Maintaining and Servicing Brewery Equipment: A Comprehensive Guide
The success of a brewery hinges not only on the quality of its ingredients and recipes but also on the meticulous maintenance and servicing of its equipment. Regular upkeep ensures operational efficiency, product consistency, and compliance with safety standards. This article outlines the key practices and considerations for maintaining and servicing brewery equipment.
- Establishing a Maintenance Schedule
Regular maintenance is critical to preventing equipment breakdowns and ensuring smooth operations. Breweries should establish a detailed maintenance schedule that includes:
Daily Inspections: Check for any visible signs of wear and tear, leaks, or malfunctions. Ensure all equipment is clean and functioning correctly.
Weekly Maintenance: Perform more thorough checks, including lubrication of moving parts, inspection of seals and gaskets, and cleaning of heat exchangers.
Monthly Servicing: Conduct comprehensive inspections of all major equipment. This includes checking electrical connections, calibrating sensors and instruments, and verifying the performance of pumps and motors.
Annual Overhaul: Schedule a complete overhaul of critical equipment, such as fermenters, mash tuns, and packaging lines. This may involve disassembly, deep cleaning, and replacement of worn parts.
- Cleaning and Sanitation
Proper cleaning and sanitation are paramount in a brewery to prevent contamination and ensure product quality:
CIP (Clean-in-Place) Systems: Use automated CIP systems for tanks and pipelines to ensure thorough cleaning without disassembling equipment. This involves circulating cleaning solutions, rinsing with water, and sanitizing with appropriate chemicals.
Manual Cleaning: Some equipment and surfaces may require manual scrubbing and sanitizing. Use food-grade cleaning agents and follow manufacturer recommendations for each piece of equipment.
Routine Sanitization: Regularly sanitize hoses, valves, and fittings that come into contact with beer to prevent microbial growth. Ensure that cleaning schedules are strictly followed to maintain hygiene.
- Monitoring and Diagnostics
Utilizing monitoring and diagnostic tools helps detect potential issues before they escalate:
Sensors and Alarms: Install sensors to monitor critical parameters such as temperature, pressure, and flow rates. Alarms can alert operators to deviations from normal operating conditions.
Data Logging: Use data logging systems to track equipment performance over time. Analyzing this data can identify trends and predict when maintenance is needed.
Vibration Analysis: Regularly conduct vibration analysis on pumps and motors to detect imbalances or bearing wear, which can indicate potential failures.
- Training and Documentation
Well-trained staff and thorough documentation are essential for effective maintenance:
Staff Training: Provide comprehensive training for staff on equipment operation, maintenance procedures, and troubleshooting techniques. Ensure they understand the importance of regular maintenance and proper cleaning practices.
Maintenance Logs: Maintain detailed logs of all maintenance activities, including inspections, repairs, and replacements. This documentation helps track the history of each piece of equipment and can aid in diagnosing recurring issues.
- Working with Equipment Manufacturers
Collaboration with equipment manufacturers can enhance maintenance efforts:
Manufacturer Guidelines: Follow the maintenance guidelines provided by equipment manufacturers. These guidelines are tailored to the specific needs of the equipment and can help extend its lifespan.
Service Contracts: Consider entering into service contracts with manufacturers or authorized service providers. Regular professional servicing can prevent major breakdowns and ensure that equipment operates at peak efficiency.
Spare Parts Inventory: Maintain an inventory of critical spare parts, as recommended by manufacturers. Having these parts on hand can minimize downtime during repairs.
- Preventive Maintenance
Preventive maintenance is about addressing potential issues before they cause problems:
Lubrication: Regularly lubricate bearings, gears, and other moving parts to reduce friction and wear.
Seal and Gasket Inspection: Check seals and gaskets for wear and replace them as needed to prevent leaks.
Calibration: Periodically calibrate instruments and sensors to ensure accurate measurements and control.
- Troubleshooting and Repairs
Even with regular maintenance, occasional breakdowns may occur:
Troubleshooting Protocols: Develop standardized troubleshooting protocols to diagnose and address common issues quickly. Ensure staff are familiar with these protocols.
Rapid Response: Implement a rapid response plan for equipment failures to minimize downtime. This includes having skilled technicians on call and a supply of essential spare parts.
Outsourcing Repairs: For complex repairs, consider outsourcing to specialized technicians or the equipment manufacturer. This can ensure that repairs are done correctly and efficiently.
Conclusion
Maintaining and servicing brewery equipment is an ongoing process that requires diligence, expertise, and strategic planning. By establishing a comprehensive maintenance schedule, ensuring proper cleaning and sanitation, leveraging monitoring tools, and collaborating with manufacturers, breweries can optimize their operations and produce high-quality beer consistently. Investing in regular maintenance not only extends the lifespan of the equipment but also safeguards the brewery’s reputation and profitability.
Micet equipment:brewery equipment
Read More From Techbullion
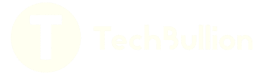