Plasma cutting is one of the most modern effective technologies that allow working with metal, wood, plastic, and stone. It is not surprising that this method is in demand and is actively used in various fields of activity, in housing and communal services, in construction, and industry. The main device in the whole process is a plasma cutter, producing an arc formed by a plasma of enormous temperature.
The arc allows you to work with high accuracy. In this article, we will consider the basic principles on which its operation is built and the best plasma cutter which you can use.
Working Principle
When the operator presses the ignition key, the battery supplies electricity to the plasma torch. This leads to the formation of a primary arc of enormous temperature, which ranges from 6 to 8 thousand degrees.
The formation of an arc between the tip of the electrode and the nozzle happens because it is extremely difficult to achieve this result directly between the workpiece and the electrode. Moreover, this is simply impossible if the work is carried out with a material characterized by insulating properties.
When the primary arc is formed, an air mixture is supplied to it. This air is in contact with it, its temperature and volume are increasing, and the increase can even be a hundredfold. In addition to this, the air loses its dielectric properties and is ionized. Since the nozzle has a narrowing towards its end, the air stream accelerates to 2-3 meters per second and breaks out, having a temperature of almost 30 thousand degrees.
At the moment of contact with the surface, the primary arc fades, and further work is already being carried out due to the newly formed cutting arc. And it melts or burns the material. The cut is smooth since a powerful air stream blows off all particles from the surface. Such a description of how the system works is the simplest and most common.
Areas of Use
Now we can consider where plasma cutting can be used. So, according to jonsguide.org, it is used for the following reasons:
- Operational cutting of large volumes of materials.
- In the case of the manufacture of sheet parts that are characterized by the complexity of geometry, up to the jewelry and instrumentation industries, where maximum compliance with the original drawings is required.
- Installation of metal structures. Plasma cutter eliminates the need for cylinders with compressed oxygen and acetylene, which increases the degree of safety and convenience, especially when it comes to operations at heights.
- Cutting of high-grade steels. In this case, mechanical methods are not suitable. Since the strength of the steels is huge, a tool that can effectively cut sheets based on them will cost a lot and get spoiled very quickly.
Conclusion
It turns out that the scope of plasma cutter use is diverse. Making holes of any configuration in metal sheets, cutting pipes, corners, and workpieces of a different cross-section, processing the edges of forged products to weld metal and close its structure, etc. can be done with the help of a plasma cutter.
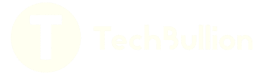