As a preventative measure against potential failures, impact testing is a key component of tool manufacturing, which helps tools meet the demanding requirements of their applications. This testing method assesses tools’ resilience and durability by simulating sudden forces during use. Whether it’s a hammer, wrench, or precision cutting tool, understanding how these tools respond to impacts is crucial for both safety and functionality.
Manufacturers rely on standardized tests, such as the Charpy and Izod impact tests, to measure the energy a tool can absorb before failing. This data not only helps comply with safety regulations but also aids in material selection and product design. As regulatory demands evolve and consumer expectations rise, impact testing becomes even more important. It ensures that every tool manufactured can withstand real-world conditions effectively, preventing tool failures that could lead to injuries or costly damages.
By integrating impact testing into quality assurance protocols, manufacturers can enhance product reliability and maintain consumer trust. In this article, we will discuss how impact testing is used in tool manufacturing in more detail. It highlights its benefits, methodologies, and importance throughout the product lifecycle.
The Basics of Impact Testing in Tool Manufacturing
Impact testing in the tool industry evaluates how well tools absorb and withstand impacts. The procedure involves subjecting tool materials to controlled impact loads that mimic real-life stresses, such as drops, strikes, or other forms of impact that tools might encounter during normal use.
Charpy and Izod impact tests are commonly used in this sector. These tests help determine material toughness – one of the most important factors in tool manufacturing. In the Charpy test, a pendulum hammer strikes a notched specimen to measure the energy absorbed by the material, while the Izod test involves a similar approach but with the specimen mounted vertically. These tests are critical in choosing materials that are cost-effective and robust enough to handle typical stresses without failure.
Such testing not only maintains compliance with international safety standards but also assists in product development and innovation. It allows manufacturers to explore and adopt new materials and design techniques that lead to more durable and efficient tools. Moreover, regular impact testing during the production phase ensures consistent quality and helps in identifying production issues early, thereby reducing waste and improving overall product quality.
Benefits of Impact Testing in Manufacturing Tools
Impact testing offers numerous benefits in tool manufacturing, improving the quality of products and assuring compliance with industry standards. By rigorously applying these tests, manufacturers can ascertain that their tools meet both national and international safety standards, a requirement for market acceptance and consumer safety.
One of the primary benefits of impact testing is its role in quality control. This testing allows manufacturers to identify inconsistencies and potential weaknesses in the material or design before mass production. For instance, if a batch of steel shows lower-than-expected toughness in impact tests, it can be reevaluated or replaced before being fashioned into high-stakes tools like construction equipment or automotive parts. This preemptive approach saves costs by reducing material waste and also prevents tool failures in the field.
Moreover, impact testing is vital for maintaining compliance with industry regulations, which often specify minimum toughness and durability standards. Tools that fail to meet these standards may lead to safety risks, legal repercussions, and damage to the manufacturer’s reputation. By making sure that every tool can withstand significant stress and impact, manufacturers uphold stringent quality standards and reinforce consumer trust in their products.
In addition to regulatory compliance and quality assurance, impact testing also facilitates continuous improvement and innovation within the tool manufacturing industry. The data obtained from these tests provide critical insights that help engineers refine tool designs and develop new materials that are more resilient and efficient. This ongoing innovation is essential for keeping up with market and regulatory demands.
The Importance of Reliable Impact Testing Equipment
In tool manufacturing, selecting the right impact testing equipment is crucial for obtaining accurate and reliable results. The integrity of tools, especially those used in critical applications, hinges not just on the material and design, but also on the quality of testing they undergo. Whether manufacturers opt for drop-weight testing systems or Charpy and Izod impact testers, the choice of equipment must align with the specific needs and standards of the tool being tested.
Impact testing equipment reliability directly affects test results’ quality. This is why the quality of these machines, including their ability to provide precise and repeatable measurements, needs to be high. Poor calibration or a lack of regular maintenance can lead to discrepancies in data, potentially leading to the approval of materials that might fail under operational conditions.
Moreover, the choice of testing equipment also involves considering the latest technological advancements and compliance with current testing standards. Manufacturers must make sure their equipment can adapt to new standards and testing protocols, which can change as new materials and manufacturing techniques evolve. Making sure that testing equipment is up-to-date is necessary for maintaining test results validity and compliance with international safety regulations.
Critical Role of Impact Testing in Tool Manufacturing
Impact testing is a foundational element in tool manufacturing, integral to making sure that tools are not only compliant with safety standards to prevent disasters but also capable of withstanding the rigorous demands of their applications. This method of testing is crucial for assessing tools’ resilience and durability, providing manufacturers with essential data that influences everything from material selection to product design. As industries and regulations evolve, impact testing becomes increasingly important, safeguarding tools’ functionality and safety in diverse working conditions.
By including impact testing in their quality assurance protocols, manufacturers are able to increase the reliability of their products and secure consumer trust. This practice not only meets regulatory demands but also drives innovation, allowing manufacturers to continually improve and adapt their products to satisfy both current and future needs. Furthermore, the consistent application of impact testing throughout the manufacturing process helps identify potential issues early, reducing waste and guaranteeing that every product meets quality standards before it reaches the consumer.
In order to maintain high standards, it is extremely important to choose reliable impact testing equipment from well-known companies. Investing in high-quality testing tools from reputable suppliers guarantees that the equipment will perform as expected, providing accurate and consistent results that are critical for decision-making. This strategic choice supports manufacturers in upholding stringent quality and safety standards, thus improving the overall reliability and performance of their tools on the market.
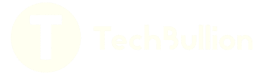