In the rapidly evolving landscape of manufacturing technologies, 3D printing and injection molding stand out as two powerful methodologies. While each has its unique strengths, their combined use can significantly enhance production processes. This article explores how 3D printing complements injection molding, highlighting the benefits and applications of integrating these technologies.
Accelerating Prototyping
Prototyping is a critical phase in product development, and the synergy between 3D printing and injection molding can revolutionize this process.
Rapid Iteration
3D printing enables rapid iteration by allowing designers to quickly create and test design prototypes. This capability is essential before committing to the costly and time-consuming process of creating a 3D print injection mold. With 3D printed prototypes, manufacturers can refine designs, identify flaws, and make necessary adjustments in a fraction of the time traditionally required.
Cost Efficiency
Utilizing 3D printing for functional prototypes significantly reduces expenses. Instead of investing in full-scale molds for each design iteration, 3D printing allows for the creation of detailed, functional prototypes at a lower cost. This not only speeds up the development process but also conserves resources, making it a cost-efficient solution for prototyping, especially before producing a 3D print injection mold.
Enhancing Mold Making
The mold-making process, essential for injection molding, can be greatly enhanced by incorporating 3D printing technology.
Complex Mold Inserts
One of the standout advantages of 3D printing is its ability to produce complex mold inserts. Traditional machining processes often struggle with intricate designs and detailed geometries. 3D printing, however, can effortlessly create these complex components, enhancing the functionality and precision of the final molds. This capability is particularly beneficial in creating a 3D print injection mold that meets exact specifications.
Reduced Lead Time
Incorporating 3D printed parts into mold-making can drastically reduce lead times. The traditional approach to mold production can be slow and labor-intensive. By using 3D printing for specific parts of the mold, manufacturers can expedite the process, delivering molds faster and accelerating the overall production timeline. This efficiency is especially evident when creating a 3D print injection mold.
Supporting Small Batch Production
For many manufacturers, small batch production presents unique challenges that 3D printing and injection molding can address effectively.
Low-Volume Runs
3D printing is particularly advantageous for low-volume production runs where traditional injection molding is not cost-effective. The ability to produce small quantities of parts without the need for extensive mold retooling makes 3D printing an ideal solution for bespoke and limited edition products. This flexibility is key when considering 3D printed injection mold tooling for short production runs.
Flexible Production
The flexibility of 3D printing enables manufacturers to switch designs quickly and efficiently. Unlike traditional molding, which requires significant retooling, 3D printing allows for seamless transitions between different product designs. This flexibility is crucial for industries that demand frequent updates and customizations, making 3D printed injection mold tooling an invaluable resource.
Enabling Design Flexibility
Design flexibility is a cornerstone of innovative manufacturing, and the combination of 3D printing and injection molding offers unparalleled opportunities in this area.
Custom and Complex Designs
3D printing empowers manufacturers to achieve higher levels of customization and complexity in product designs. Traditional injection molding often imposes design limitations due to the constraints of mold fabrication. With 3D printing, these constraints are minimized, enabling the creation of intricate and unique designs that meet specific customer needs. This is particularly important in the context of a 3D print injection mold, where precision and customization are paramount.
Iterative Testing
Continuous refinement and testing of designs are vital to ensuring optimal performance and manufacturability. 3D printing facilitates iterative testing by allowing quick production and assessment of design variations. This iterative approach ensures that the final product is both high-quality and manufacturable, reducing the risk of costly post-production adjustments. The ability to iteratively test and refine designs is a significant advantage when developing a 3D print injection mold.
Conclusion
The integration of 3D printing with injection molding represents a significant advancement in manufacturing technology. By accelerating prototyping, enhancing mold-making, supporting small batch production, and enabling design flexibility, 3D printing complements and enhances traditional injection molding processes. Companies like HordRT, with their expertise in plastic injection molding, are at the forefront of leveraging these technologies to deliver superior products and services.
The use of 3D printing and injection molding in tandem can transform the manufacturing landscape. The efficiency, cost savings, and design flexibility offered by combining these technologies enable manufacturers to meet the demands of modern production with greater agility and precision. As the industry continues to evolve, the role of 3D printed injection mold tooling will undoubtedly become even more pivotal.
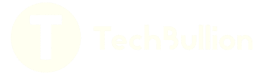