sources, leading to improved decision-making and operational efficiency.
The benefits of RPA in manufacturing are numerous and can lead to improved efficiency, productivity, quality, cost savings, and worker safety. With these benefits, it is no wonder that RPA has become an essential tool for manufacturers looking to remain competitive in a rapidly changing industry.
The potential for RPA to transform the manufacturing industry, including the possibility of completely automated factories
Robotic Process Automation (RPA) has the potential to transform the manufacturing industry in significant ways. One possibility is the development of completely automated factories, where robots perform all aspects of production, from assembly to packaging and shipping.
The concept of fully automated factories is not new, but recent advancements in RPA have made this possibility more achievable. RPA technology can now enable the development of “smart factories” that incorporate advanced technologies, such as the Internet of Things (IoT) and Artificial Intelligence (AI), to control and optimize production processes.
A fully automated factory has several potential advantages. For one, it can significantly increase production rates while reducing costs. By automating all aspects of production, there is no need for human labor, reducing the risk of human error and increasing consistency in output. This can lead to higher quality products and faster production rates.
Another advantage of a fully automated factory is improved safety. Automation can reduce the risk of worker injury by removing the need for workers to perform dangerous or repetitive tasks. Robots can perform these tasks instead, improving overall worker safety.
There are, however, potential drawbacks to a fully automated factory. One concern is the potential for job displacement as human workers are replaced by robots. However, proponents of automation argue that it will create new job opportunities, particularly in fields related to RPA and other advanced technologies.
Another potential drawback is the upfront cost of implementing a fully automated factory. The cost of RPA technology can be high, and there may be additional costs associated with retrofitting existing factories to incorporate automation technology.
Therefore, the development of fully automated factories may still be in its early stages, the potential benefits of RPA in manufacturing are clear. By increasing production rates, improving quality, and enhancing worker safety, RPA has the potential to transform the manufacturing industry in significant ways.
How RPA is enabling manufacturers to reduce costs and increase profitability
Robotic Process Automation (RPA) is enabling manufacturers to reduce costs and increase profitability in several ways. Here are some examples:
- Automating repetitive tasks: RPA can automate repetitive and time-consuming tasks, such as data entry and inventory management, which can reduce labor costs and increase efficiency. By automating these tasks, manufacturers can reallocate human resources to more value-added activities.
- Improved accuracy and consistency: RPA can perform tasks with a high degree of accuracy and consistency, reducing the risk of errors and rework. This can lead to improved product quality and customer satisfaction while reducing costs associated with defects and returns.
- Better supply chain management: RPA can help manufacturers optimize their supply chain by automating tasks such as order processing and supplier management. This can lead to more efficient procurement, reduced inventory costs, and better supplier relationships.
- Predictive maintenance: RPA can help manufacturers implement predictive maintenance programs, which can reduce maintenance costs and minimize downtime. By monitoring equipment and identifying potential issues before they become major problems, manufacturers can optimize maintenance schedules and reduce repair costs.
- Improved data analytics: RPA can collect and analyze large amounts of data, providing manufacturers with insights that can inform business decisions. By leveraging this data, manufacturers can identify inefficiencies, reduce waste, and optimize production processes, leading to cost savings and increased profitability.
How RPA is changing the face of manufacturing
Robotic Process Automation (RPA) is changing the face of manufacturing in numerous ways. Here are some examples:
- Increased productivity: RPA can automate repetitive and time-consuming tasks, such as data entry, inventory management, and quality control inspections. By automating these tasks, manufacturers can increase productivity and throughput, reducing the time it takes to bring products to market.
- Improved quality control: RPA can perform tasks with a high degree of accuracy and consistency, reducing the risk of errors and defects. By improving quality control processes, manufacturers can reduce waste, rework, and customer complaints, improving overall product quality and brand reputation.
- Enhanced safety: RPA can perform tasks that are dangerous or repetitive for human workers, improving overall worker safety. By reducing the risk of worker injury, manufacturers can improve workplace conditions and reduce the risk of litigation.
- Better supply chain management: RPA can help manufacturers optimize their supply chain by automating tasks such as order processing and supplier management. By automating these tasks, manufacturers can reduce lead times, improve supplier relationships, and reduce inventory costs.
How RPA differs from traditional manufacturing processes
Robotic Process Automation (RPA) differs from traditional manufacturing processes in several ways. Here are some key differences:
- Manual vs. automated processes: Traditional manufacturing processes rely on human workers to perform tasks such as assembly, quality control, and inventory management. In contrast, RPA automates these processes using software robots, reducing the need for manual labor.
- Accuracy and consistency: RPA can perform tasks with a high degree of accuracy and consistency, reducing the risk of errors and defects. Traditional manufacturing processes are more prone to errors, especially in tasks that require a high level of precision.
- Scalability: RPA can be easily scaled up or down depending on demand, making it ideal for manufacturers that need to adapt quickly to changing market conditions. Traditional manufacturing processes can be more difficult to scale, requiring significant investment in equipment and infrastructure.
- Flexibility: RPA can be easily reprogrammed to perform different tasks, making it ideal for manufacturers that need to adapt quickly to changing market demands. Traditional manufacturing processes are more rigid and may require significant retooling to adapt to new products or processes.
- Cost savings: RPA can reduce labor costs by automating repetitive tasks and improving operational efficiency. Traditional manufacturing processes are more labor-intensive and may require significant investment in training and development.
RPA differs from traditional manufacturing processes by automating tasks, improving accuracy and consistency, increasing scalability and flexibility, and reducing labor costs. By adopting RPA technology, manufacturers can improve operational efficiency, reduce costs, and remain competitive in a rapidly changing industry.
Conclusion:
As manufacturers face increasing competition and pressure to deliver products quickly and efficiently, adopting RPA technology can provide a significant advantage. Therefore, it is imperative that manufacturers explore RPA technology and understand how it can benefit their specific operations. By partnering with experienced RPA providers and implementing a strategic plan for RPA adoption, manufacturers can remain competitive and achieve long-term success. As a manufacturer, if you haven’t yet explored the possibilities of RPA, now is the time.
Reach out to RPA providers and learn more about how RPA can improve your manufacturing processes. Start by identifying the most time-consuming and repetitive tasks and consider how RPA can help automate those tasks. With the right approach and strategic plan, RPA can revolutionize your manufacturing operations and position your company for long-term success in a rapidly changing industry.
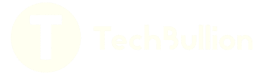