Artificial intelligence (AI) and advanced automation are rapidly reshaping metal fabrication and CNC machining. In today’s smart manufacturing environment, “AI in manufacturing” means using machine learning, data analytics, and robotics on the shop floor – from self-optimizing CNC machines to automated welding cells. These systems learn from sensors and CAD/CAM data to improve cutting paths, schedule maintenance, and catch defects, all with minimal human intervention. The impact is already clear: one industry survey found 70% of metal manufacturers have adopted AI, and 82% plan to increase AI investment in coming years. In short, AI-driven manufacturing is making metalshops faster, more precise, and more efficient.
Core Value
AI and automation deliver real, quantifiable benefits in metalworking. For example, data show major gains in throughput, quality, uptime, and cost savings:
- Higher Productivity: Smart machines crank out more parts. In surveys, about 72% of fabricators report productivity increases after adopting AI-driven systems. AI-optimized CNC scheduling and path planning can raise throughput roughly 15–20% (one report notes ~18% higher sheet-metal output). In practice, intelligent machine tending and robotic automation create “lights-out” cell operations that run 24/7, vastly expanding output without adding staff.
- Maximized Uptime: Predictive maintenance is a game-changer. By analyzing vibration and tool-wear data, AI systems predict failures before they happen, cutting unplanned downtime by up to 30%. This boosts overall equipment effectiveness (OEE) – a recent study found OEE rises ~14% on average when AI is applied to fabrication lines. In short, machines run longer and more reliably, so production stays on schedule.
- Superior Quality: Automated inspection and precision control slash defects. AI-powered vision systems detect flaws at about 98% accuracy– far higher than manual inspection – so scrap rates fall. Likewise, AI-guided processes (like robotic welding or laser cutting) improve part accuracy. For instance, robotic welding with AI can achieve ~25% greater precision than manual welding. Smarter CAD/CAM algorithms also help optimize cutting layouts, trimming material waste (some sources report 15–25% scrap reduction with AI tools). The result: higher first-pass yield and tighter tolerances on metal parts.
- Cost & Waste Reduction: By automating repetitive tasks, shops cut labor and operating costs. Studies show metal fabricators using AI can reduce labor expenses by about 10%. With AI controlling feed rates and cutting speeds, material use drops – reports cite up to 15% less waste and as much as 10% energy savings. Altogether, these efficiencies translate into significant cost savings in scrap, labor, and utilities.
- Safer, Smarter Workflows: Automation tackles dangerous or tedious jobs. Robots handle tasks like MIG/TIG welding or heavy lifting, so workers avoid hazards and can focus on programming or quality work. In fact, about 62% of metal shops report improved safety metrics after AI implementation. Smarter scheduling also gives flexibility: shops can run multiple machines with fewer operators. New AI-based training tools mean workers upskill faster, further multiplying the value of automation.
Together, these advantages form the core value proposition: AI-driven CNC parts and fabrication systems boost throughput and quality while lowering downtime, defects, and costs.
Data Proof
These gains aren’t just theory – real-world cases and industry surveys back them up:
- Raymath (Ohio, USA): This metal fabricator installed collaborative welding robots for MIG and TIG welding (from Universal Robots/THG). The result was dramatic: welding speed doubled (cobots weld twice as fast as manual), yielding a 4× improvement in welding output, even with half the operators. For CNC, adding robot “tenders” to two Hurco mills enabled true lights-out machining. Raymath reports a 600% boost in CNC throughput (they get six times more hours of machining with the same workforce). All this was achieved with a payback under one year. Raymath’s case shows that AI/robotics can multiply fabricator capacity and quickly return on investment.
- Great Lakes Stainless (Michigan, USA):
Confronting a labor and time challenge, this custom fabricator automated a complex weld with a FANUC CRX cobot and LightWELD laser. A part that took 3 hours of manual welding was done in 15 minutes – a 95% cycle-time reduction. The automated welds had a smoother finish, and output soared. The freed-up welders moved to other tasks. This real-life case underscores the throughput and quality gains possible: cutting cycle time by an order of magnitude while enhancing weld consistency.
- Nexlam (Italy): A sheet-metal fab partnered with Roboteco-Italargon to add an AI-driven welding cell (their GWP system). The AI software analyzes CAD models and automatically programs optimal weld sequences. Nexlam reports “improved weld quality and greater efficiency with a smoother workflow” thanks to this AI-enabled solution. Essentially, even a small shop cut programming time and got better, more consistent welds by letting AI generate and adjust the robot instructions.
- Industry Surveys and Reports: Data from broader studies align with these cases. For instance, an Advanced Manufacturing Outlook survey found 47% of companies saw higher product quality and 43% reported increased throughput after adopting Industry 4.0 technologies. Another recent report notes that over 65% of metal fabrication firms are planning AI adoption within five years. These numbers match the case studies: most fabricators expect AI to improve efficiency, quality, and competitiveness. For example, 72% of shops already report productivity gains from AI, and 55–60% believe AI gives them a strategic edge in the marketplace.
- Advanced CNC Market Trends: Analysts forecast the CNC industry will continue growing. The global CNC market is expected to expand at ~9.5% CAGR through 2030 (from $6.2B in 2023 to ~$11.7B by 2030) driven by automation. Crucially, vendors are integrating AI and IoT into controls – smart CNC machines will soon optimize toolpaths on-the-fly, adapt to wear, and schedule maintenance autonomously. Reports highlight that embedding AI/ML in CNC enhances adaptability and uptime. All of this confirms that both the market and user surveys support the value of AI in metal machining.
In sum, both on-the-shop-floor case studies and industry-wide data paint a consistent picture: AI and automation deliver measurable benefits in metal fabrication and CNC machining.
Future Outlook
Looking ahead 5–10 years, AI and automation will deepen their impact on metalworking. Industry experts project explosive growth: the overall AI-in-manufacturing market is forecast to surge (Capgemini and market reports predict multi–billion-dollar markets by 2030), and the AI in metal fabrication segment alone should grow at ~12% per year. We expect several key trends:
- Autonomous CNC & Robotics: Machines will get smarter. CNC controllers will embed machine learning to adjust feeds/speeds in real time, based on sensor feedback. Robots will use advanced vision and force control to handle more complex tasks (multi-axis welding, adaptive bending, etc.) without reprogramming. Collaborative robots (cobots) will continue expanding into welding, cutting, and material handling, making automation accessible even for low- to mid-volume jobs. IFR data already shows robotics installations climbing, and by 2024 we expect ~600,000 industrial robots installed annually worldwide.
- Digital Twins & Data Analytics:
More shops will build “digital twins” of their machines and processes. Real-time data streams from CNCs and fab equipment, fed into cloud-based AI models, will simulate and optimize the workflow. This means predictive maintenance getting even better (machines self-diagnose issues) and process optimization becoming routine. Manufacturers will use AI-driven analytics to shorten new product ramp-up times – for example, reducing setup or prototyping by ~20–35% using simulation.
- Generative Design & Customization: AI-driven design tools will automatically generate optimized part geometries and manufacturing plans for metal components. This complements trends in mass customization: shops will quickly reconfigure their CNC and automation cells to new designs without extensive reprogramming. Enhanced connectivity (5G, IIoT) will allow remote monitoring and even remote operation of machines, breaking old factory boundaries.
- Sustainability & Efficiency: Environmental concerns will drive AI use. Expect AI to optimize energy use (one study projects ~10% energy savings) and raw material usage, cutting carbon footprints. AI-guided sorting and recycling (already improving metal purity by ~18%) will become common in fabrication shops. Overall, “green manufacturing” will leverage AI to meet tighter regulations and corporate sustainability goals.
- Workforce Evolution: The role of human workers will shift. While some manual tasks will vanish, new high-skill jobs will emerge. Most current metal engineers already see this coming (82% say AI is essential to future innovation). Over the next decade, training programs will integrate AI tools, and operators will need data literacy. We may also see increased use of AI for scheduling and training (e.g. virtual reality training modules already show ~25% faster competency gains).
- Challenges & Integration: There will be hurdles too. SMEs may face cost and integration challenges initially, though those costs are dropping. Cybersecurity will become vital as machines connect. Data management and interoperability (legacy CNCs vs. new systems) remain issues. Nevertheless, many believe these challenges will be solved as standards improve and vendors offer turnkey AI solutions (for example, persistent collaborations between AI firms and traditional machine-tool companies).
Overall, the trend is clear: the next decade will solidify smart manufacturing in metalworking. CNC machining and fabrication plants will be increasingly autonomous, adaptive, and interconnected. As one market report notes, advanced AI algorithms in CNC will optimize every cut and predict maintenance automatically – a foretaste of the factory floors to come.
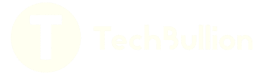