Mold temperature controllers play a critical role in the manufacturing industry, particularly in injection molding and other thermoplastic processes. The precise control of mold temperature is essential for maintaining product quality, reducing defects, and optimizing the manufacturing process. This article delves into the importance of mould temperature controllers, how they work, and their impact on product quality and defect reduction.
The function of the mold temperature machine
The manufacturing industry relies heavily on injection molding to produce a wide range of plastic products. From automotive components to consumer electronics, the quality and precision of these products are paramount. mould temperature controller are devices used to regulate the temperature of the moulds in which these products are formed. By ensuring that the mould temperature is maintained within a specific range, these controllers help achieve consistent product quality and minimize defects.
The Role of Temperature in Injection Molding
Temperature plays a crucial role in the injection molding process. The temperature of the mould affects several aspects of the final product, including:
Material Flow: The viscosity of the molten plastic is temperature-dependent. Proper mould temperature ensures optimal flow characteristics, reducing the likelihood of incomplete filling or defects.
Cycle Time: Consistent mould temperature can reduce cycle times by promoting faster cooling and solidification of the molded part.
Mechanical Properties: The mechanical strength and durability of the finished product are influenced by the cooling rate, which is controlled by the mould temperature.
Surface Finish: A uniform mould temperature helps achieve a better surface finish and reduces the appearance of surface defects.
How Mould Temperature Controllers Work
Mold temperature controller typically consist of a heating unit, a cooling unit, and a control system. The control system monitors the mould temperature using sensors and adjusts the heating and cooling units to maintain the desired temperature. The process can be described in the following steps:
Temperature Measurement: Sensors placed in the mould measure the current temperature.
Feedback Loop: The measured temperature is fed back to the control system.
Control Algorithm: The control system compares the measured temperature with the setpoint temperature and determines the required heating or cooling.
Temperature Adjustment: The control system activates the heating or cooling units to adjust the mould temperature accordingly.
Enhancing Product Quality with Mould Temperature Controllers
Consistent Material Flow and Filling: Proper temperature control ensures that the molten plastic flows uniformly into the mould cavities. This reduces the likelihood of incomplete fills, voids, and sink marks, leading to higher quality parts.
Reduced Residual Stresses: Consistent mould temperature helps in even cooling of the molded part, which reduces residual stresses. Lower residual stresses result in better dimensional stability and less warpage.
Improved Surface Finish: Maintaining the right temperature minimizes surface defects such as weld lines, flow marks, and rough textures. This is particularly important for aesthetic parts where surface quality is critical.
Enhanced Mechanical Properties: Proper temperature control ensures uniform crystallinity and molecular orientation in the final product, enhancing its mechanical properties like strength, toughness, and impact resistance.
Reducing Defects with Mould Temperature Controllers
Minimizing Warpage and Shrinkage: Uneven cooling can cause differential shrinkage, leading to warpage. Consistent mould temperature reduces these issues, resulting in parts with better dimensional accuracy.
Preventing Short Shots: Short shots occur when the mould is not filled with plastic. By ensuring optimal flow and fill, mould temperature controllers help prevent this defect.
Avoiding Flash: Flash is the excess material that escapes from the mould cavity. Proper temperature control ensures that the mould closes tightly, reducing the occurrence of flash.
Reducing Burn Marks and Discoloration: Excessive temperatures can cause the plastic to degrade, leading to burn marks and discoloration. Mould temperature controllers help maintain the temperature within the appropriate range to avoid such issues.
Decreasing Cycle Times and Increasing Throughput: Efficient temperature control can reduce the cooling time, thereby decreasing the overall cycle time. This increases the production rate without compromising quality.
Case Studies and Practical Applications
Several industries have reported significant improvements in product quality and reduction in defects by implementing advanced mould temperature controllers. Here are a few examples:
Automotive Industry: In the production of automotive components, precise temperature control has led to parts with better dimensional accuracy and surface finish, reducing the need for post-processing and rework.
Consumer Electronics: Manufacturers of consumer electronics have achieved higher yields and better-quality products by maintaining optimal mould temperatures, resulting in fewer defects and higher customer satisfaction.
Medical Devices: The stringent quality requirements in the medical device industry necessitate precise temperature control. Mould temperature controllers have helped manufacturers produce defect-free and reliable medical components.
Future Trends and Innovations
The field of mould temperature control is continuously evolving with advancements in technology. Some of the emerging trends include:
Smart Controllers: Integration of IoT and AI technologies in mould temperature controllers enables real-time monitoring, predictive maintenance, and adaptive control for enhanced efficiency and precision.
Energy Efficiency: Newer models of mould temperature controllers are designed to be more energy-efficient, reducing overall energy consumption and operational costs.
Advanced Materials: The development of new materials with better thermal conductivity and stability can improve the performance of mould temperature controllers.
Sustainability: Focus on sustainable manufacturing practices is driving the development of mould temperature controllers that minimize waste and environmental impact.
An indispensable tool in the injection molding industry
Mould temperature controllers are indispensable tools in the injection molding industry. By ensuring precise temperature control, they significantly enhance product quality and reduce defects. The benefits include consistent material flow, reduced residual stresses, improved surface finish, and enhanced mechanical properties. Additionally, they help minimize defects such as warpages, short shots, flashes, burn marks, and discoloration. As technology advances, the capabilities of mold temperature controllers will continue to improve, driving further efficiencies and quality enhancements in the manufacturing process.
Implementing advanced mold temperature controllers is a strategic investment for manufacturers aiming to achieve high-quality products, reduce defects, and stay competitive in the market. By understanding and leveraging the benefits of these controllers, manufacturers can optimize their processes and deliver superior products to their customers.
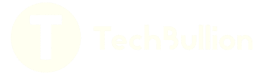