In industrial manufacturing, accuracy and speed are essential for success. Every second counts whether you are turning out electronic products, car parts, or packaging materials. Every cut counts.
If your company is involved in mass production or involves large systems, this article will show the way to improve efficiency and cut waste.
What Is Die Cutting and How Does It Work?
The technique can be achieved with steel-rule dies, rotary tools, or even by using laser cutting, according to the material and volume involved.
Improve Production Quality
An uneven edge or an error in proportion can result from hand cutting or manual processing, especially with large-scale operations. Die cutting services eliminate such uncertainties by following a predetermined template for every cut. That does wonders for production quality.
When parts need to fit tightly together or meet precision design requirements, this degree of consistency is indispensable. With reliable services, you sidestep the need for rework and prevent costly flaws in production.
Increased Speed and Volume
Once the die is made and the machine is set up, thousands of identical parts can be made. Because of this, it is an excellent choice for manufacturers who need to speed up their production to meet production deadlines or to increase their scale. There is the potential to save both time and money by outsourcing this process if your production line is dependent on high efficiency.
Versatility Across Materials and Industries
Whether it’s thin plastic films, thick foam, flexible fabrics, or rigid metal sheets, there is a cutting method to suit your needs.
The versatility and precision of die cutting make it an indispensable tool for a variety of industries, including the medical manufacturing sector. But it is also used in industries with high demands, such as gaskets, seals, insulation panels, and device parts.
Less Waste and Better Use of Materials
Any material that’s wasted will do nothing more than cost you money in production. When die cutting is used to make parts, this no longer needs to happen.
Dies are designed in keeping with exact part specifications, so there’s little excess left over when parts are trimmed out. Not only does this save money on materials, but it also reduces disposal and storage requirements.
Clean Edges and Professional Finish
When the appearance is important—such as with packaging inserts or visible hardware—die cutting produces a professional setup appearance. The tools’ sharpness and the process’s precision yield smooth edges and even surfaces that need no treatment. This technique saves time during final assembly and also adds a more polished feel to your finished product.
Customisation for Unique Designs
Would you like a shape that is not standard or a custom pattern? Die-cutting services can do that. You can work with suppliers to build a die set that meets your precise dimensions, hole locations, and material requirements. This kind of flexibility makes the process suitable for short production runs of niche items as much as for long ones that are complex and detailed.
A Smarter Way to Scale
At speeds and with accuracy machines cannot achieve, die-cutting technology combines both into one amazing product.
When you are working with your trusty partner, the same materials, less waste, and a harmonious line from better design to finished product are almost guaranteed every time you design.
To that end, die-cutting might be your lucky break and a place where you could consider investing effort.
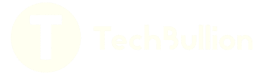