In an industry that thrives on innovation, the rapid evolution of robotics technology is redefining manufacturing standards. Among these advancements, collaborative robots, or “cobots,” stand out as a transformative force in the manufacturing sector. These smart, flexible, and often autonomous machines work side-by-side with human workers, enhancing productivity and reimagining traditional operational processes. But the innovation doesn’t end there. The emergent trend of “servitization” is setting the stage for a further revolution, particularly in how cobots are offered to customers.
Servitization in the context of cobots isn’t just a buzzword; it’s a dynamic shift from selling products to delivering comprehensive services. This model, commonly known as Robot-as-a-Service (RaaS), takes inspiration from the digital transformation strategies that have reshaped sectors like entertainment and software, where services are subscribed to rather than purchased.
By adopting the RaaS model, manufacturers encapsulate cobots within a full suite of services that may include installation, routine maintenance, on-site training, software updates, and data analysis to optimize the robots’ performance. This paradigm shift is advantageous but brings its complexities, primarily related to the management of numerous tailored service contracts, each reflecting different customer needs, pricing models, and operational metrics.
That’s where advanced service contract management solutions play a pivotal role. Imagine a platform that functions much like a highly efficient digital assistant, dedicated to the creation, customization, pricing, quoting, and monitoring of a wide array of service contracts. Such system not only simplifies administrative workflows but also revolutionizes customer service by offering transparency and customization, streamlining the quoting process, and ensuring clients understand the scope of services they’re subscribing to.
Moreover, an effective service contract management solution can be a boon for cost control. By enhancing efficiency, such solutions allow manufacturers to focus on core competencies: developing superior cobots and ensuring the provision of high-value services. However, the successful integration of such system requires careful consideration. It must align with the manufacturer’s strategic goals, be intuitive for users, integrate seamlessly with existing operational software, and possess robust analytics and risk management features.
Training and user adoption are also fundamental to leverage these solutions effectively. An intuitive system minimizes the learning curve for staff, enabling them to harness its full potential swiftly, thereby enhancing operational efficiency rather than complicating processes. Nevertheless, adopting servitization and a suitable contract management solution is not a “set-and-forget” strategy. Continuous performance review is essential. Manufacturers must stay attuned to service contract performance metrics and customer feedback, ensuring that the provided services remain relevant, competitive, and value-generating for the customers.
All in all, the journey of cobots in manufacturing is stepping into an exciting new phase with servitization. It’s a mutually beneficial evolution; manufacturers enjoy sustained revenue and deeper customer engagement, while customers receive an all-encompassing, high-value service experience. As this trend gains traction, the manufacturing landscape will witness standards not just being met but redefined, with service contract management solutions illuminating the path forward. In this dynamic environment, those who adapt, innovate, and maintain a customer-centric approach will lead the charge into a future where cobots are central to manufacturing success.
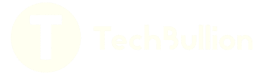