Designing Brewery Layouts for Efficiency: Key Considerations and Best Practices
Designing an efficient brewery layout is critical to optimizing production, ensuring safety, and maintaining the quality of the beer. A well-thought-out layout minimizes wasted time and resources, streamlines operations, and can significantly impact the overall success of the brewery. This article outlines key considerations and best practices for designing a brewery layout that promotes efficiency.
- Understanding the Brewing Process
Before designing the layout, it’s essential to have a thorough understanding of the brewing process. This involves several key stages:
Raw Material Storage: Receiving and storing malt, hops, yeast, and other ingredients.
Milling: Grinding the malt to prepare it for mashing.
Mashing and Lautering: Mixing milled malt with water and separating the wort.
Boiling: Boiling the wort and adding hops.
Cooling: Rapidly cooling the wort to fermentation temperature.
Fermentation: Allowing yeast to ferment the wort into beer.
Conditioning: Aging the beer to develop flavors.
Packaging: Bottling, canning, or kegging the finished product.
Storage and Distribution: Storing packaged beer and preparing it for shipment.
Each stage has specific requirements and spatial needs, which should be considered in the layout.
- Workflow Optimization
An efficient layout minimizes the distance and effort required to move materials and products through the brewing process. Consider the following strategies:
Linear Workflow: Arrange equipment in a linear sequence that follows the brewing process, reducing backtracking and cross-traffic.
Zoning: Create dedicated zones for different activities (e.g., brewing, fermentation, packaging) to prevent contamination and streamline operations.
Accessibility: Ensure that all equipment is easily accessible for maintenance and operation. This includes providing adequate space around tanks, vessels, and other machinery.
Flow of Raw Materials and Finished Products: Design separate paths for incoming raw materials and outgoing finished products to prevent bottlenecks and contamination.
- Space Utilization
Effective use of space is crucial, especially in breweries with limited square footage:
Vertical Space: Utilize vertical space by installing tall fermenters and stacking storage areas. Mezzanine levels can house smaller equipment or additional storage.
Flexible Spaces: Design flexible spaces that can be reconfigured as production needs change. Modular equipment and movable partitions can help adapt to varying production volumes.
Compact Layouts: For smaller breweries, a compact layout that minimizes the distance between different stages of production can improve efficiency.
- Safety and Compliance
Safety is a paramount consideration in brewery design. Ensure compliance with local health and safety regulations by incorporating the following:
Clear Pathways: Maintain clear and wide pathways for safe movement of personnel and equipment.
Emergency Exits: Designate and mark emergency exits that are easily accessible from all areas of the brewery.
Ventilation: Install proper ventilation systems to handle steam, heat, and carbon dioxide produced during brewing.
Hazard Zones: Clearly mark and isolate hazardous areas, such as those with hot surfaces or chemical storage, to protect workers.
- Utilities and Infrastructure
Efficient utility management is critical to brewery operations:
Water Supply and Drainage: Ensure an adequate supply of clean water and efficient drainage systems to handle large volumes of wastewater.
Power Supply: Design a robust electrical system to support heavy machinery and brewing equipment.Commercial Brewing Equipment
Cooling Systems: Implement effective cooling systems, such as glycol chillers, to maintain precise temperature control during fermentation and storage.
Waste Management: Plan for the proper disposal of spent grains, yeast, and other waste products to maintain cleanliness and sustainability.
- Technology Integration
Modern breweries leverage technology to enhance efficiency:
Automation: Incorporate automated systems for tasks such as milling, mashing, and packaging to reduce manual labor and increase consistency.
Monitoring Systems: Install sensors and monitoring systems to track key parameters like temperature, pressure, and fermentation progress in real-time.
Software Solutions: Use brewery management software to streamline inventory management, production scheduling, and quality control.
- Scalability and Future Expansion
Design the layout with future growth in mind:
Modular Design: Opt for modular equipment that can be easily expanded or upgraded.
Space for Expansion: Allocate space for additional tanks, packaging lines, or storage areas to accommodate future increases in production capacity.
Infrastructure Readiness: Ensure that utilities and infrastructure can support future expansions without requiring major overhauls.
Conclusion
Designing an efficient brewery layout is a complex task that requires careful planning and consideration of various factors. By optimizing workflow, utilizing space effectively, ensuring safety, managing utilities, integrating technology, and planning for future growth, breweries can create layouts that enhance productivity and support long-term success. An efficient layout not only improves operational efficiency but also contributes to producing high-quality beer consistently, ultimately satisfying both the brewery team and its customers.
Micet equipment:brewery equipment
Read More From Techbullion
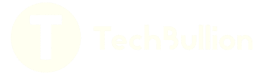