Abstract: Aluminum castings play a pivotal role in modern industry, with increasingly stringent quality requirements, ranging from automotive components to aerospace assemblies. However, various internal and surface defects in castings are often the primary cause of low yields, and the root of these defects can often be traced back to non-metallic inclusions mixed in the molten aluminum. As a professional glass fiber filter manufacturer, we deeply understand these industry pain points. This article will delve into how high-silica fiberglass mesh, as a highly efficient molten aluminum filtration solution, can significantly increase the yield of aluminum castings through its unique operating principles and superior properties, bringing a revolutionary change to the casting industry.
Part 1: Understanding the Challenges of Aluminum Casting Yields
Aluminum alloys, with their properties of lightweight, high strength, and excellent mechanical properties, are widely used in various fields. However, during the casting process, due to a variety of factors such as impure charge material, improper melting operations, tool wear, and environmental contamination, large quantities of non-metallic inclusions inevitably occur in the molten aluminum, such as oxides (especially Al₂O₃), dross, carbides, etc. These tiny impurities may seem insignificant, but they can cause a series of fatal defects during the solidification of the casting:
- Non-metallic Inclusions: These are the primary source of internal defects in castings, which can destroy the continuity of the metal matrix, lead to stress concentration, and thus significantly reduce the mechanical properties of castings, such as tensile strength, fatigue strength, and elongation. At the same time, inclusions form defects on the surface of the casting, affecting appearance and subsequent processing.
- Porosity: Inclusions often become favorable sites for gas bubble nucleation, leading to porosity defects inside the casting, further weakening mechanical properties and sealing performance.
- Shrinkage Defects: Although primarily caused by solidification shrinkage, inclusions can impede the effective feeding of liquid metal, exacerbating the formation of shrinkage cavities and porosity.
These defects directly lead to an increase in the rejection rate and rework rate of aluminum castings, which in turn increases production costs, prolongs the production cycle, and ultimately affects product competitiveness in the market, customer satisfaction, and brand reputation. Therefore, finding an efficient and reliable molten metal purification solution is key to improving casting yield and achieving sustainable development.
Part 2: Working Principles and Superior Properties of High-Silica Fiberglass Mesh
Facing the challenges of casting defects, high silica fiberglass mesh filter has emerged as an innovator in the field of molten aluminum filtration. Its superior performance stems from its unique material composition and precise purification mechanism.
Revealing Material Properties: The Unique Advantages of High Silica
The core of high-silica fiberglass mesh lies in its high purity silica content, reaching up to 96% SiO₂. This high purity bestows it with unparalleled properties:
- Exceptional High-Temperature Resistance: Our high-silica fiberglass mesh can operate continuously at 1000°C, with an astonishing softening point of 1700°C. This means it can maintain structural integrity and filtration efficiency in the red-hot molten aluminum environment without softening, deforming, or decomposing, ensuring a stable and reliable filtration process.
- Ideal Thermal Expansion Match: With a thermal expansion coefficient of 0.55×10⁻⁶/°C, our filters exhibit thermal expansion characteristics that closely match those of molten aluminum. This excellent match minimizes stress and cracking due to thermal stress differences during rapid temperature changes, making it outstanding even in continuous casting or under thermal shock, having demonstrated zero deformation after 12 hours of continuous pouring tests.
- Excellent Chemical Stability: The high-purity SiO₂ material ensures that the fiberglass mesh exhibits extremely strong chemical inertness when it comes into contact with molten aluminum, without reacting at all with the molten aluminum. This means it will not introduce secondary contamination or alter the chemical composition of the molten aluminum, thereby guaranteeing the maximum purity of the final casting.
- Extremely Low Gas Emission: Our filters guarantee a gas emission of ≤ 30 cm³/3g, which helps reduce the formation of porosity defects and further improves casting quality.
Detailed Analysis of the Triple Purification Mechanism
The reason why high-silica fiberglass mesh can reduce the casting defect rate by 90% lies in its unique triple purification mechanism, far surpassing traditional filtration methods:
- Mechanical Sieving: This is the most direct filtration method. The precise pore size of the fiberglass mesh can physically intercept large particulate inclusions in the molten metal, such as dross, refractory fragments, etc., preventing them from entering the casting.
- Deep-Bed Adsorption: The complex three-dimensional structure inside the fiberglass mesh forms a deep filtration bed. When the molten metal flows through, fine inclusions will come into contact with the fiber surface and be adsorbed and adhered to the fibers, allowing them to be effectively captured even if their size is smaller than the mesh openings.
- Electrostatic Capture: This is the unique advantage of high-silica fiberglass mesh. During the molten metal flow, static electricity is generated between inclusions and the fiber surface. Utilizing this charge difference, the filter can actively capture and adsorb charged tiny particles, including some extremely difficult-to-remove sub-micron contaminants. This mechanism is particularly effective for capturing 5-50μm Al₂O₃ clusters.
Part 3: How High-Silica Fiberglass Mesh Directly Boosts Aluminum Casting Yields
High-silica fiberglass mesh, with its powerful filtration capabilities, directly and significantly improves the yield of aluminum castings, bringing tangible benefits to casting production:
- Improved Purity of Molten Aluminum: The filter can effectively remove micron-sized inclusions of 5 – 50μm in the molten aluminum, especially aluminum oxide (Al₂O₃) clusters. These inclusions are important nucleation sites for the formation of pores and shrinkage cavities. By reducing these inclusions, the filter fundamentally reduces the incidence of internal defects in the casting, resulting in a denser and more uniform casting structure.
- Optimization of Casting Quality Indicators:
- Improved Surface Finish: Removing inclusions near the surface reduces pits, spots, and roughness on the casting surface, lowering the cost and time of subsequent grinding and finishing.
- Enhanced Mechanical Properties: The reduction of internal defects directly improves key mechanical properties of the casting, such as tensile strength, yield strength, fatigue strength, impact toughness, and elongation, ensuring that the product meets more stringent performance requirements.
- Improved Metallurgical Structure: Pure molten metal is conducive to grain refinement and uniform distribution, improving the metallurgical structure of the casting and further enhancing its overall performance.
- Practical Benefits and Cost Savings:
- Reduced Scrap Rate: Reducing casting rejects due to defects is the most direct manifestation of yield improvement, as our filters can reduce the defect rate by 90%.
- Reduced Rework and Machining Loss: A higher initial pass rate for castings means less repair work, less material waste, shorter production cycles, and increased overall production efficiency.
- Increased Production Efficiency: Ensures stable and smooth flow of molten metal, reducing production interruptions caused by impurities blocking gates, guaranteeing continuous production.
- High Recovery Rate: The high purity of the filtered molten metal results in a casting recovery rate of over 95%, further reducing material costs.
Part 4: Selecting the Right High Silica Fiberglass Mesh Product
To maximize the benefits of high-silica fiberglass mesh, it is crucial to select the product suitable for your specific application.
- Selection of Different Precision Grades:
- Coarse Filtration (3.0mm mesh): Primarily designed to capture dross and larger impurities over 500μm, serving as a crucial primary cleaning stage in the casting process.
- Precision Filtration (0.8mm mesh): Specifically designed to trap 5-50μm Al₂O₃ clusters and other fine impurities. This level of precision filtration is essential for aerospace castings and other applications with extremely high purity requirements.
- We also offer custom weaving services, allowing us to tailor filter precision to your exact specifications and most demanding molten metal filtration needs.
- Advantages of the Cap Filter:
- Innovative Design: Our cap filters feature a unique “cap” design that simplifies the gating system, reduces secondary oxidation of molten metal during pouring, and provides an efficient, stable, and superior filtration experience.
- Highly Customizable: Cap filters are available with options for with or without a base, and with or without a cap cover, to adapt to different gating system structures and filtration needs, achieving more precise filtration.
- Installation and Compatibility:
- Our filters are designed with practicality in mind, are easy to install, and can be seamlessly integrated with existing molding equipment, without the need for extensive modifications to the current production line.
Conclusion
In today’s pursuit of excellent casting quality and higher production efficiency, high-silica fiberglass mesh has become an indispensable tool in the modern aluminum casting industry. With its exceptional high-temperature resistance, chemical inertness, and revolutionary triple purification mechanism, it fundamentally solves the problem of defects caused by inclusions in molten aluminum. By significantly improving the purity of molten aluminum, optimizing the mechanical properties and surface finish of castings, and bringing considerable economic benefits (such as reduced scrap rates, decreased rework, and increased recovery rates), high-silica fiberglass mesh is undoubtedly the key secret to increasing aluminum casting yield.
We firmly believe that actively embracing and adopting advanced filtration technologies, such as high-silica fiberglass mesh, is a wise decision for foundry enterprises to stand out in an increasingly demanding market with growing quality challenges.
Call to Action: Contact us today to learn more about high-silica fiberglass mesh, or request a free sample to experience firsthand how our products can improve your casting quality, significantly reduce casting defects, and substantially boost the production efficiency of your molten aluminum filtration operations!
About Explorer Company
Explorer Company, as an innovative enterprise focused on advanced material solutions, is committed to providing high-quality molten metal filtration products to the global casting industry. With deep expertise and continuous technological investment, we have developed a series of high-performance high-silica fiberglass filter mesh products, including filters of various shapes and precision grades, designed to help customers solve the most complex filtration challenges, improve product quality, and optimize production efficiency. We believe that the combination of excellent material performance and precise filtration technology is the cornerstone for driving the casting industry towards higher standards.
Read More From Techbullion
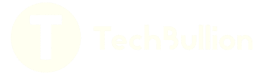